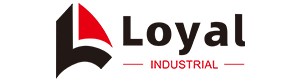
- Shandong Loyal Industrial Co.,Ltd.
- Macaroni Production Machine Instant Noodle Machine Biscuit Making Machine

Home> Company News> The Ultimate Guide To nutritional powder baby food processing line Updated 2024

The Ultimate Guide To nutritional powder baby food processing line Updated 2024
2024-08-05 10:53:13Necessity for Efficient and Energy-Saving Processing Lines in Nutritional Powder Baby Food Production
In the realm of baby food manufacturing, the pursuit of efficiency and energy savings has become paramount. As parents and caregivers continue to prioritize the health and wellbeing of infants, the demand for high-quality, nutrient-dense baby food has soared. Nutritional powder baby food, in particular, has gained immense popularity due to its convenience, versatility, and ability to provide a balanced blend of essential nutrients. However, to meet this growing demand sustainably, the industry must embrace efficient and energy-saving processing lines.
Firstly, let's delve into the necessity for efficiency in baby food processing. With the proliferation of baby food brands and the increasing competition in the market, manufacturers are under immense pressure to produce large quantities of product while maintaining stringent quality standards. A fully automated nutritional powder baby food processing line offers a solution by streamlining production processes, reducing manual intervention, and enhancing overall productivity. This not only helps manufacturers keep up with demand but also ensures consistency in product quality and safety.
Moreover, the energy consumption associated with traditional baby food processing methods can be substantial. From raw material preparation to final packaging, each step requires energy, often leading to high operational costs and a significant carbon footprint. In today's eco-conscious world, it's imperative for businesses to adopt sustainable practices that minimize their environmental impact. An energy-saving nutritional powder baby food processing line, equipped with state-of-the-art technologies, can significantly reduce energy consumption throughout the production cycle.
One of the key advantages of such a processing line is its ability to optimize resource utilization. By precisely controlling temperature, mixing conditions, and other critical parameters, it minimizes waste and over-processing, ensuring that every ounce of energy is used efficiently. Additionally, the integration of renewable energy sources, such as solar or wind power, where feasible, can further reduce the carbon footprint of the production process.
From an economic perspective, efficient and energy-saving processing lines offer a compelling business case. By reducing energy consumption and waste, manufacturers can achieve cost savings that can be reinvested in product innovation, quality improvement, or price reductions, ultimately benefiting both consumers and the environment.
Definition and key components of a fully automated line
In the realm of modern food processing, the fully automated nutritional powder baby food processing line represents a pinnacle of technological advancement. This sophisticated system integrates a myriad of cutting-edge machines and technologies to streamline the production of high-quality, nutrient-dense baby food powders. Understanding the definition and key components of such a line is crucial for manufacturers seeking to enhance their production capabilities and remain competitive in the market.
Definition:
A fully automated nutritional powder baby food processing line is a comprehensive assembly of interconnected equipment designed to convert raw ingredients into finished baby food powders with minimal human intervention. This system encapsulates every stage of the production process, from ingredient preparation and mixing to drying, milling, blending, and final packaging, all under strict quality control measures.
Key Components:
Ingredient Handling and Preparation |
The line begins with the handling and preparation of raw ingredients. This stage involves the accurate measurement and blending of various nutrients, vitamins, minerals, and other additives to create a balanced formula. Automated feeders and mixers ensure precise ingredient ratios and homogeneity, reducing the risk of contamination and ensuring product consistency. |
Wet Mixing and Cooking |
Following ingredient preparation, the mixture is subjected to wet mixing and cooking. High-shear mixers and steam-jacketed kettles are commonly used to ensure thorough blending and sterilization of the mixture, killing harmful bacteria and enhancing the digestibility of nutrients. |
Drying and Milling |
Once cooked, the mixture is dried to remove excess moisture and convert it into a powder form. Spray dryers are the most prevalent technology for this purpose, as they offer fast and efficient drying while preserving the nutritional integrity of the product. Following drying, the resulting agglomerates are milled into a fine, uniform powder using specialized milling equipment. |
Blending and Conditioning |
The powdered ingredients may undergo further blending and conditioning to ensure consistent quality and flowability. This step is crucial for ensuring that the final product meets strict quality standards and is easy to handle and package. |
Packaging and Distribution |
The final stage of the processing line involves packaging the nutritional powder baby food into convenient containers, such as pouches, jars, or cans. Automated packaging machines, including filling, sealing, and labeling equipment, ensure rapid and hygienic packaging, minimizing human error and contamination risks. The packaged products are then inspected, labeled, and distributed to retailers and consumers. |
Automation and Control Systems |
Throughout the entire processing line, automation and control systems play a pivotal role. These systems monitor and regulate critical process parameters, such as temperature, humidity, and mixing speeds, ensuring optimal conditions for each stage of production. Additionally, they facilitate data collection and analysis, enabling manufacturers to continuously improve their processes and maintain the highest standards of quality and safety. |
Advantages of automation in baby food processing
In the realm of baby food production, automation has emerged as a game-changer, particularly in the realm of nutritional powder baby food processing lines. By incorporating advanced automation technologies, manufacturers can achieve significant benefits that not only enhance production efficiency but also ensure the highest standards of safety and quality. As an industrial food machinery expert, I will delve into the advantages of automation in baby food processing, with a specific focus on nutritional powder lines.
1. Improved Efficiency and Productivity:
Automation eliminates the need for manual labor in many time-consuming and repetitive tasks. In a fully automated nutritional powder baby food processing line, machines handle ingredient handling, mixing, drying, milling, blending, packaging, and other critical steps with precision and speed. This significantly increases production capacity, allowing manufacturers to produce larger quantities of baby food powders in a shorter time frame.
2. Enhanced Product Consistency and Quality:
Automation ensures that every step of the production process is carried out with the utmost precision and consistency. Automated control systems monitor and regulate critical process parameters, such as temperature, humidity, and mixing speeds, ensuring that the final product meets strict quality standards. This consistency in production leads to a more uniform and reliable product, giving parents peace of mind that their baby is receiving the best possible nutrition.
3. Reduced Risk of Contamination:
Manual handling of ingredients and products increases the risk of contamination from dirt, bacteria, or other contaminants. Automation minimizes human intervention, thereby reducing the chances of contamination. Automated packaging systems, for instance, can seal products immediately after filling, preventing exposure to the environment and maintaining the product's purity.
4. Enhanced Energy Efficiency:
Efficient energy-saving nutritional powder baby food processing lines are designed to minimize energy consumption throughout the production process. Advanced automation technologies, such as energy-efficient motors and optimized drying processes, help reduce energy waste and lower operating costs. This not only benefits the manufacturer's bottom line but also aligns with the growing demand for sustainable and environmentally friendly production practices.
5. Real-time Monitoring and Data Analytics:
Automated systems collect vast amounts of data throughout the production process, providing manufacturers with real-time insights into their operations. This data can be analyzed to identify inefficiencies, predict maintenance needs, and optimize production schedules. Additionally, data analytics can help manufacturers develop new products and improve existing ones based on consumer preferences and market trends.
6. Scalability and Flexibility:
Automated processing lines are highly scalable, allowing manufacturers to adjust their production capacity based on market demand. As baby food consumption patterns change, automated systems can be easily modified or expanded to accommodate new product formulations or production volumes. This flexibility ensures that manufacturers remain competitive in a rapidly evolving market.
Energy-Saving Features of the Processing Line
In the modern era of food processing, energy efficiency is a paramount concern for manufacturers, especially in the context of nutritional powder baby food production. An efficient energy-saving nutritional powder baby food processing line with full automation is designed to minimize energy consumption while maximizing production output. As an industrial food machinery expert, I will elaborate on the key energy-saving features that characterize such a processing line.
Energy-Efficient Motors and Drives |
At the heart of any energy-saving processing line are energy-efficient motors and drives. These advanced components are designed to consume less electricity while delivering the same or higher levels of power and torque. By incorporating variable frequency drives (VFDs) and permanent magnet motors, manufacturers can significantly reduce energy consumption during mixing, drying, and other power-intensive processes. |
Optimized Drying Processes |
Drying is a crucial step in the production of nutritional powder baby food, and it can also be a significant energy consumer. Energy-saving processing lines employ optimized drying technologies, such as convective drying, spray drying, or freeze-drying, depending on the specific product requirements. These methods are carefully calibrated to minimize energy usage while ensuring thorough and efficient drying of the product. |
Heat Recovery Systems |
Heat recovery systems are a vital component of energy-saving processing lines. By capturing and reusing waste heat generated during the production process, these systems significantly reduce the need for additional energy input. For instance, heat generated during drying can be harnessed to preheat incoming air or water, thereby reducing the overall energy consumption of the system. |
Intelligent Control Systems |
Advanced control systems play a pivotal role in optimizing energy usage. These systems monitor and regulate various process parameters in real-time, adjusting motor speeds, temperatures, and other settings to minimize energy waste. By using predictive analytics and machine learning algorithms, control systems can anticipate energy demands and adjust operations accordingly, ensuring that energy is used only when necessary. |
Energy-Efficient Packaging Solutions |
Energy-saving does not end with the production process; it extends to packaging as well. Modern processing lines often incorporate energy-efficient packaging machines that use less electricity and minimize material waste. Additionally, vacuum packaging and modified atmosphere packaging (MAP) techniques can help extend product shelf life, reducing the need for refrigeration or other energy-intensive storage methods. |
Sustainable Design and Materials |
The overall design and materials used in the processing line also contribute to energy savings. Using lightweight, durable materials for equipment and structures can reduce the energy required for transportation and installation. Furthermore, incorporating sustainable design principles, such as natural ventilation and daylighting, can further minimize energy consumption in the production facility. |
Ensuring Nutritional Integrity
1. Precision Ingredient Handling
The first step towards ensuring nutritional integrity begins with precise ingredient handling. The processing line must be equipped with accurate weighing and metering systems that ensure that each ingredient is added in the correct proportions. This precision is crucial, as even small deviations in ingredient ratios can significantly impact the nutritional content of the final product.
2. Gentle Processing Techniques
To preserve the delicate nutrients present in baby food ingredients, the processing line employs gentle processing techniques. This includes minimizing heat exposure, avoiding excessive shearing or agitation, and using low-pressure drying methods. By adopting these gentle approaches, the processing line ensures that vital nutrients such as vitamins, minerals, and essential fatty acids are retained in their bioavailable forms.
3. Advanced Mixing and Blending
Efficient mixing and blending are essential for achieving a uniform and nutritionally balanced final product. The processing line incorporates advanced mixing and blending technologies that ensure thorough and homogeneous blending of ingredients. This not only ensures that each serving of baby food contains the same nutritional profile but also prevents the formation of nutrient-poor or nutrient-dense pockets within the product.
4. Controlled Drying Conditions
Drying is a critical step in the production of nutritional powder baby food, and it must be carried out under carefully controlled conditions to preserve nutritional integrity. The processing line employs optimized drying technologies that minimize heat exposure and prevent nutrient degradation. By precisely controlling the temperature, humidity, and airflow during the drying process, manufacturers can ensure that the final product retains its full nutritional value.
5. Sanitary Design and Hygiene
Sanitary design and rigorous hygiene practices are vital in maintaining nutritional integrity throughout the processing line. The equipment is designed to be easy to clean and sanitize, minimizing the risk of contamination and nutrient loss. Additionally, regular maintenance and inspections ensure that the processing line remains in optimal condition, contributing to the overall quality and nutritional value of the final product.
6. Traceability and Quality Control
To ensure nutritional integrity, the processing line must be equipped with robust traceability and quality control systems. These systems allow manufacturers to track each ingredient from its source to the final product, ensuring that only the highest quality ingredients are used. Additionally, regular testing and analysis of the final product ensure that it meets all relevant nutritional standards and regulations.
Reference
The following are five authoritative foreign literature websites in the field of Industrial food machinery:
1. Food Engineering Magazine
Website: https://www.foodengineeringmag.com/
2.Food Processing Magazine
Website: https://www.foodprocessing.com/
3.Journal of Food Engineering
Website:https://www.journals.elsevier.com/journal-of-food-engineering
4. Food Manufacturing Magazine
Website:https://www.foodmanufacturing.com/
5. International Journal of Food Science & Technology
Website:https://onlinelibrary.wiley.com