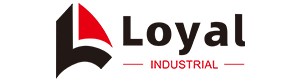
- Shandong Loyal Industrial Co.,Ltd.
- Macaroni Production Machine Instant Noodle Machine Biscuit Making Machine

Home> Company News> The Ultimate Guide to Sun Chips Production Line Extruder Machine in 2024

The Ultimate Guide to Sun Chips Production Line Extruder Machine in 2024
2024-07-09 11:51:31Introduction
In the competitive landscape of snack food production, Sun Chips have carved out a significant niche. These multi-grain chips are renowned for their unique texture and health benefits, which are largely attributed to the sophisticated production process. Central to this process is the Sun Chips Production Line Extruder Machine, a vital piece of machinery that ensures consistency, quality, and efficiency.
The extruder machine plays a crucial role in transforming raw ingredients into the familiar Sun Chips we enjoy. As we look towards 2024, several trends and innovations are shaping the future of this technology. From advancements in energy efficiency to improvements in production capacity, the extruder machine is evolving to meet the demands of both manufacturers and consumers.
Understanding the intricacies of the Sun Chips Production Line Extruder Machine is essential for anyone involved in the snack food industry. This guide aims to provide a comprehensive overview, detailing the functions, features, and future trends of this indispensable machine. By exploring these aspects, we can appreciate the technological marvels that contribute to the production of one of our favorite snacks, ensuring its continued success in the market.
Core Ingredients and Their Processing
The production of Sun Chips involves a meticulous process that begins with selecting high-quality ingredients. The core ingredients include whole corn, wheat, rice, and oats. These grains are chosen for their nutritional benefits and ability to produce the unique texture that Sun Chips are known for.
The first step in processing these ingredients is cleaning and sorting. This ensures that any impurities are removed, providing a pure base for the subsequent steps. After cleaning, the grains undergo milling, where they are ground into fine flours. This milling process is crucial for achieving the right consistency in the dough.
Next, the flours are blended according to a precise recipe. This blend forms the dough that will be used in the Sun Chips Production Line Extruder Machine. Water and a small amount of oil are added to the mix to achieve the desired dough consistency. The dough is then preconditioned, where it is subjected to heat and moisture to prepare it for extrusion.
The preconditioned dough is fed into the extruder machine, where it is subjected to high pressure and temperature. This process not only shapes the dough into the familiar chip form but also cooks it, ensuring that the final product is both safe to eat and delicious. The extruder's precise control over these conditions is essential for maintaining the quality and consistency of Sun Chips.
After extrusion, the chips are cut to size and undergo a drying process to remove any excess moisture. This step is vital for achieving the crispy texture that consumers expect. Finally, the chips are lightly seasoned before packaging.
Types of Extruder Machines Used in the Food Industry
In the realm of food production, the Sun Chips Production Line Extruder Machine stands out due to its specialized application. However, understanding the broader spectrum of extruder machines used in the food industry provides insight into the technology's versatility and importance.
Single-Screw Extruders
Single-screw extruders are the most common type of extruder machine. They consist of a single rotating screw within a stationary barrel. These machines are primarily used for straightforward extrusion processes, where the ingredients do not require complex mixing. Single-screw extruders are known for their simplicity, ease of operation, and lower cost, making them suitable for producing uniform products like pasta and snacks.
Twin-Screw Extruders
Twin-screw extruders feature two intermeshing screws that rotate within the barrel. This design allows for superior mixing, kneading, and processing of ingredients, making them ideal for more complex food products. In the context of the Sun Chips Production Line Extruder Machine, twin-screw extruders are preferred due to their ability to handle the multi-grain dough and ensure even cooking and shaping. They offer enhanced flexibility, higher efficiency, and better control over the extrusion process, resulting in a consistent and high-quality final product.
Co-Rotating vs. Counter-Rotating Twin-Screw Extruders
Twin-screw extruders can be further classified into co-rotating and counter-rotating types. Co-rotating twin-screw extruders have screws that rotate in the same direction, which is effective for intensive mixing and shearing of materials. This type is commonly used in the production of Sun Chips for its ability to create a homogeneous dough mixture. Counter-rotating twin-screw extruders, where the screws rotate in opposite directions, are less common in snack production but are used for specific applications requiring gentle handling of ingredients.
Cold Extruders
Cold extruders operate at lower temperatures and are used for products that do not require cooking during the extrusion process. These machines are ideal for applications where the ingredients' nutritional content must be preserved, such as in the production of certain health foods and pet treats. While not typically used in the production of Sun Chips, understanding cold extrusion highlights the range of capabilities within extruder technology.
High-Pressure Extruders
High-pressure extruders are designed to handle tougher materials and achieve finer textures in the final product. They are essential in applications where precise control over the texture and density is crucial. The Sun Chips Production Line Extruder Machine often utilizes high-pressure settings to achieve the desired crispiness and texture that consumers expect.
Advantages of Modern Extruder Machines in Sun Chips Production
Advantage |
Description |
Improved Product Texture and Flavor |
Modern extruder machines ensure consistent mixing and cooking, resulting in a uniform texture and enhanced flavor profile for Sun Chips. |
Increased Production Efficiency |
High-speed operation and precise control reduce downtime and maximize output, meeting high consumer demand efficiently. |
Reduced Waste |
Advanced extrusion technology minimizes ingredient waste through precise portioning and consistent production processes. |
Enhanced Food Safety and Hygiene Standards |
Incorporation of stainless steel and other hygienic materials, along with automated cleaning systems, ensures that the production environment meets stringent food safety standards. |
Energy Efficiency |
Modern extruder machines are designed to use less energy, lowering operational costs and reducing the environmental footprint of the production line. |
Versatility |
Capable of processing a wide range of ingredients, these machines can be adjusted to create different types of snacks, not just Sun Chips, enhancing production flexibility. |
Consistent Quality Control |
Real-time monitoring and advanced control systems maintain optimal processing conditions, ensuring that each batch of Sun Chips meets quality standards. |
Automation and Integration |
Integration with other production line components and use of automation reduces the need for manual intervention, improving overall workflow and productivity. |
Sustainability |
By reducing energy consumption and waste, modern extruders contribute to a more sustainable production process, aligning with industry trends towards eco-friendly manufacturing. |
Advanced Technology and Innovation |
Continuous improvements and innovations, such as AI integration for predictive maintenance, keep the Sun Chips Production Line Extruder Machine at the forefront of food processing technology. |
The Extrusion Process for Sun Chips
The extrusion process is central to the production of Sun Chips, transforming raw ingredients into the final product. The Sun Chips Production Line Extruder Machine plays a crucial role in this sophisticated and precise operation.
Step-by-Step Breakdown of the Extrusion Process
1. Mixing and Preconditioning
The process begins with the mixing of core ingredients, including whole corn, wheat, rice, and oats. These ingredients are combined with water and a small amount of oil to form a consistent dough.
Preconditioning involves subjecting the dough to controlled heat and moisture, preparing it for extrusion by enhancing its pliability and ensuring uniform cooking.
2. Feeding the Extruder
The preconditioned dough is fed into the Sun Chips Production Line Extruder Machine. The machine's design ensures a continuous and consistent feed, crucial for maintaining product quality.
3. Extrusion
Inside the extruder, the dough is subjected to high pressure and temperature. The twin-screw design of the extruder facilitates thorough mixing and even cooking.
As the dough moves through the extruder, it is pushed through a die, which shapes it into the characteristic form of Sun Chips. The precise control over temperature and pressure settings is vital to achieving the desired texture and consistency.
4. Cutting and Shaping
Once extruded, the dough is cut to the appropriate size. The cutting mechanism ensures uniformity in chip size, which is important for consistent cooking in subsequent stages.
5. Drying
The extruded and cut chips are then dried to remove excess moisture. This step is essential for achieving the crispy texture that consumers expect from Sun Chips.
The drying process is carefully controlled to ensure that the chips are neither undernor over-dried, which could affect their quality.
6. Seasoning and Packaging
After drying, the chips are lightly seasoned. The seasoning process is uniform to ensure every chip has the right flavor.
Finally, the seasoned chips are packaged, ready for distribution.
Importance of Precise Control in the Extrusion Process
Consistency: The extruder machine’s precise control over temperature, pressure, and feed rate ensures that every batch of Sun Chips meets the same high standards of quality and taste.
Efficiency: Modern extruder machines are designed to maximize production efficiency, reducing waste and energy consumption while maintaining high output levels.
Quality Control: Advanced monitoring systems in the extruder machine allow for real-time adjustments, ensuring any deviations in the process are immediately corrected to maintain product integrity.
Role of the Extruder Machine in Sun Chips Production
The Sun Chips Production Line Extruder Machine is a critical component in the manufacturing of Sun Chips, a beloved multigrain snack known for its unique texture and flavor. This sophisticated machinery plays a vital role in ensuring the efficiency and quality of the production process.
Efficient Mixing and Cooking
Central to the extruder machine is its ability to mix and cook ingredients effectively. It combines various grains like corn, wheat, and rice, ensuring a uniform blend that forms the base of Sun Chips. The machine applies precise heat and pressure to this mixture, cooking it evenly to achieve the ideal texture and taste.
Precise Shaping and Cutting
A key function of the Sun Chips Production Line Extruder Machine is shaping and cutting the dough. The extruder pushes the dough through specially designed molds, creating the distinctive wavy shape of Sun Chips. This process guarantees uniformity in size and shape, enhancing the product's visual appeal and ensuring consistency.
Enhancing Product Quality and Consistency
Maintaining high quality and consistency is paramount in Sun Chips production. The extruder machine is equipped with advanced controls to monitor and adjust temperature, pressure, and moisture levels throughout the process. These adjustments are crucial for producing chips with the perfect texture and flavor every time.
Maximizing Production Efficiency
Beyond quality, the extruder machine significantly improves production efficiency. Its continuous processing capabilities allow for high throughput, minimizing downtime and boosting overall productivity. This efficiency is essential for meeting market demand and ensuring timely delivery of Sun Chips.
Future Trends in Sun Chips Production Line Extruder Machines
As the food industry evolves, the Sun Chips Production Line Extruder Machine is set to undergo significant advancements to meet growing consumer demands and sustainability goals. Here are the key future trends anticipated in 2024:
Technological Advancements
Artificial Intelligence and Machine Learning
The integration of artificial intelligence (AI) and machine learning (ML) is transforming the operation of extruder machines. AI and ML algorithms can analyze vast amounts of production data to optimize the extrusion process in real-time. This leads to more precise control over temperature, pressure, and moisture levels, resulting in consistently high-quality Sun Chips.
IoT and Smart Sensors
The adoption of the Internet of Things (IoT) and smart sensors allows for continuous monitoring and remote management of the extrusion process. These technologies enhance predictive maintenance, reducing downtime and increasing overall efficiency. Smart sensors provide real-time feedback, enabling instant adjustments to ensure optimal production conditions.
Energy Efficiency and Sustainability
Eco-Friendly Design
Future extruder machines will focus on energy efficiency and reduced environmental impact. Innovations such as improved insulation, energy recovery systems, and eco-friendly materials will make the Sun Chips Production Line Extruder Machine more sustainable. These advancements will help manufacturers reduce their carbon footprint and operational costs.
Sustainable Materials
There is a growing trend towards using biodegradable and recyclable materials in the construction of extruder machines. This not only enhances the sustainability of the production process but also aligns with consumer preferences for environmentally responsible products.
Enhanced Automation and Integration
Advanced Automation
Automation is set to become even more sophisticated, with advanced robotic systems handling various aspects of the production line. This includes automated ingredient mixing, precise dough feeding, and seamless integration with packaging systems. Enhanced automation reduces the need for manual intervention, increasing production speed and consistency.
Seamless Integration
Future extruder machines will feature seamless integration with other components of the production line, such as mixing tanks, preconditioners, and packaging units. This holistic approach ensures a streamlined production process, minimizing bottlenecks and enhancing overall productivity.
Customization and Flexibility
Modular Design
The trend towards modular design will allow manufacturers to customize their extruder machines to meet specific production needs. Modular components can be easily added or removed, providing flexibility in product development and scaling production volumes.
Versatility in Production
Future extruder machines will be designed to handle a wider range of ingredients and recipes. This versatility will enable manufacturers to produce various snack types, including new flavors and healthier options, catering to diverse consumer preferences.
References
The following are five authoritative foreign literature websites on industrial Sun Chips production:
1.ScienceDirect
Website: [https://www.sciencedirect.com/]
2.IEEE Xplore
Website: [https://ieeexplore.ieee.org/Xplore/home.jsp]
3.SpringerLink
Website: [https://link.springer.com/]
4.Potato Business
Website: [https://www.potatobusiness.com]
5.ResearchGate
Website: [https://www.researchgate.net/]