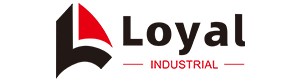
- Shandong Loyal Industrial Co.,Ltd.
- Macaroni Production Machine Instant Noodle Machine Biscuit Making Machine

Home> Company News> The Ultimate Guide to Breakfast Cereal Corn Flakes Extruder Production Line in 2024

The Ultimate Guide to Breakfast Cereal Corn Flakes Extruder Production Line in 2024
2024-07-01 11:19:17Introduction
In 2024, the breakfast cereal industry continues to thrive, with corn flakes maintaining their status as a staple in households worldwide. As consumers increasingly seek convenient and nutritious options, the demand for high-quality cereals has surged. This has driven significant advancements in production line technologies, particularly in the use of extruders for manufacturing corn flakes.
Importance of Corn Flakes in the Breakfast Cereal Market
Corn flakes are a cornerstone of the breakfast cereal market due to their wide appeal, nutritional benefits, and versatility. They are enjoyed by people of all ages and are often fortified with essential vitamins and minerals. The consistent demand for corn flakes has necessitated efficient and innovative production methods, highlighting the critical role of the Breakfast Cereal Corn Flakes Extruder Production Line.
Purpose of the Guide: Navigating the Extruder Production Line
This guide aims to provide an in-depth understanding of the Breakfast Cereal Corn Flakes Extruder Production Line. Whether you are a food industry professional looking to enhance your production capabilities or an entrepreneur considering entering the cereal market, this guide will equip you with the knowledge needed to navigate the complexities of corn flakes production using modern extruder technology.
Types of Extruders Used in Corn Flakes Production
In the production of corn flakes, the choice of extruder is critical to ensuring product quality, consistency, and efficiency. There are several types of extruders used in the Breakfast Cereal Corn Flakes Extruder Production Line, each with distinct advantages depending on the production requirements.
Single-Screw Extruders
Single-screw extruders are one of the most common types used in corn flakes production. These extruders are known for their simplicity, ease of operation, and cost-effectiveness. They consist of a single screw housed within a cylindrical barrel. The screw rotates to mix, knead, and push the raw materials through a die, forming the desired shape and texture of the corn flakes. Single-screw extruders are suitable for producing large quantities of corn flakes and are particularly effective in handling materials with lower moisture content.
Twin-Screw Extruders
Twin-screw extruders are highly versatile and offer greater control over the extrusion process compared to single-screw extruders. They feature two intermeshing screws that rotate simultaneously, providing enhanced mixing, shearing, and conveying capabilities. This type of extruder is ideal for producing corn flakes with complex formulations, including those with added ingredients such as vitamins, minerals, and flavorings. Twin-screw extruders are also more efficient in processing high-moisture materials, making them a preferred choice for many modern Breakfast Cereal Corn Flakes Extruder Production Lines.
Co-Rotating Twin-Screw Extruders
A subset of twin-screw extruders, co-rotating twin-screw extruders, have screws that rotate in the same direction. This configuration ensures thorough mixing and homogenization of the ingredients, resulting in a uniform product. Co-rotating twin-screw extruders are particularly effective in producing high-quality corn flakes with consistent texture and taste. They are also known for their flexibility in adjusting to different product specifications and processing conditions.
Counter-Rotating Twin-Screw Extruders
In contrast, counter-rotating twin-screw extruders have screws that rotate in opposite directions. This setup provides superior compression and shearing forces, which are beneficial for certain formulations that require intense mixing and breaking down of ingredients. Although less common in the corn flakes production sector, counter-rotating twin-screw extruders can be advantageous for specific niche products or unique processing requirements.
Advanced Extruder Technologies
Recent advancements in extruder technology have led to the development of hybrid extruders and specialized extruder systems designed to enhance production efficiency and product quality. These innovations include improved temperature control systems, advanced screw designs, and automated monitoring and control features. Integrating these advanced technologies into the Breakfast Cereal Corn Flakes Extruder Production Line allows manufacturers to optimize their processes, reduce waste, and produce corn flakes that meet the highest standards of quality and safety.
Key Components of a Corn Flakes Extruder
In the Breakfast Cereal Corn Flakes Extruder Production Line, understanding the key components of the extruder is essential for ensuring efficient and high-quality production. Below is a detailed table outlining the primary components of a corn flakes extruder:
Component |
Description |
Function |
Feeding System |
Includes hoppers and feeders that introduce raw materials into the extruder. |
Ensures consistent and controlled flow of ingredients into the extruder for uniform processing. |
Extruder Barrel |
Cylindrical housing where the extrusion process takes place, typically made of high-strength steel. |
Contains and guides the material as it is processed, heated, and formed by the rotating screws. |
Screw(s) |
Helical structure(s) that rotate within the barrel, available in single or twin configurations. |
Mixes, kneads, and conveys the raw materials through the barrel, applying pressure and heat. |
Heaters |
Electrical or steam-based heating elements that surround the barrel. |
Provide precise temperature control to facilitate cooking and gelatinization of the cereal dough. |
Die |
A metal plate with specific openings at the end of the barrel. |
Shapes the extruded material into the desired form of corn flakes. |
Cutter |
Mechanism with rotating blades located near the die. |
Cuts the extruded material into uniform flakes as it exits the die. |
Control System |
Electronic interface with programmable logic controllers (PLCs) and sensors. |
Monitors and adjusts operational parameters such as temperature, pressure, and screw speed. |
Cooling System |
Incorporates fans or water jackets to reduce the temperature of the extruded product. |
Ensures the product is cooled quickly to maintain its shape and quality. |
Drive Motor |
Electric motor that powers the rotation of the screw(s). |
Provides the necessary torque and speed to the screws for effective material processing. |
Gearbox |
Mechanical component that adjusts the speed and torque from the drive motor to the screws. |
Transmits and modifies the motor's power to optimize the extrusion process. |
Vacuum Venting System |
Feature that removes air and moisture from the material during extrusion. |
Enhances product density and texture by eliminating unwanted air pockets and excess moisture. |
Instrumentation |
Various sensors and gauges for monitoring pressure, temperature, and other critical parameters. |
Provides real-time data to ensure consistent production quality and operational efficiency. |
Steps in the Corn Flakes Extruder Production Line
Raw Material Selection and Preparation
The first step in the Breakfast Cereal Corn Flakes Extruder Production Line is the selection and preparation of raw materials. High-quality corn is essential for producing superior corn flakes. The corn undergoes cleaning to remove impurities and is then ground into a consistent particle size to ensure uniform cooking and extrusion.
Cooking and Extrusion Process
In this stage, the prepared corn mixture is fed into the extruder. The extruder, equipped with screws and a heated barrel, cooks the material under controlled temperature and pressure conditions. This process gelatinizes the starches, enhancing the texture and digestibility of the final product. The cooking process can utilize either steam or dry heat, depending on the desired characteristics of the corn flakes.
Shaping and Forming Corn Flakes
Once the material is cooked, it passes through a die, which shapes it into the desired form. The extruded material is then cut into uniform pieces by a cutter located at the end of the extruder. This step ensures that each corn flake is consistent in size and shape, which is crucial for packaging and consumer satisfaction.
Drying and Toasting
The shaped corn flakes are then dried to reduce their moisture content. This can be achieved using air dryers or drum dryers, depending on the production line setup. After drying, the corn flakes are toasted to achieve the perfect crispiness. The toasting process also enhances the flavor and color of the flakes, making them more appealing to consumers.
Flavoring and Coating
In this stage, the corn flakes can be flavored or coated with various ingredients to meet different market demands. Sweet, savory, and nutritious coatings are applied using specialized equipment. This step allows manufacturers to diversify their product offerings and cater to varying consumer preferences.
Packaging and Quality Control
The final step in the Breakfast Cereal Corn Flakes Extruder Production Line is packaging and quality control. The corn flakes are packed using automated packaging solutions that ensure freshness and convenience. Quality control measures, including weight checks, moisture tests, and visual inspections, are implemented to ensure that the product meets industry standards and consumer expectations.
Technological Advancements in Extruder Machines
The Breakfast Cereal Corn Flakes Extruder Production Line has seen significant technological advancements in recent years, enhancing efficiency, product quality, and operational flexibility. These innovations are crucial for meeting the growing demands of the breakfast cereal market.
1. Enhanced Temperature Control Systems
Modern extruders are equipped with advanced temperature control systems that allow for precise heating throughout the extrusion process. Improved sensors and control algorithms ensure uniform cooking, which is essential for achieving the desired texture and consistency in corn flakes. Accurate temperature management also minimizes the risk of overcooking or undercooking the product.
2. High-Efficiency Screw Designs
Recent developments in screw design have led to more efficient mixing, kneading, and conveying of raw materials. High-efficiency screws reduce energy consumption and increase throughput, enabling manufacturers to produce larger quantities of corn flakes without compromising on quality. These designs also facilitate the processing of various ingredient blends, enhancing the versatility of the extruder production line.
3. Automated Process Monitoring and Control
Automation has revolutionized the Breakfast Cereal Corn Flakes Extruder Production Line by integrating sophisticated monitoring and control systems. Programmable logic controllers (PLCs) and human-machine interfaces (HMIs) provide real-time data on key parameters such as pressure, temperature, and moisture content. This data-driven approach allows for immediate adjustments, ensuring consistent product quality and reducing waste.
4. Eco-Friendly and Sustainable Practices
Sustainability is a major focus in the food manufacturing industry. Modern extruders are designed to be more energy-efficient and to minimize waste. Innovations such as energy recovery systems and recyclable materials in machine construction contribute to more sustainable production practices. These eco-friendly advancements not only benefit the environment but also appeal to environmentally conscious consumers.
5. Modular and Flexible Extruder Configurations
To meet diverse production needs, extruders now offer modular and flexible configurations. Manufacturers can customize their extruder machines with interchangeable components tailored to specific product requirements. This flexibility allows for easy adaptation to new recipes or changes in production volume, making it possible to quickly respond to market trends.
6. Improved Sanitation and Hygiene Standards
Advances in extruder design also include enhanced sanitation and hygiene features. Quick-release mechanisms and streamlined surfaces make cleaning and maintenance more efficient, reducing downtime between production runs. Compliance with stringent food safety regulations is ensured through materials and designs that minimize contamination risks.
7. Integration with IoT and Industry 4.0
The integration of the Internet of Things (IoT) and Industry 4.0 technologies has brought a new level of connectivity and intelligence to the Breakfast Cereal Corn Flakes Extruder Production Line. Smart sensors, data analytics, and remote monitoring capabilities enable predictive maintenance and optimized production workflows. These technologies enhance operational efficiency and provide valuable insights for continuous improvement.
Maintenance and Troubleshooting
Maintenance and troubleshooting are crucial aspects of managing a Breakfast Cereal Corn Flakes Extruder Production Line efficiently. Proper maintenance ensures optimal performance and longevity of the equipment, while effective troubleshooting minimizes downtime and production losses.
Importance of Regular Maintenance
Regular maintenance of the extruder and associated equipment is essential to prevent breakdowns and maintain consistent production. Key maintenance tasks include:
1. Cleaning and Lubrication: Regular cleaning of the extruder barrel, screws, and die ensures residue buildup does not affect product quality. Proper lubrication of moving parts reduces friction and wear, extending component life.
2. Inspection of Wear Parts: Periodically inspect wear parts such as screw elements, barrels, and seals. Replace worn parts promptly to prevent operational issues and maintain product consistency.
3. Calibration of Sensors and Controls: Verify the accuracy of temperature, pressure, and other sensors regularly. Calibration ensures precise control over the extrusion process, optimizing product quality.
4. Check for Leaks and Loose Connections: Inspect hydraulic and pneumatic systems for leaks and tighten any loose connections. Leaks can lead to reduced efficiency and potential safety hazards.
5. Training and Skill Development: Provide ongoing training for maintenance personnel to stay updated on new technologies and best practices. Well-trained staff can identify and resolve issues more effectively.
Troubleshooting Common Issues
Effective troubleshooting requires a systematic approach to identify and resolve issues quickly. Common problems in Breakfast Cereal Corn Flakes Extruder Production Lines include:
1. Uneven Extrusion or Flakes: Check for inconsistent material feeding or improper screw alignment. Adjust feeding rates and inspect screws for damage or wear.
2. Overheating or Underheating: Monitor temperature settings and ensure heating elements are functioning correctly. Clean heat transfer surfaces to improve efficiency.
3. Excessive Noise or Vibration: Investigate loose bolts, worn bearings, or misaligned components. Address mechanical issues promptly to prevent further damage.
4. Product Quality Issues: Analyze raw material quality, processing parameters, and equipment settings. Make adjustments to achieve desired product characteristics such as texture and color.
5. Electrical or Control System Malfunctions: Diagnose electrical faults using diagnostic tools and reset or replace faulty components. Ensure all safety protocols are followed during troubleshooting.
Implementing Preventive Measures
To minimize the need for troubleshooting, preventive maintenance measures should be prioritized. Develop a comprehensive maintenance schedule and adhere to manufacturer recommendations for servicing extruder machines and associated equipment. Document maintenance activities and track equipment performance metrics to identify trends and anticipate potential issues.
By prioritizing maintenance and implementing effective troubleshooting strategies, manufacturers can optimize the performance of their Breakfast Cereal Corn Flakes Extruder Production Line. This proactive approach not only enhances operational efficiency but also contributes to consistent product quality and customer satisfaction.
References
The following are five authoritative foreign literature websites in the field of corn flakes making machines:
1. SpringerLink
Website: [https://link.springer.com/]
2.IEEE Xplore Digital Library
Website: [https://ieeexplore.ieee.org/]
3. GEA Group
Website: [https://www.gea.com]
4. Sollich KG
Website: [https://www.sollich.com]
5. Bühler Group
Website: [https://www.buhlergroup.com]