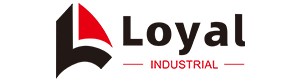
- Shandong Loyal Industrial Co.,Ltd.
- Macaroni Production Machine Instant Noodle Machine Biscuit Making Machine

Home> Company News> The Ultimate Guide to Snack Bar Manufacturing Machine in 2024

The Ultimate Guide to Snack Bar Manufacturing Machine in 2024
2024-07-01 14:26:55Introduction
In the rapidly evolving world of food production, snack bars have surged in popularity due to their convenience, nutritional benefits, and variety of flavors. As demand grows, manufacturers are continuously seeking advanced solutions to optimize production efficiency and maintain high-quality standards. Enter the snack bar manufacturing machine, a pivotal piece of equipment that revolutionizes the way snack bars are produced.
A snack bar manufacturing machine is designed to handle the intricate processes of making snack bars, from mixing and forming to cutting and packaging. These machines are engineered to ensure consistency, enhance production speed, and maintain stringent hygiene standards, all while being adaptable to various recipes and ingredient combinations. In 2024, the advancements in these machines are set to address the increasing complexities and demands of the snack bar market.
The purpose of this guide is to provide a comprehensive overview of the latest developments in snack bar manufacturing machines, their features, and how they can significantly benefit your production line. Whether you are a seasoned manufacturer or new to the snack bar industry, understanding the capabilities and innovations of these machines will empower you to make informed decisions that can enhance your operational efficiency and product quality.
Key Features of Modern Snack Bar Manufacturing Machines
Modern snack bar manufacturing machines have revolutionized the food processing industry, offering unparalleled efficiency, precision, and versatility. As the demand for snack bars continues to surge globally, these machines have become indispensable for manufacturers aiming to meet consumer needs while maintaining high standards of quality and consistency.
1. Advanced Automation and Integration
One of the most significant advancements in snack bar manufacturing machines is the integration of advanced automation technologies. These machines are equipped with programmable logic controllers (PLCs) and human-machine interfaces (HMIs) that facilitate seamless operation, monitoring, and control. Automation not only enhances production speed but also reduces human error, ensuring consistent product quality.
2. Versatility in Product Formulation
Modern snack bar manufacturing machines are designed to handle a wide range of ingredients and formulations. Whether it's granola bars, protein bars, or fruit and nut bars, these machines can accommodate various recipes with ease. This versatility is achieved through adjustable settings and interchangeable components that allow manufacturers to switch between different products quickly and efficiently.
3. Precision and Consistency
Consistency in size, shape, and weight is crucial in snack bar production. Today's machines utilize state-of-the-art cutting and forming technologies to ensure each bar meets exact specifications. Precision cutters and molds are essential for maintaining uniformity, which is critical for both consumer satisfaction and compliance with industry standards.
4. High Throughput and Efficiency
Efficiency is a key consideration for any manufacturing operation. Modern snack bar manufacturing machines are engineered to maximize throughput while minimizing downtime. High-speed production lines can produce thousands of bars per hour, significantly boosting productivity. Additionally, features such as quick changeover and easy cleaning help maintain continuous operation with minimal interruption.
5. Hygienic Design and Food Safety
Food safety is paramount in the production of snack bars. Modern machines are designed with hygiene in mind, featuring stainless steel construction and smooth surfaces that prevent contamination. Many machines also incorporate automatic cleaning systems that ensure thorough sanitation between production runs. Compliance with food safety regulations, such as HACCP (Hazard Analysis Critical Control Point) and FDA guidelines, is a standard feature in contemporary snack bar manufacturing equipment.
6. Energy Efficiency and Sustainability
As sustainability becomes increasingly important, manufacturers are seeking equipment that minimizes environmental impact. Modern snack bar manufacturing machines are designed to be energy-efficient, utilizing advanced technologies that reduce power consumption. Additionally, many machines are built to be durable and require less maintenance, which contributes to their overall sustainability.
7. Scalability and Customization
Every snack bar manufacturer has unique needs, and modern machines offer a high degree of scalability and customization. Whether a business is just starting or looking to expand its production capacity, these machines can be tailored to specific requirements. Customizable features and modular designs allow manufacturers to scale their operations and adapt to changing market demands seamlessly.
Types of Snack Bar Manufacturing Machines
The snack bar manufacturing industry is diverse, with various machines designed to cater to different production needs. Understanding the types of snack bar manufacturing machines available in 2024 is crucial for optimizing your production line. Here, we delve into the primary categories of these machines, highlighting their features and applications.
Mixing Machines
Mixing machines are foundational to the snack bar manufacturing process. These machines are designed to uniformly combine ingredients, ensuring a consistent texture and flavor in the final product. Modern mixing machines come equipped with advanced features like variable speed controls, programmable settings, and robust mixing blades capable of handling a wide range of ingredients, from nuts and seeds to syrups and powders. They are essential for producing homogeneous mixtures, which are critical for the quality of snack bars.
Forming Machines
Forming machines play a pivotal role in shaping the mixture into the desired snack bar shape. These machines are designed with precision to ensure each bar is consistent in size and weight, which is vital for both quality control and packaging. The latest forming machines incorporate technologies such as adjustable molds, automated feeding systems, and quick-change tooling, allowing manufacturers to switch between different snack bar shapes and sizes with minimal downtime.
Cooling Conveyors
Once the snack bars are formed, they need to be cooled efficiently to maintain their shape and texture. Cooling conveyors are specialized machines that transport the freshly formed bars through a controlled cooling environment. These machines ensure that the snack bars cool uniformly, preventing any deformation or stickiness. Advanced cooling conveyors offer adjustable speed controls, temperature regulation, and even air circulation systems to enhance the cooling process.
Coating Machines
For snack bars that require an additional layer of coating, such as chocolate or yogurt, coating machines are indispensable. These machines are designed to evenly apply coatings to snack bars, enhancing their flavor and visual appeal. Modern coating machines feature precision nozzles, temperature control systems, and automated drying tunnels to ensure a uniform and high-quality coating process. This step is crucial for creating premium snack bars that meet consumer expectations.
Cutting Machines
Cutting machines are essential for portioning large slabs of snack bars into individual pieces. These machines use advanced cutting technologies such as ultrasonic blades, rotary cutters, and guillotine cutters to achieve clean, precise cuts without damaging the bars. Cutting machines are designed to handle various bar sizes and shapes, ensuring versatility and efficiency in the production process. They also often include features like adjustable cutting speeds, programmable cutting patterns, and waste minimization systems.
Packaging Machines
The final step in the snack bar manufacturing process involves packaging, which is critical for product preservation and presentation. Packaging machines for snack bars come in various types, including flow wrappers, tray sealers, and vacuum packaging machines. These machines are equipped with features like automated feeding, sealing, and labeling, ensuring that the snack bars are packaged quickly and hygienically. High-speed packaging machines are designed to handle large volumes, making them ideal for large-scale production operations.
Choosing the Right Snack Bar Manufacturing Machine
Choosing the right snack bar manufacturing machine is critical for optimizing production efficiency, ensuring product quality, and maintaining compliance with industry standards. This decision involves evaluating several key factors, each influencing the overall performance and cost-effectiveness of your production line. Below, we delve into the primary considerations to guide you in selecting the most suitable snack bar manufacturing machine for your needs.
Production Capacity
The production capacity of a snack bar manufacturing machine is a fundamental criterion. It determines how many units can be produced within a given timeframe. Depending on the scale of your operations, you might require a machine capable of producing thousands of snack bars per hour. High-capacity machines are ideal for large-scale manufacturers, while smaller producers may benefit from machines with lower capacities that offer greater flexibility and reduced energy consumption. Ensuring that the machine’s capacity aligns with your production goals will prevent bottlenecks and maximize efficiency.
Versatility and Flexibility
In the dynamic snack bar industry, the ability to adapt to changing market demands is invaluable. A versatile snack bar manufacturing machine can handle various recipes and bar sizes, accommodating different ingredients and formulations. Machines that offer easy adjustments and quick changeovers between different products enhance operational flexibility, allowing manufacturers to respond swiftly to consumer trends and demands. This adaptability not only extends the machine's utility but also supports innovation in product development.
Automation and Technology Integration
Modern snack bar manufacturing machines incorporate advanced automation and technology features. Automated systems reduce labor costs, minimize human error, and ensure consistent product quality. Features such as programmable logic controllers (PLCs), touch screen interfaces, and real-time monitoring systems enhance operational control and efficiency. Integration with other production line components, such as mixers, depositors, and packaging machines, creates a seamless and cohesive manufacturing process, further boosting productivity and reliability.
Quality and Durability
Investing in a high-quality, durable snack bar manufacturing machine is essential for long-term operational success. Machines constructed from robust, food-grade materials withstand the rigors of continuous use and comply with stringent hygiene standards. Look for equipment from reputable manufacturers known for their engineering excellence and reliable after-sales support. A durable machine reduces downtime and maintenance costs, ensuring uninterrupted production and a higher return on investment.
Compliance with Safety and Regulatory Standards
Compliance with safety and regulatory standards is non-negotiable in the food manufacturing industry. Your snack bar manufacturing machine must meet local and international food safety regulations, including those set by the FDA, USDA, and other relevant authorities. Features such as easy-to-clean surfaces, sanitary design, and safety guards protect both the product and the operators. Ensuring regulatory compliance not only safeguards your brand's reputation but also avoids costly legal issues and recalls.
Cost Considerations
While the initial investment in a snack bar manufacturing machine can be substantial, it is crucial to consider the total cost of ownership. Factors such as energy efficiency, maintenance requirements, and the availability of spare parts influence the long-term costs. Machines that offer energy-saving features and require minimal maintenance can lead to significant cost savings over time. Additionally, evaluating the machine's warranty and the manufacturer's support services can provide peace of mind and protect your investment.
Technological Innovations in Snack Bar Manufacturing
The snack bar manufacturing industry is witnessing a technological revolution, driven by advancements in automation, precision engineering, and data integration. The latest innovations in snack bar manufacturing machines are setting new standards for efficiency, consistency, and product quality. These cutting-edge technologies not only streamline production processes but also ensure that manufacturers can meet the evolving demands of consumers and regulatory standards.
Automation and Robotics
One of the most significant technological innovations in snack bar manufacturing is the integration of automation and robotics. Modern snack bar manufacturing machines are equipped with advanced robotic systems that handle various stages of production, from mixing and forming to cutting and packaging. These systems enhance precision and consistency, reducing human error and increasing production speed. Automated systems also enable manufacturers to switch between different product lines quickly, offering greater flexibility and reducing downtime.
Precision Engineering
Precision engineering is another critical advancement in snack bar manufacturing machines. These machines are now designed with high-precision components that ensure uniformity in size, shape, and weight of each snack bar. Precision cutting tools and molds are used to create consistent products, which is essential for maintaining quality and meeting consumer expectations. Enhanced precision also contributes to better resource utilization, minimizing waste and optimizing production efficiency.
Advanced Mixing and Forming Technologies
The mixing and forming stages are crucial in snack bar manufacturing, and recent innovations have significantly improved these processes. Modern snack bar manufacturing machines feature advanced mixing technologies that ensure homogeneity and consistency of ingredients. High-shear mixers and continuous mixers are commonly used to achieve uniform blends, which is vital for the taste and texture of the final product. In the forming stage, advanced extrusion and molding technologies allow for the creation of diverse shapes and sizes, catering to a wide range of consumer preferences.
Data Integration and Analytics
Data integration and analytics have become indispensable in the modern snack bar manufacturing landscape. Advanced snack bar manufacturing machines are now equipped with sensors and IoT (Internet of Things) capabilities that collect real-time data throughout the production process. This data is analyzed to monitor equipment performance, predict maintenance needs, and optimize production parameters. By leveraging big data and analytics, manufacturers can achieve greater operational efficiency, reduce downtime, and enhance product quality.
Energy Efficiency and Sustainability
Sustainability is a growing concern in the food manufacturing industry, and technological innovations are playing a crucial role in addressing this issue. Modern snack bar manufacturing machines are designed with energy-efficient components and processes that reduce power consumption and environmental impact. Innovations such as regenerative braking systems, energy-efficient motors, and advanced heating and cooling technologies contribute to greener manufacturing practices. Additionally, these machines often incorporate sustainable materials and designs that facilitate recycling and waste reduction.
Customization and Personalization
The demand for customized and personalized snack bars is on the rise, and manufacturers are leveraging technological innovations to meet this trend. Advanced snack bar manufacturing machines offer greater flexibility in recipe formulation and production. Manufacturers can now easily adjust ingredients, flavors, and nutritional profiles to create bespoke products tailored to specific consumer needs and preferences. This capability not only enhances consumer satisfaction but also opens up new market opportunities for niche and specialty products.
Maintenance and Troubleshooting
Importance of Regular Maintenance
Ensuring the longevity and optimal performance of a snack bar manufacturing machine necessitates a rigorous and regular maintenance schedule. Regular maintenance helps prevent unexpected downtimes, which can be costly in terms of both time and productivity. By addressing potential issues before they escalate, manufacturers can maintain a steady production flow and meet their output targets consistently. Moreover, regular maintenance enhances the machine's efficiency, ensuring it operates at peak performance, which directly translates to higher quality snack bars and increased overall productivity.
Key Maintenance Procedures
1. Daily Cleaning: One of the most fundamental maintenance tasks is daily cleaning. Residual ingredients can cause buildup within the machinery, leading to potential contamination and mechanical issues. Using food-safe cleaning agents, all contact surfaces and internal components should be thoroughly cleaned at the end of each production cycle.
2. Lubrication: Proper lubrication of moving parts is essential to minimize wear and tear. It is crucial to use the correct type of lubricant recommended by the machine's manufacturer. Regular lubrication schedules should be adhered to, and operators should be trained to recognize signs of insufficient lubrication, such as unusual noises or increased friction.
3. Inspection and Replacement of Wear Parts: Snack bar manufacturing machines consist of numerous components that undergo wear over time. Regular inspections should be conducted to identify worn-out parts such as belts, bearings, and blades. Replacing these parts before they fail can prevent more significant mechanical issues and ensure continuous operation.
4. Calibration: To maintain the precision of snack bar sizes and weights, periodic calibration of the machine is necessary. Calibration ensures that the machine's settings align with the desired product specifications, maintaining consistency in product quality.
Troubleshooting Common Issues
1. Inconsistent Product Size: If the snack bars produced are inconsistent in size or weight, the first step is to check the calibration of the machine. Additionally, inspect for any blockages or buildup that might be obstructing the normal flow of ingredients.
2. Machine Jams: Frequent jams can be caused by several factors, including ingredient buildup, improper ingredient consistency, or worn-out components. Clearing any blockages and ensuring that the ingredients meet the required specifications can help resolve this issue. Regularly inspecting and replacing worn-out parts can also prevent jams.
3. Electrical Issues: Electrical problems can disrupt production and pose safety hazards. Common signs include irregular machine behavior, unexpected shutdowns, or error messages. In such cases, it is essential to check the electrical connections and wiring for any signs of wear or damage. Consulting with a qualified technician to diagnose and repair electrical faults is advisable.
4. Reduced Efficiency: If the machine is operating slower than usual or consuming more energy, it may indicate underlying issues such as insufficient lubrication, worn-out parts, or misalignment. Conducting a thorough inspection and addressing these factors can help restore the machine's efficiency.
Training and Documentation
Proper training of personnel is critical to effective maintenance and troubleshooting. Operators should be well-versed in the machine's operation, maintenance procedures, and safety protocols. Additionally, maintaining comprehensive documentation of maintenance activities, inspections, and repairs can provide valuable insights into the machine's performance over time and help in identifying recurring issues.
Regulatory Compliance in Snack Bar Manufacturing Machines
Snack bar manufacturing machines are subject to rigorous regulatory frameworks to ensure food safety and quality. Regulatory bodies such as the FDA (Food and Drug Administration) in the United States and similar agencies globally set forth guidelines that manufacturers must follow. These guidelines encompass various aspects, including:
1. Material Safety: One of the primary concerns is the materials used in the construction of snack bar manufacturing machines. Components in direct contact with food must be made from food-grade materials that are non-toxic, corrosion-resistant, and easy to clean. Compliance with materials like stainless steel, approved plastics, and food-safe coatings is essential to prevent contamination and ensure product integrity.
2. Sanitary Design: The design of snack bar manufacturing machines must facilitate easy cleaning and sanitization to prevent bacterial growth and cross-contamination. Machines should have smooth surfaces without crevices where food particles can accumulate, and they should be designed to allow access for thorough cleaning procedures.
3. Operational Safety: Safety features are critical to prevent accidents during machine operation. This includes ensuring guards and safety interlocks are in place to protect operators from moving parts and potential hazards. Emergency stop mechanisms and proper labeling of controls also contribute to operational safety standards.
4. Electrical and Mechanical Safety: Compliance with electrical and mechanical safety standards is vital to prevent hazards such as electrical shock, fire, or mechanical failure. Machines should be tested and certified to meet relevant safety standards specific to their operating environment and intended use.
Meeting Food Safety Standards
In addition to regulatory compliance, snack bar manufacturing machines must adhere to food safety standards that ensure the final product is safe for consumption. This involves:
1. HACCP (Hazard Analysis Critical Control Points): Implementing a HACCP plan is essential to identify and control potential hazards throughout the manufacturing process, from raw materials to finished products. Critical control points include temperature controls, sanitation procedures, and allergen management.
2. Good Manufacturing Practices (GMP): Following GMP guidelines ensures that manufacturing processes are conducted in a hygienic and controlled manner. This includes maintaining cleanliness, training staff in hygiene practices, and monitoring the production environment to prevent contamination.
3. Allergen Control: Snack bar manufacturing machines should be designed and operated to prevent cross-contact with allergens. This includes dedicated equipment for allergen-containing ingredients, proper labeling, and effective cleaning procedures to minimize allergen risks.
Reference
The following are five authoritative foreign literature websites in the field of Industrial food machinery:
1. Food Engineering Magazine
Website: https://www.foodengineeringmag.com/
2.Food Processing Magazine
Website: https://www.foodprocessing.com/
3.Journal of Food Engineering
Website:https://www.journals.elsevier.com/journal-of-food-engineering
4. Food Manufacturing Magazine
Website:https://www.foodmanufacturing.com/
5. International Journal of Food Science & Technology
Website:https://onlinelibrary.wiley.com/