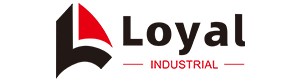
- Shandong Loyal Industrial Co.,Ltd.
- Macaroni Production Machine Instant Noodle Machine Biscuit Making Machine

Home> Processing> Fully Automatic Hard Biscuit Equipment for High-Efficiency Snack Production

Fully Automatic Hard Biscuit Equipment for High-Efficiency Snack Production
2025-04-30 10:57:37Introduction
The demand for high-efficiency snack production has seen a significant rise in recent years. As consumers seek convenient, tasty, and nutritious snacks, food manufacturers are compelled to adapt to evolving market needs. This surge in demand has led to innovations in food production technology, especially in automated systems designed to streamline production processes, reduce costs, and improve quality.
Among these innovations, hard biscuits have emerged as a popular snack worldwide, owing to their long shelf life, ease of production, and diverse flavors. Whether enjoyed as a quick breakfast, a midday snack, or an accompaniment to tea, hard biscuits hold an enduring place in the snack industry. Their appeal lies in their versatility, as they can be customized to cater to a wide range of dietary preferences and taste profiles.
The key to meeting the growing demand for hard biscuits lies in adopting fully automatic hard biscuit equipment. This cutting-edge technology has revolutionized the snack production process, making it more efficient, consistent, and scalable. Fully automatic hard biscuit production lines not only enhance the speed of manufacturing but also ensure consistent quality across large batches. With automation, the production of hard biscuits becomes more reliable, cost-effective, and faster—qualities that are indispensable in today’s fast-paced market.
What is Fully Automatic Hard Biscuit Equipment?
Definition and Explanation of Hard Biscuit Production Line
A hard biscuit production line refers to a fully integrated system designed to manufacture hard biscuits, a staple in the snack industry. This production line combines several key processes, including dough mixing, shaping, baking, and packaging, into one seamless system. Each component of the line works together to ensure the efficient creation of high-quality biscuits. The automation of this process reduces the need for manual intervention, making it faster, more consistent, and more cost-effective.
The hard biscuit production line is designed to handle large-scale production, making it ideal for snack manufacturers aiming to meet the increasing market demand. From start to finish, this system ensures precision, reducing the likelihood of human error while maximizing output.
Breakdown of Key Components in the Hard Biscuit Making Machine and Their Functions
A hard biscuit making machine is the heart of the production line, composed of several critical components that each perform specific functions to ensure optimal production efficiency. These components include:
Dough Mixer: The dough mixer is responsible for combining ingredients—flour, water, fats, and other flavorings—into a dough.
Shaping Machine: Once the dough is prepared, it is fed into the shaping machine, which cuts and forms the dough into the desired biscuit shape. This machine allows for high customization, adjusting mould shapes and sizes to meet market demands.
Baking Oven: The dough shapes are then baked in an automated baking oven, where heat is evenly distributed to produce uniformly crisp and golden biscuits. The oven’s precise temperature control ensures consistent results batch after batch.
Cooling Tunnel: After baking, the biscuits are cooled to room temperature in a cooling tunnel. This ensures that the biscuits retain their crisp texture and do not become too soft.
Packaging System: Finally, the biscuits are automatically packaged, sealing in freshness and extending shelf life. Packaging can be customized based on packaging type.
Description of the Hard Biscuit Equipment and How It Ensures Automation in Production
Hard biscuit equipment refers to the machinery used in the production line to carry out each of these tasks. The key advantage of fully automatic hard biscuit equipment is its ability to automate each step of the process, from dough mixing to packaging, without the need for manual labor.
Automation in these systems eliminates variability in production, which leads to improved consistency in the finished product. These machines are also designed for ease of operation, allowing manufacturers to manage production at a larger scale with minimal oversight. Hard biscuit equipment ensures that every biscuit produced meets strict quality standards, from texture and taste to size and appearance.
Furthermore, the integration of various steps into a single, cohesive system makes the production process more efficient. By automating each stage, the hard biscuit production line reduces the time spent on manual tasks, such as handling raw ingredients or packing finished products. This, in turn, accelerates production speeds, lowers labor costs, and minimizes human error—critical factors for manufacturers competing in a fast-moving market.
Hard biscuit production line flow chart
It is the same as mentioned in the previous article, except that its mold is a tough biscuit mold, which is rolled and formed.
Flour Mixing---Hard Biscuit Forming machine---Oven---Oil Spraying ---Cooling Conveyor---Biscuit Stacking ---Biscuit Packing
Regarding biscuit making machine, We have small and large biscuit machines for you to choose from.If you need a packaging machine, we also provide it.
The function of hard biscuit production line
- Mixer: Dough mixer is a machine that mixes flour with water or other ingredients into dough. It is widely used in making dough for various pastries, biscuits, bread, steamed buns, etc.
- Hard Biscuit Forming machine: Toughness molding: put the mixed dough into this machine, press the skin through three rollers, and then roll it into biscuit embryos through the roller cutting mold, and put it into the oven to bake medium and high-end tough biscuits.
- Oven: Suitable for baking all kinds of biscuits. Use electric heating, temperature zone control, temperature of each temperature zone can be set in advance, uniform temperature in the temperature zone, use high-quality insulation materials, good insulation performance, high thermal efficiency. Temperature control system, automatic temperature control and constant temperature, flexible operation, high safety performance.
- Oil Spraying: Spray oil on the surface of biscuits coming out of the baking oven to make the color, aroma and taste of the biscuits more distinctive and improve the grade of the biscuits.
- Cooling Conveyor: This equipment fully cools the biscuits before they are conveyed to the packaging machine to ensure the quality of the biscuits after packaging and extend the shelf life.
6.Biscuit Stacking: sort biscuits and pick out unqualified products.
Technical specifications of hard biscuit production line
Model |
Output |
LY-320 |
100-150kg/h |
LY-400 |
150-200kg/h |
LY-600 |
400-500kg/h |
LY-800 |
600-800kg/h |
LY-1000 |
1000kg/h |
LY-1200 |
2000kg/h |
Layout for the hard biscuit production line
Our machines can be flexibly arranged according to the size and dimensions of the factory. We can also customize the size of the machine according to the data you provide.
Sample of hard biscuit equipment
Benefits of Fully Automatic Hard Biscuit Production
Enhanced Production Speed and Scalability for Large Volumes
One of the key benefits of fully automatic hard biscuit production is its ability to scale production effectively and efficiently. Automated systems enable manufacturers to produce large volumes of biscuits with minimal human intervention, meeting the ever-growing demand for snacks in the global market. These production lines are designed to run continuously, allowing businesses to maintain high output levels while ensuring consistency across all batches.
The ability to scale production without sacrificing quality is crucial for businesses looking to expand their reach. Whether producing small batches for local markets or mass production for global distribution, the automated production line ensures that speed and efficiency remain at optimal levels throughout. This scalability makes the system ideal for businesses aiming to grow rapidly or respond to seasonal spikes in demand.
Improved Consistency and Product Quality, Reducing Defects
Consistency is one of the most critical factors in snack production. Consumers expect the same taste, texture, and appearance from every biscuit they purchase. With fully automatic hard biscuit equipment, the process is highly controlled, which leads to uniform results in every batch. From precise measurements of ingredients during dough preparation to constant temperature control in the baking process, automation ensures that every biscuit produced is consistent in quality.
This consistency significantly reduces the likelihood of defects such as overbaking, undercooking, or uneven texture. The control over each production step eliminates variables that could lead to subpar products. The outcome is a high-quality biscuit that meets both consumer expectations and industry standards, fostering brand loyalty and customer satisfaction.
Lower Operational Costs and Reduced Reliance on Manual Labor
In addition to increasing production efficiency, fully automatic hard biscuit production helps businesses reduce operational costs. The automation of production processes means that fewer staff members are needed to operate the machinery, monitor processes, or manage quality control. This leads to lower labor costs and allows companies to reallocate resources to other areas of their business, such as research and development, marketing, or customer service.
Moreover, automation minimizes human error, which can be costly in terms of wasted ingredients, production downtime, or product defects. With a more efficient production system, businesses can reduce waste, optimize their use of raw materials, and maintain tighter control over their overall production costs.
Reduced Downtime and Increased Reliability
Automated hard biscuit production lines are built to operate for extended periods with minimal downtime. Because the system is designed to handle large volumes of production continuously, there are fewer interruptions for repairs or maintenance compared to traditional, manual production processes. Routine maintenance and scheduled check-ups are easily managed, ensuring that the system remains in top working condition.
If you are interested, I will recommend a company to you, please continue reading.
Recommended Company
Shandong Loyal Industrial Co.,Ltd. Is a Manufacturer Of Snacks Extruder Machine , Industrial Microwave Oven , Corn Flakes Production Line , And a Standing Director Of China Food And Drying Equipment Industry Association.
The Self-developed Twin-screw Extruder And Single-screw Equipment of Shandong Loyal Machinery Have Been Used In Production: Puffed Snack Food, Breakfast Cereal Corn Flakes, Fried Pasta, Bread Crumbs, Fruit Chips, Baby Food, Textured Soy Protein (tsp) Food, Fish Feed And Pet Food. a Variety of Snack Production Line Supporting Products.at The Same Time, The Batching, Drying, Flaking, Baking, Frying And Spraying Equipment Matching The Twin-screw Extrusion System Have All Achieved Independent Design And Production.
Our Extrusion System Is Widely Used In: Puffed Snack Foods, Breakfast Cereals, Vegetable Protein Meat Products, Soy Based Nutrition Bars, Reconstituted Rice, Grain Nutrition Powder, Modified Starch, Starch-based Sticky Music Children's Educational Toys, Degradable Starch-based Packaging Filling Materials, Bread Crumbs And Other Food Additives, Pet Food, Aquatic Feed, Biology And Chemical Industries.
Customer-specific Food Processing Plant Project Solutions
As one of the leading manufacturers of food processing equipment, we are always searching for new solutions that benefit our snack food customers. Our experienced frying engineers always find the optimal solution for your industrial batch and continuous frying system line application. That's why we also develop, design and produce custom fried snack production line.
Close collaboration with our customer is important to us even in the early development phase. No matter what the special requirements of instant noodles production line, snack food extruder machine, pasta production line application, we can develop a custom made food processing equipment to match your needs.
Loyal have a unique and efficient industrial continuous frying equipment for snack food extruder machine that provides the right crunch and desired moisture level.
The Industrial Microwave Sterilization Defrosting Drying Machine can be designed as a dry powder dosing system and a wet slurry dosing system as required.
Some snacks can also be fried according to taste requirements, and we also provide Fried Snack Production Line for the processing and packaging of fried extruded snacks.
Loyal Food Production Line meet the needs of customers to obtain snack food that meet the needs.
In ovens or drying units, electric or gas can be used as heating sources.
Loyal have a unique and efficient industrial continuous frying equipment for snack food extruder machine that provides the right crunch and desired moisture level.
The Industrial Microwave Sterilization Defrosting Drying Machine can be designed as a dry powder dosing system and a wet slurry dosing system as required.
Some snacks can also be fried according to taste requirements, and we also provide Fried Snack Production Line for the processing and packaging of fried extruded snacks.
About packaging and after-sales service
Packing: Plastic Film Suitable For Ocean Carriage
Technical Support: The customer can inform machine related problems to us via telephone, email or fax. All information will be recorded and will be reported to the After-sale Service team. Meanwhile, the sales person will be tracking the case until problem solved.
Service Team:We have a professional After-sale Service team including10 professional engineers with at least 6 years working experience. They can handle technical consultation about manufacturing process, maintenance, fault diagnosis and troubleshooting, etc.
After-sale Service available :1.Check & test before delivery 2.Instruction for installation 3.On site commissioning 4.Repair & maintenance
After the receipt the advanced payment, we will provide allocation chart at the buyer’s request. When effect the shipment, we’ll provide operation manual, etc. in English.