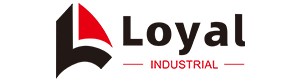
- Shandong Loyal Industrial Co.,Ltd.
- Macaroni Production Machine Instant Noodle Machine Biscuit Making Machine

Home> Company News> The Ultimate Guide To nutrition powder making machine Updated 2024

The Ultimate Guide To nutrition powder making machine Updated 2024
2024-07-24 10:53:02Importance of Automation in Food Processing Industries
Automation plays a crucial role in modern food processing industries, especially in the context of nutrition powder production. Nutrition powder making machines exemplify the integration of automation to achieve unprecedented levels of efficiency and energy savings.
These machines automate various stages of the production process, starting from ingredient mixing and blending to packaging and labeling. By eliminating manual interventions, they reduce the likelihood of human errors and ensure consistent product quality batch after batch. This reliability is paramount in industries where precision in ingredient ratios and processing times directly impacts product efficacy and consumer satisfaction.
Moreover, automation in nutrition powder making machines extends beyond mere operational efficiency. It encompasses predictive maintenance capabilities enabled by IoT (Internet of Things) technologies, which anticipate potential equipment failures before they occur. This proactive approach minimizes downtime and optimizes production schedules, thereby maximizing overall equipment effectiveness (OEE) and reducing operational costs.
From a sustainability standpoint, automated machines are designed to optimize energy usage. They incorporate energy-efficient components and processes, such as advanced heating and cooling systems that minimize energy wastage during production. This aligns with global efforts towards sustainable manufacturing practices and reduces the environmental footprint of food processing operations.
In conclusion, the adoption of fully automatic nutrition powder making machines underscores a paradigm shift towards smarter, more sustainable food manufacturing practices. By integrating automation, food processing industries not only enhance productivity and product quality but also contribute to environmental stewardship through reduced energy consumption and waste generation.
Focus on High Efficiency and Energy-Saving Benefits
Fully automatic nutrition powder making machines are engineered with a primary focus on maximizing efficiency and minimizing energy consumption throughout the production cycle. These machines leverage advanced technologies and innovative design features to achieve optimal performance and operational excellence.
One of the key benefits of automated systems is their ability to enhance production efficiency. By automating repetitive tasks such as ingredient weighing, mixing, and packaging, these machines significantly reduce production time while maintaining consistent product quality. This streamlined approach not only increases output but also improves overall productivity, allowing manufacturers to meet growing market demands effectively.
Moreover, automated nutrition powder making machines incorporate energy-saving mechanisms that contribute to sustainable manufacturing practices. These include efficient motor systems, automated shutdown protocols during idle periods, and intelligent energy management systems that optimize resource utilization without compromising production output.
Furthermore, the integration of IoT (Internet of Things) capabilities enables real-time monitoring and control of machine operations. Manufacturers can remotely access production data, monitor performance metrics, and make informed decisions to optimize efficiency further. This proactive approach not only minimizes downtime but also reduces operational costs associated with maintenance and energy consumption.
In essence, the high efficiency and energy-saving benefits of fully automatic nutrition powder making machines underscore their role as catalysts for innovation in the food processing industry. By embracing automation, manufacturers can achieve sustainable growth, enhance competitiveness, and deliver high-quality products that meet consumer expectations.
Understanding Fully Automatic Nutrition Powder Making Machines
In the realm of food machinery, the evolution towards automation has revolutionized processes, particularly in the production of nutrition powder. Fully automatic nutrition powder making machines represent a pinnacle of technological advancement in this sector. These machines are designed to streamline production processes, ensuring high efficiency and significant energy savings.
Introduction to Nutrition Powder Making Machines
Nutrition powder making machines are specialized equipment designed to efficiently blend, process, and package powdered nutritional products. These machines are equipped with advanced features such as automated mixing, precise ingredient dispensing, and integrated packaging systems. The automation eliminates manual errors and optimizes production throughput, making it an indispensable asset in large-scale food manufacturing facilities.
Key Features of Fully Automatic Machines
Fully automatic nutrition powder making machines boast several key features that set them apart from traditional equipment. These include:
Automated Process Control |
Integrated sensors and computerized control systems monitor and adjust production parameters in real-time, ensuring consistent product quality. |
High Efficiency |
By automating repetitive tasks like ingredient weighing, mixing, and packaging, these machines drastically reduce production time and labor costs. |
Energy Efficiency |
Modern designs incorporate energy-saving technologies such as efficient motors and optimized heat exchange systems, reducing overall energy consumption. |
Benefits of Automation in Nutrition Powder Production
The shift towards fully automatic machines offers numerous benefits to manufacturers:
Enhanced Productivity |
Automation increases production output while maintaining high standards of product quality and consistency. |
Cost Savings |
Reduced labor costs and energy efficiency contribute to lower operational expenses over time. |
Quality Assurance |
Automated processes minimize human error, ensuring precise formulation and packaging, which is crucial for meeting regulatory standards. |
Benefits of High Efficiency in Nutrition Powder Production
Efficiency is a cornerstone in the realm of nutrition powder production, especially with the integration of fully automatic machines. These advancements not only streamline operations but also offer substantial benefits across various aspects of manufacturing.
1. Increased Production Output
Fully automatic nutrition powder making machines significantly boost production output compared to traditional methods. By automating processes such as ingredient mixing, blending, and packaging, these machines ensure a consistent and higher volume of output in a shorter timeframe. This increased efficiency is crucial for meeting growing market demands without compromising on product quality.
2. Enhanced Resource Utilization
Efficient utilization of resources is another key advantage of fully automatic machines. These systems are designed to optimize raw material usage and minimize waste generation during the production process. Precise control over ingredient measurements and automated workflows reduce the margin of error, resulting in less material wastage and lower production costs over time.
3. Labor Cost Reduction
Automation reduces dependency on manual labor, thereby lowering labor costs associated with nutrition powder production. By automating repetitive tasks and integrating sophisticated control systems, manufacturers can allocate human resources to more skilled roles such as quality control and maintenance. This shift not only improves operational efficiency but also enhances overall workforce productivity.
4. Energy Savings and Sustainability
Modern fully automatic machines are engineered with energy-efficient technologies that contribute to sustainability efforts. These machines optimize energy consumption through features like programmable logic controllers (PLCs) and variable frequency drives (VFDs) that regulate motor speed and power usage based on real-time operational demands. As a result, manufacturers can reduce their carbon footprint while maintaining high production standards.
5. Consistent Product Quality
Consistency in product quality is paramount in nutrition powder manufacturing, where precise formulation and uniformity are critical. Fully automatic machines ensure consistent mixing ratios, ingredient dispersion, and packaging accuracy, minimizing variations in the final product. This reliability not only meets stringent regulatory requirements but also enhances consumer trust and brand reputation in the competitive marketplace.
6. Scalability and Flexibility
Scalability is a significant advantage of fully automatic nutrition powder making machines. These systems are designed to accommodate production scale-ups seamlessly, allowing manufacturers to respond swiftly to market demands or seasonal fluctuations. Automated processes also offer flexibility in adapting to diverse product formulations and packaging specifications, catering to evolving consumer preferences with minimal downtime.
Conclusion
The adoption of fully automatic nutrition powder making machines represents a transformative shift in the food machinery industry, offering substantial benefits in terms of efficiency, sustainability, and quality assurance. As technological advancements continue to drive innovation, these machines will play a pivotal role in shaping the future of nutrition powder production, meeting the dynamic needs of global markets effectively.
Energy Saving Techniques in Automated Production Processes
Efficiency in energy consumption is crucial for optimizing operations in automated nutrition powder production. Modern fully automatic machines integrate several advanced techniques to minimize energy usage while maintaining high productivity levels.
Advanced Heating and Cooling Systems |
Fully automatic nutrition powder making machines employ advanced heating and cooling systems designed for optimal energy efficiency. These systems utilize technologies such as heat exchangers and insulation materials to regulate temperatures precisely during different stages of production. By minimizing heat loss and optimizing thermal transfer, manufacturers can reduce overall energy consumption without compromising on processing quality. |
Variable Frequency Drives (VFDs) |
Variable Frequency Drives (VFDs) are integral components in automated machinery that control motor speed and power consumption based on real-time production demands. By adjusting motor speed to match specific operational requirements, VFDs optimize energy usage and reduce unnecessary power consumption during idle or low-demand periods. This adaptive control not only lowers electricity bills but also extends the lifespan of equipment components. |
Efficient LED Lighting |
Lighting plays a significant role in the operational environment of nutrition powder production facilities. Fully automatic machines are equipped with energy-efficient LED lighting systems that provide adequate illumination while consuming less power than traditional lighting options. LED lights generate minimal heat and have a longer operational lifespan, contributing to overall energy savings and maintenance cost reductions. |
Programmable Logic Controllers (PLCs) |
Programmable Logic Controllers (PLCs) serve as central control units in automated production systems, orchestrating sequences of operations with precision and efficiency. These controllers optimize energy consumption by monitoring and adjusting parameters such as equipment runtimes, process temperatures, and material flows in real time. By implementing energy-saving algorithms and predictive maintenance routines, PLCs enhance operational efficiency while minimizing energy waste. |
Regenerative Braking Systems |
Regenerative braking systems are innovative energy-saving technologies integrated into automated machinery. These systems recover and store kinetic energy generated during braking or deceleration phases of equipment operation. By converting this energy into usable electrical power or redistributing it within the production system, regenerative braking systems reduce reliance on external power sources and enhance overall energy efficiency. |
Energy Monitoring and Management |
Effective energy monitoring and management are essential for identifying and addressing potential inefficiencies in automated production processes. Manufacturers utilize advanced energy monitoring tools and software systems to track real-time energy consumption patterns, analyze data trends, and implement targeted strategies for energy optimization. Continuous monitoring allows for proactive maintenance interventions and adjustments to operational parameters, ensuring sustained energy savings and operational reliability. |
Conclusion
Energy-saving techniques in fully automatic nutrition powder making machines represent a critical aspect of sustainable manufacturing practices. By integrating advanced technologies and adopting proactive energy management strategies, manufacturers can achieve significant reductions in energy consumption, lower production costs, and enhance overall operational efficiency. As the industry continues to innovate, these techniques will play a pivotal role in shaping the future of automated food machinery, meeting both economic and environmental goals effectively.
Emerging Technologies and Their Potential Impact
The landscape of food machinery, especially in nutrition powder production, is continually evolving with the integration of emerging technologies. These advancements not only enhance operational efficiency but also pave the way for new possibilities in manufacturing capabilities.
1. Internet of Things (IoT) Integration
IoT integration is revolutionizing the automation of nutrition powder making machines by enabling real-time data monitoring and predictive maintenance. Sensors embedded within equipment collect operational metrics such as temperature, humidity, and energy consumption. This data is then analyzed to optimize production processes, detect anomalies, and preemptively address potential equipment failures. IoT-enabled machines facilitate proactive decision-making, ensuring consistent product quality and minimizing downtime.
2. Artificial Intelligence (AI) and Machine Learning
AI and machine learning algorithms are increasingly being applied to enhance the performance of fully automatic nutrition powder making machines. These technologies analyze vast datasets to optimize production parameters, predict ingredient blending ratios, and improve packaging efficiency. AI-driven systems can adapt to variable production conditions, continuously refining operational strategies to maximize throughput and minimize waste. By leveraging AI, manufacturers can achieve unprecedented levels of precision, quality control, and operational flexibility in nutrition powder manufacturing.
3. Robotics and Automation
The integration of robotics in food machinery is transforming manufacturing workflows, particularly in handling and packaging processes. Robotics systems equipped with advanced grippers and vision sensors automate intricate tasks such as product sorting, palletizing, and quality inspection. In nutrition powder production, robotic arms ensure precise filling and sealing of packaging containers, significantly reducing human error and enhancing production line efficiency. The synergy between robotics and automation technologies streamlines operations, accelerates throughput, and optimizes resource utilization in food manufacturing facilities.
4. 3D Printing in Equipment Manufacturing
3D printing, also known as additive manufacturing, is revolutionizing the design and production of components for nutrition powder making machines. This technology enables manufacturers to create complex geometries and customized parts with enhanced durability and performance. In equipment manufacturing, 3D printing reduces lead times, lowers production costs, and facilitates rapid prototyping of innovative machine designs. By leveraging 3D printing, manufacturers can customize equipment to meet specific production requirements, integrate advanced features, and enhance overall system reliability in nutrition powder production.
5. Sustainable Innovations
Sustainable innovations are driving the development of eco-friendly solutions in nutrition powder making machines. Manufacturers are incorporating renewable energy sources such as solar panels and wind turbines to power automated production processes, reducing dependency on fossil fuels and minimizing carbon emissions. Additionally, bio-based materials and recyclable packaging solutions are being adopted to enhance environmental sustainability throughout the product lifecycle. By embracing sustainable practices, food machinery manufacturers contribute to global efforts towards resource conservation, environmental stewardship, and circular economy principles.
Reference
The following are five authoritative foreign literature websites in the field of Industrial food machinery:
1. Food Engineering Magazine
Website: https://www.foodengineeringmag.com/
2.Food Processing Magazine
Website: https://www.foodprocessing.com/
3.Journal of Food Engineering
Website:https://www.journals.elsevier.com/journal-of-food-engineering
4. Food Manufacturing Magazine
Website:https://www.foodmanufacturing.com/
5. International Journal of Food Science & Technology
Website:https://onlinelibrary.wiley.com