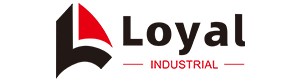
- Shandong Loyal Industrial Co.,Ltd.
- Macaroni Production Machine Instant Noodle Machine Biscuit Making Machine

Home> Company News> Unlock The Secrets Of Efficient nutritional powder food processing line Manufacturing

Unlock The Secrets Of Efficient nutritional powder food processing line Manufacturing
2024-08-06 09:55:45Challenges faced in traditional powder food processing
In the realm of food manufacturing, nutritional powder food processing has traditionally been a labor-intensive and resource-draining endeavor. Traditional powder food processing lines often struggle with a myriad of challenges that not only hinder production efficiency but also drive up costs significantly. These challenges underscore the urgent need for innovation and modernization in the industry, particularly the adoption of fully automated, high-efficiency, and energy-saving systems.
One of the primary challenges in traditional powder food processing lies in the inconsistency of output quality. Manual operations and reliance on human intervention introduce a high degree of variability, making it difficult to maintain consistent product quality across batches. This inconsistency can lead to customer dissatisfaction, product recalls, and ultimately, damage to brand reputation.
Furthermore, traditional powder food processing lines are often plagued by inefficiencies in production processes. From raw material handling and pre-treatment to drying, milling, mixing, and packaging, each step is prone to bottlenecks and delays that can significantly slow down production speed. These inefficiencies not only increase labor costs but also lead to higher energy consumption and waste generation, further escalating production expenses.
Another significant challenge is the difficulty in scaling up production to meet growing market demands. Traditional processing lines are often limited by their capacity and flexibility, making it challenging to quickly adjust production volumes in response to changing market conditions. This lack of scalability can result in missed opportunities and lost revenue for food manufacturers.
Moreover, traditional powder food processing methods often pose significant health and safety risks to workers. Exposure to dust, allergens, and other hazards can lead to respiratory problems, skin irritation, and other occupational health issues. These risks not only impact the well-being of workers but also expose food manufacturers to potential legal liabilities and increased insurance costs.
Finally, the environmental impact of traditional powder food processing cannot be overlooked. High energy consumption, waste generation, and emissions from production processes contribute to the overall carbon footprint of the industry. As consumer awareness of sustainability and environmental responsibility grows, food manufacturers are under increasing pressure to adopt more eco-friendly production methods.
In conclusion, traditional powder food processing faces numerous challenges that hinder production efficiency, drive up costs, and pose risks to both workers and the environment. To overcome these challenges and remain competitive in the market, food manufacturers must embrace innovation and modernization by adopting fully automated, high-efficiency, and energy-saving nutritional powder food processing systems.
Need for Optimization and Innovation in Production Costs
In the highly competitive landscape of the food industry, manufacturers of nutritional powder products are constantly seeking ways to optimize production costs while maintaining or enhancing product quality. The relentless pursuit of cost efficiency has become paramount, driven by the need to stay afloat amidst rising raw material costs, labor shortages, and increasing consumer demands. This pressing need underscores the critical importance of optimization and innovation in the nutritional powder food processing line.
The Challenge of Rising Costs |
In recent years, the food industry has been faced with a myriad of challenges that have significantly impacted production costs. Rising raw material prices, coupled with fluctuations in the global supply chain, have made it increasingly difficult for manufacturers to maintain profitability. Moreover, labor shortages and increasing labor costs have added further pressure on production budgets, necessitating a shift towards automation and other cost-saving measures. |
The Imperative for Optimization |
Given these challenges, the need for optimization in the nutritional powder food processing line has become more urgent than ever. By optimizing production processes, manufacturers can significantly reduce waste, minimize downtime, and improve overall operational efficiency. This, in turn, leads to lower production costs and enhanced profitability. |
Innovation as a Driving Force |
Innovation plays a pivotal role in driving optimization efforts in the nutritional powder food processing line. Advancements in technology, such as automation, artificial intelligence, and predictive maintenance, offer manufacturers new tools to streamline production processes and achieve unprecedented levels of efficiency. By embracing these innovations, manufacturers can stay ahead of the curve, reducing costs, and improving product quality. |
Fully Automated, High-Efficiency Systems |
One of the most significant innovations in the nutritional powder food processing line is the development of fully automated, high-efficiency systems. These systems integrate advanced robotics, sensors, and control systems to automate every step of the production process, from raw material handling to final packaging. By eliminating manual intervention, these systems significantly reduce labor costs and enhance operational efficiency. Furthermore, their precision control over process parameters ensures consistent product quality, minimizing waste and maximizing yield. |
Energy-Saving Technologies |
Another critical aspect of optimization and innovation in the nutritional powder food processing line is the adoption of energy-saving technologies. By incorporating energy-efficient motors, drives, and insulation systems, manufacturers can significantly reduce energy consumption and lower operating costs. Additionally, the use of heat recovery systems and other energy-saving measures further enhances the overall efficiency of the processing line. |
Understanding the Fully Automated Nutritional Powder Food Processing Line
The fully automated nutritional powder food processing line represents a significant advancement in the food industry, revolutionizing the way nutritional powders are produced. This advanced system integrates cutting-edge technologies and automation techniques to streamline production processes, enhance efficiency, and reduce costs. As an industrial food machinery expert, let's delve deeper into the intricacies of this innovative system.
1.The Core Components
At the heart of a fully automated nutritional powder food processing line are a series of interconnected machines and equipment designed to perform specific tasks seamlessly. These components range from raw material handling and preparation, through to mixing, drying, milling, and finally, packaging. Each stage is carefully optimized to ensure maximum efficiency and minimal waste.
2.Raw Material Handling and Preparation
The process begins with the handling and preparation of raw materials. Automated feeders and conveyors transport raw ingredients such as vitamins, minerals, and other nutritional additives into the mixing stage. Precision scales and metering devices ensure accurate dosing, minimizing errors and ensuring consistent product quality.
3.Mixing and Blending
The mixing and blending stage is critical to achieving a uniform, homogeneous product. Fully automated mixing systems utilize high-shear mixers or planetary mixers, equipped with advanced control systems to maintain precise mixing parameters. These systems ensure that all ingredients are thoroughly blended, creating a consistent, high-quality nutritional powder.
4.Drying and Milling
After mixing, the product is often subjected to drying and milling processes. Automated drying systems, such as spray dryers or fluidized bed dryers, remove moisture efficiently, preventing product degradation and extending shelf life. Subsequently, milling equipment breaks down the dried product into the desired particle size, ensuring uniform distribution and improved solubility.
5.Automated Packaging
The final stage of the process involves automated packaging. High-speed packaging machines, equipped with filling, sealing, and labeling capabilities, ensure that products are packaged quickly, accurately, and consistently. Automated quality control systems inspect each package for defects, ensuring that only the highest quality products reach consumers.
6.Integration and Automation
The key to the success of a fully automated nutritional powder food processing line lies in its seamless integration and automation. Advanced control systems, powered by PLCs (Programmable Logic Controllers) and SCADA (Supervisory Control and Data Acquisition) systems, oversee the entire process, ensuring that all machines and equipment work in harmony. Real-time monitoring and data analytics enable operators to make informed decisions, optimize production parameters, and minimize downtime.
7.Benefits of Automation
The adoption of a fully automated nutritional powder food processing line offers numerous benefits. Firstly, automation significantly reduces labor costs, as fewer workers are required to operate the system. Additionally, automation eliminates human error, improving product quality and consistency. Furthermore, the precision control over process parameters ensures optimal resource utilization, reducing waste and maximizing yield. Finally, automation enhances production flexibility, enabling manufacturers to quickly adapt to changing market demands and product formulations.
Energy-Saving Measures Incorporated in the System
In the pursuit of optimizing production costs, a fully automated, high-efficiency nutritional powder food processing system incorporates various energy-saving measures that not only reduce operational expenses but also contribute to a greener, more sustainable production process. As an industrial food machinery expert, I will delve into these energy-saving strategies, highlighting their importance and the tangible benefits they bring to manufacturers.
1.Efficient Heating and Cooling Systems
One of the primary energy-consuming processes in nutritional powder production is heating and cooling. To minimize energy usage, advanced heating and cooling systems are integrated into the processing line. These systems employ high-efficiency heat exchangers and insulation materials, reducing heat loss and maximizing thermal efficiency. Additionally, they utilize intelligent control algorithms that adjust heating and cooling rates based on real-time process parameters, eliminating over-heating or over-cooling, thereby conserving energy.
2.Energy-Efficient Motors and Drives
Motors and drives are critical components in any automated processing system, and their efficiency can significantly impact overall energy consumption. In a fully automated nutritional powder food processing line, energy-efficient motors and drives are utilized throughout the system. These motors are designed to operate at peak efficiency across a wide range of loads, reducing energy waste during periods of partial or light loads. Furthermore, advanced drive systems, such as variable frequency drives (VFDs), allow for precise control of motor speed, further optimizing energy usage.
3.Optimized Process Parameters
The optimization of process parameters plays a vital role in energy saving. By carefully controlling factors such as mixing speed, drying temperature, and milling duration, manufacturers can minimize unnecessary energy consumption while ensuring product quality. Advanced control systems, integrated into the processing line, continuously monitor and adjust these parameters based on real-time data, achieving optimal performance with minimal energy input.
4.Recycling and Recovery Systems
Energy-saving measures also extend to the recovery and recycling of process by-products and waste heat. For instance, exhaust gases from drying processes often contain significant amounts of recoverable heat. By integrating heat recovery systems, this waste heat can be captured and reused, reducing the need for additional heating sources. Similarly, process by-products, such as dust and fines, can be recycled back into the process or repurposed for other applications, minimizing waste and conserving resources.
5.Lighting and HVAC Systems
Finally, the facility's lighting and HVAC (Heating, Ventilation, and Air Conditioning) systems also play a role in energy savings. Energy-efficient lighting fixtures, such as LED lights, are used throughout the processing line, significantly reducing electricity consumption compared to traditional lighting systems. Additionally, intelligent HVAC systems, equipped with occupancy sensors and automated temperature controls, ensure that only the necessary amount of heating or cooling is provided, minimizing energy waste.
Impact on Production Costs
In the competitive landscape of the food industry, optimizing production costs is a paramount concern for manufacturers, particularly in the realm of nutritional powder production. A fully automated, high-efficiency, energy-saving nutritional powder food processing system represents a game-changer, offering significant cost savings across various aspects of the production process. As an industrial food machinery expert, I will delve into the impact this advanced system has on production costs.
Reduced Labor Costs |
One of the most immediate cost savings realized with a fully automated system is the reduction in labor costs. Automated processing lines eliminate the need for manual labor in tasks such as mixing, drying, milling, and packaging, significantly reducing the workforce requirements. This not only saves on wages but also eliminates the need for training, supervision, and the potential for human error, further contributing to cost savings. |
Improved Efficiency and Throughput |
Efficiency and throughput are crucial factors in determining production costs. A high-efficiency processing system ensures that raw materials are processed quickly and efficiently, maximizing output while minimizing waste. With precise control over process parameters and continuous monitoring capabilities, manufacturers can achieve optimal performance levels, resulting in higher yields and lower production costs per unit. |
Reduced Energy Consumption |
Energy is a significant expense in any manufacturing process, and the incorporation of energy-saving measures in a nutritional powder food processing system can lead to substantial cost savings. As discussed earlier, efficient heating and cooling systems, energy-efficient motors and drives, and recycling and recovery systems all contribute to reduced energy consumption. Over time, these savings can translate into significant cost reductions, improving the overall profitability of the production process. |
Minimized Downtime and Maintenance Costs |
Downtime can be a costly issue in any production environment, and a fully automated, high-efficiency processing system is designed to minimize downtime. Regular maintenance and predictive maintenance programs, facilitated by advanced monitoring and diagnostic tools, help identify potential issues before they become major problems, reducing unplanned downtime. Additionally, the use of high-quality components and materials in the construction of the system ensures long-term reliability and reduced maintenance costs. |
Increased Product Quality and Consistency |
Another significant impact on production costs is the improvement in product quality and consistency. With precise control over process parameters and automated quality control checks, manufacturers can ensure that every batch of nutritional powder meets the highest standards. This consistency in product quality leads to fewer rejects, reducing waste and improving customer satisfaction, both of which contribute to lower production costs. |
Reference
The following are five authoritative foreign literature websites in the field of Industrial food machinery:
1. Food Engineering Magazine
Website: https://www.foodengineeringmag.com/
2.Food Processing Magazine
Website: https://www.foodprocessing.com/
3.Journal of Food Engineering
Website:https://www.journals.elsevier.com/journal-of-food-engineering
4. Food Manufacturing Magazine
Website:https://www.foodmanufacturing.com/
5. International Journal of Food Science & Technology
Website:https://onlinelibrary.wiley.com