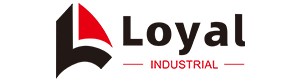
- Shandong Loyal Industrial Co.,Ltd.
- Macaroni Production Machine Instant Noodle Machine Biscuit Making Machine

Home> Company News> Fully Automatic Kurkure Factory: The Future of High-Efficiency Snack Production

Fully Automatic Kurkure Factory: The Future of High-Efficiency Snack Production
2024-11-22 17:00:02Introduction
Theindustry has experienced remarkable growth over the past few decades, driven by increasing global demand for snacks that combine taste, texture, and convenience. As consumer preferences evolve, manufacturers are seeking innovative solutions to meet market demands while maintaining operational efficiency and sustainability. Fully automatic Kurkure factories represent a transformative leap forward, enabling snack producers to deliver consistent quality at an unprecedented scale.
Automation in snack production has become a cornerstone for success in the competitive food manufacturing sector. According to food technology expert Dr. Elaine Roberts, "Automation is no longer a luxury for the snack industry—it's a necessity to stay ahead of market trends while achieving efficiency and quality." Fully automated systems not only streamline production but also reduce labor costs, minimize human error, and enhance food safety standards.
A fully automatic Kurkure factory integrates cutting-edge technology to deliver a range of benefits for manufacturers. From precision engineering to energy-efficient operations, these systems are tailored to optimize every aspect of snack production. This article explores how such factories are shaping the future of high-efficiency snack production, revolutionizing the way Kurkure snacks are made.
Features of a Fully Automatic Kurkure Factory
A fully automatic Kurkure factory is built around advanced technology and a streamlined production system that ensures maximum efficiency and quality. From ingredient preparation to packaging, every step is automated, delivering precision and scalability unmatched by manual operations.
Advanced Technology and Automation Systems
Modern Kurkure factories incorporate sophisticated automation technologies, including programmable logic controllers (PLCs), sensors, and monitoring systems. These components work together to maintain consistent production rates, control critical parameters such as temperature and pressure, and minimize waste. As food engineer Dr. Michael Grant states, "Automation in Kurkure manufacturing not only enhances production speed but also ensures the safety and reliability of the entire process."
Key Components of the Kurkure Factory
A Kurkure factory features several essential components, including:
Mixing units: Combine raw materials with precise formulations for consistency.
Extruders: Shape the Kurkure snacks while ensuring uniformity in size and texture.
Fryers or ovens: Cook the snacks to perfection, achieving the signature crunch.
Seasoning systems: Add flavors uniformly for a delightful taste experience.
Packaging units: Seal the products efficiently to maintain freshness and shelf life.
Each component is designed to integrate seamlessly into the production line, reducing downtime and enhancing overall throughput.
Energy-Efficient Machinery Design
Energy efficiency is a cornerstone of a fully automatic Kurkure factory. The machinery is engineered to reduce power consumption without compromising performance. Advanced thermal systems and optimized motor designs help minimize energy waste, making these factories both environmentally and economically sustainable. This aligns with the global push toward greener manufacturing practices, ensuring compliance with modern environmental standards.
Advantages of High-Efficiency Snack Production
A fully automatic Kurkure factory provides a host of advantages for manufacturers, making it an indispensable solution in modern snack production. These benefits span cost savings, quality improvements, and environmental sustainability, enabling manufacturers to meet growing consumer demands while remaining competitive.
Reduction in Production Costs and Time
One of the most significant advantages of a Kurkure factory is the dramatic reduction in operational costs and production time. Automated systems streamline the entire manufacturing process, minimizing the need for manual labor and significantly reducing human error. This efficiency translates into lower production costs and faster turnaround times, allowing manufacturers to meet high market demand without compromising on quality.
Enhanced Product Consistency and Quality
Consistency is key in the snack industry, and a fully automatic Kurkure factory ensures uniformity in every batch produced. The integration of precise control systems maintains consistent texture, flavor, and appearance across all products. According to industry expert Sarah Conner, "Automation in snack production guarantees that every piece meets the same high-quality standard, fostering consumer trust and brand loyalty."
Eco-Friendly and Energy-Saving Operations
Energy efficiency is another critical advantage of a Kurkure factory. By incorporating advanced energy-saving machinery, these factories significantly reduce their carbon footprint. Features like heat recovery systems, optimized power usage, and waste management solutions contribute to eco-friendly production practices. This not only reduces environmental impact but also aligns manufacturers with sustainability goals, a growing priority in the global food industry.
Applications of Kurkure Factory Technology
The versatility of a fully automatic Kurkure factory makes it a vital asset for snack manufacturers across various markets. Its adaptable technology supports the production of diverse snack varieties, scalable operations, and global industry demands.
Suitable for Diverse Snack Varieties
While primarily designed for Kurkure snacks, these factories can be customized to produce a wide range of similar extruded snacks. From spicy to cheesy flavors, the advanced seasoning systems ensure even distribution, catering to varied consumer preferences. This adaptability allows manufacturers to diversify their product lines without significant reconfiguration, making the Kurkure factory an efficient multi-purpose solution.
Scalability for Small, Medium, and Large-Scale Operations
A Kurkure factory can be scaled to meet the specific needs of different production volumes, from small-scale startups to large-scale snack manufacturers. Modular designs enable easy upgrades or adjustments as production demands grow. This flexibility ensures that businesses can expand without incurring excessive costs or delays, providing a clear path for long-term growth.
Meeting Global Snack Industry Demands
With the increasing popularity of Kurkure and similar snacks in international markets, fully automatic Kurkure factories are tailored to meet global demands. These factories adhere to stringent food safety and quality standards, making them suitable for export-oriented production. Additionally, their ability to maintain consistent quality and high production rates ensures manufacturers remain competitive in a rapidly evolving global snack industry.
Why Choose a Fully Automatic Kurkure Factory
Investing in a fully automatic Kurkure factory provides manufacturers with a competitive edge in the highly dynamic snack industry. From cost efficiency to sustainability, the advantages of these state-of-the-art systems align with the goals of modern food production.
Competitive Advantages for Manufacturers
In an industry where consistency and speed are paramount, a Kurkure factory ensures that every batch meets the highest standards. The automation reduces human intervention, decreasing the risk of contamination while maintaining product quality. By adopting fully automated systems, manufacturers can produce at a scale and efficiency that surpasses traditional methods, giving them a distinct advantage in the marketplace.
Long-Term Cost Savings and Higher ROI
Although the initial investment in a fully automatic Kurkure factory may seem significant, the long-term savings are substantial. Automation lowers operational costs by minimizing labor requirements and reducing waste during production. The energy-efficient designs further contribute to cost savings by cutting power consumption. These benefits lead to a faster return on investment (ROI), making it a financially sound decision for both small and large enterprises.
Alignment with Sustainable Production Trends
Sustainability has become a crucial factor in consumer and regulatory expectations. A Kurkure factory aligns perfectly with these trends by employing energy-saving technologies and waste reduction systems. Using eco-friendly materials and reducing carbon footprints not only benefits the environment but also enhances the brand's reputation in the eyes of environmentally conscious consumers.
Success Stories and Case Studies
The practical benefits of a fully automatic Kurkure factory can be best understood through real-world examples. These success stories demonstrate how advanced automation and high-efficiency systems have transformed snack production for manufacturers worldwide.
Real-World Examples of Fully Automatic Kurkure Factories
One leading snack manufacturer in India implemented a fully automatic Kurkure factory to scale production while reducing operational costs. By upgrading to automated extruders and energy-efficient fryers, the company increased its output by 40% while cutting energy consumption by 25%. These improvements allowed them to expand their product offerings and meet growing consumer demand across both domestic and international markets.
In another case, a mid-sized snack company in Southeast Asia used automation to enhance product consistency. The integration of PLC-controlled systems ensured that every Kurkure piece was identical in texture and flavor. This consistency won the brand significant recognition and loyalty among consumers, boosting their market share.
Efficiency Improvements and Energy Savings Achieved
Case studies consistently show that adopting a fully automatic Kurkure factory results in measurable efficiency gains. For example:
A North American snack producer reported a 30% reduction in production time after installing automated mixing and packaging units.
A European food company reduced production waste by 20%, thanks to precise extrusion and seasoning systems.
These examples highlight how automation technology not only improves profitability but also aligns with sustainability goals, creating a win-win situation for manufacturers and the environment.
Conclusion
In summary, a fully automatic Kurkure factory represents the future of high-efficiency snack production, offering numerous advantages that drive success in the competitive food manufacturing industry. From reducing costs and production time to enhancing product consistency and sustainability, these factories provide manufacturers with a significant edge.
The ability to scale production, adapt to diverse snack varieties, and meet global demands makes the Kurkure factory an indispensable asset. As automation continues to shape the snack industry, investing in such systems promises long-term profitability, energy savings, and a greener manufacturing process.
For manufacturers aiming to remain competitive in the evolving snack market, the time to embrace fully automatic Kurkure factory solutions is now—leading to smarter, more efficient production that meets the demands of today and the future.
Reference
The following are five authoritative foreign literature websites in the field of Industrial food machinery:
1. Food Engineering Magazine
Website: https://www.foodengineeringmag.com/
2.Food Processing Magazine
Website: https://www.foodprocessing.com/
3.Journal of Food Engineering
Website:https://www.journals.elsevier.com/journal-of-food-engineering
4. Food Manufacturing Magazine
Website:https://www.foodmanufacturing.com/
5. International Journal of Food Science & Technology
Website:https://onlinelibrary.wiley.com/