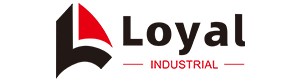
- Shandong Loyal Industrial Co.,Ltd.
- Macaroni Production Machine Instant Noodle Machine Biscuit Making Machine

Home> Company News> The Ultimate Guide to corn flakes making machine process line in 2024

The Ultimate Guide to corn flakes making machine process line in 2024
2024-07-05 16:12:30Evolution of Corn Flakes Production
Historical Background of Corn Flakes
Corn flakes, a staple breakfast cereal enjoyed by millions worldwide, have an interesting history that dates back to the late 19th century. Originally created by Dr. John Harvey Kellogg and his brother Will Keith Kellogg, corn flakes were part of a health-focused diet at the Battle Creek Sanitarium in Michigan. The Kellogg brothers' innovation quickly gained popularity, leading to the establishment of a dedicated production facility. This marked the beginning of the mass production of corn flakes, laying the groundwork for the cereal industry we know today.
Traditional Methods of Corn Flakes Production
In the early days, corn flakes were produced using labor-intensive methods that required significant manual effort. The process involved cooking corn grits in large vats, followed by rolling the cooked mixture into thin sheets. These sheets were then toasted in ovens to achieve the desired crispness. While effective, this traditional method was time-consuming and required a large workforce, making it difficult to scale up production to meet growing demand.
Transition to Automated Processes
The advent of industrialization and advancements in food processing technology brought significant changes to the production of corn flakes. The introduction of mechanized equipment revolutionized the industry, allowing for higher production volumes and improved consistency in product quality. Early automation efforts focused on mechanizing individual steps in the process, such as cooking and toasting, which led to increased efficiency.
As technology continued to evolve, the concept of a fully automatic corn flakes making machine process line emerged. This comprehensive system integrated various stages of production into a seamless, automated workflow. By automating the entire process, from raw material handling to packaging, manufacturers were able to achieve unprecedented levels of efficiency and precision.
Key Features of a Fully Automatic Corn Flakes Making Machine Process Line
Description of the Fully Automatic System
A fully automatic corn flakes making machine process line represents the pinnacle of innovation in food processing technology. This sophisticated system is designed to handle every aspect of corn flakes production, from raw material intake to the final packaging of the product. By integrating advanced automation technologies, manufacturers can achieve higher productivity, enhanced quality control, and reduced operational costs.
Major Components of the Process Line
The fully automatic corn flakes making machine process line comprises several key components, each playing a crucial role in the production process:
1. Raw Material Handling System: This component ensures the precise measurement and transfer of raw materials, such as corn grits, to the processing line. Advanced sensors and control systems maintain optimal flow rates and ingredient ratios.
2. Cooking and Gelatinization Unit: In this stage, the corn grits undergo cooking and gelatinization to form a dough-like consistency. Precise temperature and moisture control are essential to achieve the desired texture and nutritional value.
3. Forming and Flaking Section: The cooked dough is then passed through rollers to form thin sheets. These sheets are subsequently cut into flakes. Automated rollers and cutting mechanisms ensure uniform thickness and size of the flakes.
4. Toasting and Drying Equipment: The formed flakes are toasted and dried to achieve the characteristic crunchiness of corn flakes. Controlled heat application and airflow ensure even toasting and moisture removal, maintaining product quality.
5. Cooling and Packaging: After toasting, the corn flakes are cooled to prevent condensation and preserve freshness. The cooled flakes are then automatically weighed, packed, and sealed, ready for distribution.
Advanced Technology and Innovations
The modern fully automatic corn flakes making machine process line incorporates several cutting-edge technologies that enhance efficiency and product quality:
1. Automation and Control Systems: State-of-the-art PLC (Programmable Logic Controller) systems monitor and control every stage of the process, ensuring precise operation and consistency. These systems can be programmed to adjust parameters based on specific recipes and production requirements.
2. Energy Efficiency: Advanced energy-saving technologies, such as heat recovery systems and optimized power usage, reduce the overall energy consumption of the process line. This not only lowers operational costs but also contributes to sustainability efforts.
3. Hygienic Design: The equipment is designed with hygiene in mind, featuring easy-to-clean surfaces and components. This minimizes the risk of contamination and ensures compliance with food safety standards.
4. Real-time Monitoring and Data Collection: Integrated sensors and data collection systems provide real-time insights into the production process. This allows operators to monitor performance, identify potential issues, and make informed decisions to optimize production.
How the Fully Automatic Corn Flakes Making Machine Process Line Works
Step-by-Step Breakdown of the Process
The fully automatic corn flakes making machine process line is a marvel of modern food machinery, meticulously designed to transform raw materials into the finished product through a series of precise, automated steps. Each stage of the process is engineered to ensure consistency, quality, and efficiency.
Raw Material Handling and Preparation
The journey of corn flakes begins with the careful handling and preparation of raw materials. Corn grits, the primary ingredient, are received in bulk and stored in silos equipped with advanced monitoring systems. These systems ensure optimal storage conditions, maintaining the quality of the corn grits.
1. Weighing and Mixing: The first step in the process involves accurately weighing the corn grits and other ingredients. Automated weighing systems ensure the precise measurement of each component, which is then transferred to the mixing unit. Here, ingredients are blended to create a uniform mixture.
2. Conveying System: The mixed ingredients are conveyed to the next stage using a network of automated conveyors. These conveyors are designed to transport the mixture efficiently while minimizing the risk of contamination and product loss.
Cooking, Shaping, and Drying Stages
The core of the corn flakes making machine process line lies in the cooking, shaping, and drying stages, where the raw mixture is transformed into crispy, golden flakes.
3. Cooking and Gelatinization: In this stage, the corn grits mixture undergoes cooking and gelatinization in a high-temperature cooker. The mixture is cooked under precise conditions, with temperature and moisture levels meticulously controlled. This step is crucial for breaking down the starches and creating a pliable dough-like consistency.
4. Shaping and Flaking: Once cooked, the dough is passed through rollers to form thin sheets. These sheets are then cut into flakes using rotary cutters. The thickness and size of the flakes are controlled to meet specific product requirements. This stage is highly automated, ensuring uniformity in the shape and size of the corn flakes.
5. Toasting and Drying: The freshly cut flakes are transferred to the toasting and drying section. Here, the flakes are subjected to controlled heat and airflow, achieving the desired crunchiness and golden-brown color. The toasting and drying process is closely monitored to ensure even cooking and moisture removal, which is essential for product quality and shelf life.
Cooling and Packaging
After toasting, the corn flakes are cooled to prevent condensation and maintain their crisp texture. This stage is crucial to ensure the product remains fresh and crunchy until it reaches consumers.
6. Cooling System: The toasted flakes are conveyed to the cooling section, where they are gradually brought to ambient temperature. Cooling is done in a controlled environment to prevent any moisture uptake, which could compromise the product's quality.
7. Automated Packaging: Once cooled, the corn flakes are ready for packaging. The packaging unit is an integral part of the fully automatic corn flakes making machine process line. It includes automated weighing, filling, and sealing systems that ensure precise portioning and airtight packaging. The final product is then labeled and ready for distribution.
Integration and Control Systems
The entire corn flakes making machine process line is integrated with advanced control systems that monitor and manage each stage of production. These systems ensure optimal performance, quality control, and traceability.
8. PLC and SCADA Systems: Programmable Logic Controllers (PLC) and Supervisory Control and Data Acquisition (SCADA) systems are at the heart of the process line. They provide real-time data on various parameters, such as temperature, moisture, and production speed, allowing operators to make adjustments as needed to maintain product quality and efficiency.
9. Real-time Monitoring and Data Collection: The process line is equipped with sensors and data collection units that provide continuous feedback. This data is used to monitor performance, identify potential issues, and optimize production processes. The integration of IoT (Internet of Things) technology enhances the capabilities of the process line, enabling remote monitoring and control.
Innovations in the Corn Flakes Making Machine Process Line
Smart Automation and IoT Integration
The fully automatic corn flakes making machine process line is at the forefront of technological innovation, incorporating smart automation and IoT (Internet of Things) integration to enhance production efficiency, quality, and traceability. These advancements represent a significant leap forward in the field of industrial food machinery, transforming the way corn flakes are manufactured.
Advanced Automation Systems
Automation plays a crucial role in modern food processing, and the corn flakes making machine process line is no exception. The integration of advanced automation systems ensures that each stage of the production process is optimized for maximum efficiency and consistency.
1.Programmable Logic Controllers (PLCs): PLCs are the backbone of the automation system, providing precise control over various processes, such as cooking, shaping, and toasting. These controllers are programmed to handle specific tasks, ensuring that each step is performed accurately and consistently. The use of PLCs minimizes human intervention, reducing the risk of errors and enhancing overall productivity.
2.Robotic Handling: Robotics is increasingly being used in the corn flakes making machine process line to perform tasks such as material handling, packaging, and quality inspection. Robots can operate at high speeds with exceptional accuracy, significantly improving the efficiency of the production line. Their ability to work in challenging environments ensures that the highest standards of hygiene and safety are maintained.
Benefits of Smart Automation and IoT Integration
The incorporation of smart automation and IoT integration into the corn flakes making machine process line offers several benefits:
1.Increased Efficiency: Automation and IoT technologies streamline the production process, reducing cycle times and increasing throughput. This results in higher production volumes and lower operational costs.
2.Improved Quality Control: Real-time monitoring and data analysis ensure that product quality is consistently maintained. Any deviations from the desired parameters are detected and corrected immediately, preventing defects and ensuring a high-quality end product.
3.Enhanced Flexibility: The flexibility of automated systems allows manufacturers to quickly adapt to changing production requirements. Recipe changes, batch sizes, and production schedules can be adjusted with minimal downtime, providing greater agility in response to market demands.
4.Sustainability: Smart automation and IoT integration contribute to sustainability efforts by optimizing resource usage and reducing waste. Energy-efficient equipment and precise control over production processes minimize the environmental impact of manufacturing operations.
IoT Integration for Enhanced Monitoring and Control
The integration of IoT technology into the corn flakes making machine process line brings a new level of sophistication to the production process. IoT devices and sensors are embedded throughout the process line, providing real-time data on various parameters, such as temperature, humidity, and equipment performance.
1.Real-time Data Collection and Analysis: IoT sensors continuously collect data from different stages of the production process. This data is transmitted to a central monitoring system, where it is analyzed in real-time. Operators can monitor the production line remotely, making informed decisions to optimize performance and address any issues that arise promptly.
2.Predictive Maintenance: One of the significant advantages of IoT integration is the ability to perform predictive maintenance. By analyzing data from IoT sensors, the system can predict potential equipment failures before they occur. This proactive approach reduces downtime, extends the lifespan of machinery, and ensures uninterrupted production.
3.Enhanced Traceability: IoT technology enhances traceability by providing detailed information about the origin and processing of raw materials, as well as the conditions under which the corn flakes were manufactured. This level of transparency is crucial for maintaining food safety standards and meeting regulatory requirements.
Call to Action for Adopting Advanced Manufacturing Processes
As the cereal manufacturing industry continues to evolve, the adoption of advanced manufacturing processes, such as the fully automatic corn flakes making machine process line, becomes increasingly crucial. These cutting-edge technologies not only enhance efficiency and product quality but also position manufacturers at the forefront of innovation in the competitive global market.
Reference
The following are five authoritative foreign literature websites in the field of Industrial food machinery:
1. Food Engineering Magazine
Website: https://www.foodengineeringmag.com/
2.Food Processing Magazine
Website: https://www.foodprocessing.com/
3.Journal of Food Engineering
Website:https://www.journals.elsevier.com/journal-of-food-engineering
4. Food Manufacturing Magazine
Website:https://www.foodmanufacturing.com/
5. International Journal of Food Science & Technology
Website:https://onlinelibrary.wiley.com/