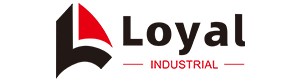
- Shandong Loyal Industrial Co.,Ltd.
- Macaroni Production Machine Instant Noodle Machine Biscuit Making Machine

Home> Company News> The Ultimate Guide to Protein Bar Machine in 2024

The Ultimate Guide to Protein Bar Machine in 2024
2024-07-01 14:09:09Introduction
In 2024, the demand for high-quality protein bars has surged, driving significant advancements in manufacturing technologies. The cornerstone of this evolution is the protein bar machine, which has become indispensable for producers aiming to meet consumer expectations for taste, texture, and nutritional value. Modern protein bar machines offer enhanced capabilities that ensure consistent production, improve efficiency, and uphold stringent quality standards. These machines are not just about mixing and forming; they integrate cutting-edge automation, IoT technologies, and precision engineering to streamline the entire manufacturing process. As the protein bar market continues to expand, understanding the latest innovations in protein bar machinery is crucial for staying competitive and fulfilling market needs efficiently.
Types of Protein Bar Machines
In the rapidly evolving world of protein bar manufacturing, the selection of the right protein bar machine is critical to achieving both efficiency and product quality. Various types of machines are designed to handle different stages of production, each tailored to specific needs and scales of operation. The primary categories of protein bar machines include:
1. Mixing and Blending Machines: These machines are essential for combining ingredients uniformly, ensuring consistent texture and taste across batches. Advanced models incorporate automated controls for precise ingredient ratios and mixing times.
2. Forming and Shaping Machines: These machines take the mixed ingredients and shape them into bars. They offer flexibility in producing different bar sizes and shapes, catering to diverse market demands. Automated forming machines enhance production speed while maintaining accuracy in size and weight.
3. Extrusion Machines: Extruders are used to form continuous bars that are then cut to size. This type of protein bar machine is ideal for high-volume production, providing consistent output and reducing manual labor.
4. Cutting and Slicing Machines: After extrusion or forming, the bars need to be cut to precise dimensions. Cutting machines ensure uniformity in bar size, which is crucial for packaging and consumer satisfaction. Some advanced models also include features for cutting bars with various inclusions like nuts or chocolate chips.
5. Coating and Enrobing Machines: For protein bars that require an outer layer, coating machines apply chocolate, yogurt, or other coatings evenly. These machines must maintain precise temperature and viscosity controls to achieve a consistent coating.
6. Cooling Tunnels: Post-coating, the bars need to be cooled quickly to set the coating properly. Cooling tunnels provide a controlled environment to ensure rapid and uniform cooling, essential for maintaining product quality.
7. Packaging Machines: Once the protein bars are manufactured, they need to be packaged efficiently. Packaging machines range from simple wrappers to complex systems that handle multiple packaging formats and materials. These machines are crucial for protecting product integrity and extending shelf life.
Each type of protein bar machine plays a pivotal role in the manufacturing process, and selecting the right combination of equipment can significantly enhance production efficiency and product quality. As the demand for protein bars continues to grow, investing in advanced machinery tailored to specific production needs will be a key factor in staying competitive in the market.
Key Features and Functions
In 2024, the protein bar manufacturing industry is rapidly evolving, driven by technological advancements and increasing consumer demand for high-quality protein bars. Understanding the key features and functions of a protein bar machine is essential for manufacturers looking to stay competitive. This guide provides an authoritative overview of what to look for in the latest protein bar machines.
High Precision Mixing and Blending
One of the fundamental aspects of any protein bar machine is its ability to mix and blend ingredients with high precision. Modern machines are equipped with advanced mixers that ensure uniform distribution of ingredients, which is crucial for maintaining the consistency and quality of protein bars. These mixers often come with programmable settings, allowing for precise control over mixing times and speeds, thus accommodating various recipes and ingredient compositions.
Efficient Forming and Shaping Mechanisms
The forming and shaping of protein bars is another critical function of the protein bar machine. State-of-the-art machines utilize automated forming technologies that can produce bars of consistent shape and size. These mechanisms often include adjustable molds and extrusion heads that can be customized to create different bar shapes and sizes, catering to diverse market demands. The efficiency of these systems not only enhances production speed but also ensures minimal waste, contributing to overall cost savings.
Advanced Baking and Cooling Systems
For protein bars that require baking, modern machines are equipped with sophisticated baking systems that ensure even heat distribution and precise temperature control. These systems often feature convection ovens that can handle large volumes of bars simultaneously. Post-baking, rapid cooling systems are essential to quickly bring the bars to the desired temperature, preventing any degradation of ingredients and maintaining the bar’s texture and nutritional value.
Integrated Packaging Solutions
Packaging is a critical component in the protein bar manufacturing process. Today's protein bar machines often come with integrated packaging solutions that streamline the packaging process, ensuring that the bars are wrapped efficiently and hygienically. These solutions can include flow wrap machines, vacuum packaging, and automated carton sealing systems, which not only protect the product but also extend its shelf life. The integration of packaging within the protein bar machine setup reduces the need for additional equipment and labor, thereby optimizing production efficiency.
User-Friendly Interfaces and Controls
Modern protein bar machines are designed with user-friendly interfaces that simplify the operation and monitoring of the manufacturing process. Touchscreen controls, real-time monitoring systems, and automated alerts for maintenance and troubleshooting are some of the features that enhance user experience. These interfaces allow operators to easily adjust settings, monitor production in real-time, and ensure that the machine operates at optimal efficiency.
Compliance with Food Safety Standards
Ensuring compliance with food safety standards is paramount in the protein bar manufacturing industry. Contemporary protein bar machines are constructed with materials that meet stringent hygiene standards, such as stainless steel, which is resistant to corrosion and easy to clean. Additionally, these machines often include features like automated cleaning systems and sanitary design principles that minimize contamination risks. Compliance with regulations such as FDA, USDA, and European standards is a critical feature of these machines, ensuring that the produced bars are safe for consumption.
Quality Control and Safety Measures
When it comes to producing protein bars, quality control and safety measures are paramount. Ensuring that each protein bar machine operates at optimal efficiency and produces consistent, high-quality products is crucial for maintaining a competitive edge in the market. This section delves into the critical aspects of quality control and safety measures that should be implemented in the protein bar manufacturing process.
1. Quality Control Standards and Protocols
Implementing stringent quality control standards is essential to guarantee the uniformity and excellence of protein bars. Each protein bar machine should undergo regular inspections and maintenance to ensure it operates within specified parameters. Utilizing automated inspection systems can significantly enhance the precision and reliability of quality checks. These systems can detect inconsistencies in size, shape, and weight, ensuring each bar meets the set standards.
2. Safety Measures in Protein Bar Manufacturing
Safety measures are equally vital in the manufacturing process. Ensuring that the protein bar machine is equipped with safety guards and emergency stop mechanisms can prevent accidents and injuries. Regular training sessions for operators on proper handling and emergency procedures can further enhance workplace safety. Additionally, adhering to food safety regulations, such as the FDA's Current Good Manufacturing Practices (CGMPs), helps prevent contamination and ensures the safety of the end product.
3. Hygiene and Sanitation Protocols
Maintaining high standards of hygiene and sanitation is crucial in preventing microbial contamination. The protein bar machine should be designed for easy cleaning and sanitization. Implementing Clean-In-Place (CIP) systems can streamline the cleaning process, reducing downtime and ensuring thorough sanitation. Regular monitoring and documentation of cleaning procedures can help maintain compliance with food safety standards.
4. Traceability and Record-Keeping
Traceability is a key component of quality control. Keeping detailed records of the production process, from raw materials to finished products, allows manufacturers to trace any issues back to their source. This is particularly important in the event of a product recall. Implementing a robust traceability system within the protein bar machine's operation can ensure quick and efficient identification of potential problems, thereby minimizing risks and maintaining consumer trust.
5. Continuous Improvement
Continuous improvement is essential in maintaining high standards of quality and safety. Regularly reviewing and updating quality control and safety measures based on the latest industry standards and technological advancements can help manufacturers stay ahead of potential issues. Encouraging feedback from operators and investing in ongoing training can also contribute to a culture of continuous improvement.
Maintenance and Downtime Management
Proper maintenance of protein bar machines is crucial to ensure optimal performance and longevity. Regular upkeep not only enhances efficiency but also minimizes downtime, ensuring continuous production without interruptions. Here’s a comprehensive guide to effectively manage maintenance and downtime for protein bar machines in 2024.
1. Scheduled Maintenance Procedures
Scheduled maintenance plays a pivotal role in the upkeep of protein bar machines. Establishing a routine maintenance schedule is essential to prevent unexpected breakdowns and maintain consistent quality output. Key maintenance tasks include:
- Cleaning and Sanitization: Regular cleaning of all machine components to remove residue and prevent contamination is vital. Use industry-approved cleaning agents and follow manufacturer guidelines to ensure hygiene standards are met.
- Lubrication of Moving Parts: Lubricate mechanical components to reduce friction and wear, prolonging the lifespan of critical parts such as conveyor belts, cutting blades, and motors.
- Inspection of Wear and Tear: Periodically inspect components for signs of wear and tear, such as fraying belts or worn-out seals. Replace these parts promptly to prevent operational disruptions.
2. Predictive Maintenance Technologies
Advancements in technology have introduced predictive maintenance tools that leverage data analytics and sensors to forecast potential equipment failures. Implementing these technologies allows for proactive maintenance rather than reactive repairs, thereby reducing unplanned downtime significantly.
- Condition Monitoring Systems: Utilize sensors to monitor equipment performance in real-time. These systems can detect anomalies, such as abnormal vibrations or temperature fluctuations, signaling potential issues before they escalate.
- Predictive Analytics: Analyze historical data and performance trends to predict maintenance requirements accurately. By identifying patterns indicative of impending failures, proactive measures can be taken to mitigate risks and optimize machine uptime.
3. Training and Skill Development
Ensure that personnel responsible for machine operation and maintenance receive comprehensive training. Equip them with the necessary skills to perform routine inspections, conduct minor repairs, and adhere to safety protocols effectively.
- Training Programs: Offer regular training sessions conducted by qualified professionals or through manufacturer-provided resources. Focus on operational best practices, safety guidelines, and troubleshooting techniques specific to protein bar machines.
- Skill Enhancement: Encourage continuous skill development among maintenance staff to keep pace with technological advancements and industry standards. Familiarity with the latest machinery updates and maintenance protocols is essential for efficient operations.
4. Downtime Management Strategies
Despite proactive maintenance efforts, downtime can still occur due to unforeseen circumstances. Implement effective downtime management strategies to minimize production losses and maximize operational efficiency.
- Root Cause Analysis: Conduct thorough root cause analysis to identify the underlying reasons for downtime incidents. Addressing root causes enables preventive measures to mitigate recurrence.
- Emergency Response Plan: Develop and communicate an emergency response plan outlining procedures to follow during equipment failures or breakdowns. Prompt action can expedite recovery and minimize downtime impact.
- Inventory Management: Maintain adequate spare parts inventory to facilitate quick repairs and replacements. Collaborate closely with suppliers to ensure timely availability of critical components, reducing downtime associated with parts procurement.
Future Trends and Innovations in Protein Bar Machines
In 2024, the landscape of protein bar machines is poised for significant advancements, driven by technological innovations and evolving consumer preferences. Manufacturers are increasingly focusing on enhancing efficiency, flexibility, and sustainability in their machinery to meet the rising demand for nutritious and convenient snack options. Here are some key trends and innovations shaping the future of protein bar machines:
1. Integration of Smart Technologies
The future of protein bar machines lies in their ability to integrate smart technologies. Manufacturers are incorporating IoT (Internet of Things) capabilities to enable real-time monitoring and control of production processes. This allows for predictive maintenance, optimizing operational efficiency, and minimizing downtime. Smart machines can adjust parameters autonomously based on real-time data, ensuring consistent product quality and reducing waste.
2. Enhanced Customization Capabilities
Consumers are increasingly seeking personalized nutrition options, and protein bar machines are adapting to this trend by offering enhanced customization capabilities. Modern machines allow manufacturers to adjust ingredients, textures, and shapes seamlessly, catering to diverse dietary preferences and nutritional requirements. This flexibility not only enhances consumer satisfaction but also enables brands to innovate and differentiate their product offerings in a competitive market.
3. Focus on Sustainability
Sustainability is a driving force in the evolution of protein bar machines. Manufacturers are adopting eco-friendly practices by optimizing energy usage, reducing water consumption, and minimizing waste generation throughout the production process. Innovative technologies such as recyclable packaging materials and biodegradable ingredients are becoming integral to sustainable manufacturing practices, aligning with consumer demand for environmentally responsible products.
4. Advances in Production Speed and Efficiency
Efficiency remains a cornerstone of modern protein bar machines. Continuous advancements in automation and robotics are streamlining production processes, significantly increasing output rates without compromising on quality. High-speed machines equipped with precision cutting and molding capabilities ensure consistent product dimensions and texture, meeting stringent industry standards while maximizing operational efficiency.
5. Embrace of Clean Label Ingredients
As consumer awareness of health and wellness grows, there is a pronounced shift towards clean label ingredients in protein bars. Machine manufacturers are adapting by designing equipment that can handle a wide range of natural ingredients, including whole grains, nuts, and plant-based proteins. The emphasis is on maintaining ingredient integrity and nutritional value throughout the manufacturing process, ensuring transparency and trust among health-conscious consumers.
6. Adaptation to Regulatory Requirements
The regulatory landscape governing food production continues to evolve globally. Protein bar machine manufacturers are proactively designing equipment that complies with stringent food safety standards and regulatory requirements. This includes implementing hygienic design principles, ensuring traceability of ingredients, and facilitating thorough cleaning and sanitation procedures to mitigate contamination risks.
Reference
The following are five authoritative foreign literature websites in the field of Industrial food machinery:
1. Food Engineering Magazine
Website: https://www.foodengineeringmag.com/
2.Food Processing Magazine
Website: https://www.foodprocessing.com/
3.Journal of Food Engineering
Website:https://www.journals.elsevier.com/journal-of-food-engineering
4. Food Manufacturing Magazine
Website:https://www.foodmanufacturing.com/
5. International Journal of Food Science & Technology
Website:https://onlinelibrary.wiley.com/