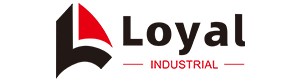
- Shandong Loyal Industrial Co.,Ltd.
- Macaroni Production Machine Instant Noodle Machine Biscuit Making Machine

Home> Company News> The Ultimate Guide to Baby Food Powder Machinery in 2024

The Ultimate Guide to Baby Food Powder Machinery in 2024
2024-07-12 10:43:12Introduction
Baby Food Powder Machinery has revolutionized the baby food industry by ensuring the production of high-quality, nutritious baby food powders. These machines are designed to meet stringent hygiene standards and deliver precise control over the manufacturing process, ensuring consistency and safety in every batch.
The advancements in baby food powder machinery technology have made it possible to achieve superior product quality while maintaining efficiency and reducing production costs. In 2024, these machines are more sophisticated than ever, featuring state-of-the-art automation, real-time monitoring, and advanced filtration systems.
Key components of modern baby food powder machinery include mixing tanks, spray dryers, sieving equipment, and packaging machines. Each of these components plays a crucial role in the production process, from mixing raw ingredients to drying and packaging the final product.
As an expert in industrial food machinery, it's essential to understand the latest trends and innovations in baby food powder machinery to stay competitive in the market. This guide will provide a comprehensive overview of the current state of the industry, highlighting key technologies, regulatory considerations, and best practices for optimizing production.
Key Components of Baby Food Powder Machinery
Understanding the key components of Baby Food Powder Machinery is crucial for optimizing production and ensuring product quality. These components work together to create a seamless manufacturing process that adheres to industry standards and meets consumer expectations.
1. Mixing Tanks
Mixing tanks are essential in the initial phase of baby food powder production. These tanks are designed to mix raw ingredients thoroughly, ensuring a consistent blend. Advanced mixing tanks feature precise temperature control and automated stirring mechanisms, which are vital for maintaining the quality and safety of the baby food powder.
2. Spray Dryers
Spray dryers play a critical role in transforming liquid mixtures into powdered form. This process involves spraying the liquid mixture into a chamber where it is rapidly dried using hot air. Modern spray dryers in baby food powder machinery are equipped with sophisticated controls that allow for the adjustment of temperature, airflow, and drying time, ensuring the optimal moisture content and particle size of the final product.
3. Sieving Equipment
After drying, the powder must be sieved to remove any oversized particles and ensure uniformity. Sieving equipment in baby food powder machinery uses fine meshes and vibrating screens to achieve this. High-quality sieving equipment enhances product consistency and quality, which are crucial for consumer satisfaction.
4. Packaging Machines
Packaging is the final step in the production process, and it requires precision and care. Packaging machines in baby food powder machinery are designed to fill and seal containers efficiently while maintaining hygiene standards. Advanced packaging systems offer features such as nitrogen flushing to preserve freshness, automated labeling, and tamper-evident seals, ensuring that the baby food powder reaches consumers in perfect condition.
Key Features and Specifications
Feature |
Description |
Automation |
Modern Baby Food Powder Machinery is highly automated, featuring PLC (Programmable Logic Controller) systems for precise control and efficiency. |
Capacity |
These machines come with varying capacities, typically ranging from 500 kg/h to 2000 kg/h, to meet different production needs. |
Material Construction |
Constructed with high-grade stainless steel to ensure durability, hygiene, and resistance to corrosion. |
Mixing Technology |
Advanced mixing technology ensures a homogeneous blend of ingredients, crucial for the consistency of baby food powder. |
Drying Process |
Utilizes state-of-the-art spray drying techniques to convert liquid mixtures into fine powder while preserving nutritional value. |
Energy Efficiency |
Designed with energy-efficient components to minimize power consumption and reduce operational costs. |
Hygienic Design |
Features easy-to-clean surfaces and CIP (Clean-in-Place) systems to maintain high hygiene standards and reduce contamination risks. |
Real-Time Monitoring |
Equipped with sensors and real-time monitoring systems to track critical parameters like temperature, humidity, and flow rates. |
Safety Features |
Includes safety interlocks, emergency stop buttons, and fail-safe mechanisms to ensure operator and product safety. |
Customization Options |
Offers customizable configurations to cater to specific production requirements and product specifications. |
Regulatory Compliance |
Meets international food safety standards and regulations, ensuring compliance with agencies like FDA, EU, and others. |
Maintenance |
Designed for easy maintenance with accessible parts and comprehensive manuals, ensuring minimal downtime and longevity of the machinery. |
Packaging Integration |
Integrated with advanced packaging systems that offer features such as vacuum sealing, nitrogen flushing, and tamper-evident sealing. |
Technological Innovations in Baby Food Powder Machinery
In 2024, Baby Food Powder Machinery has seen several technological innovations that enhance efficiency, safety, and product quality. These advancements are critical for manufacturers aiming to stay competitive in the evolving food industry.
1. Advanced Automation: Modern baby food powder machinery incorporates advanced automation technologies such as PLCs (Programmable Logic Controllers) and SCADA (Supervisory Control and Data Acquisition) systems. These technologies provide precise control over the production process, minimize human error, and enhance operational efficiency.
2. AI and Machine Learning: The integration of AI and machine learning in baby food powder machinery allows for predictive maintenance and process optimization. These technologies can analyze data in real-time, predict potential equipment failures, and suggest adjustments to improve product quality and reduce downtime.
3. Enhanced Spray Drying Technology: Innovations in spray drying technology have led to the development of more efficient dryers that use less energy and produce finer, more uniform powders. These advancements ensure that the nutritional content and flavor of the ingredients are preserved, meeting the high standards required for baby food products.
4. Improved Mixing Systems: New mixing systems provide better homogenization of ingredients, ensuring consistent quality in every batch of baby food powder. These systems are equipped with sensors that monitor the mixing process and adjust parameters automatically to maintain optimal conditions.
5. Real-Time Monitoring and Control: State-of-the-art baby food powder machinery features real-time monitoring and control systems that track critical parameters such as temperature, humidity, and particle size. These systems ensure that the production process remains within specified limits, guaranteeing the safety and quality of the final product.
6. Energy Efficiency: The latest baby food powder machinery is designed with energy-efficient components and processes, reducing the overall energy consumption and operational costs. This is achieved through innovations like heat recovery systems and low-energy drying techniques.
7. Hygienic Design: Enhanced hygienic design features, including CIP (Clean-in-Place) systems and easy-to-clean surfaces, minimize contamination risks and ensure compliance with strict hygiene standards. These features are crucial for producing safe baby food products.
8. Sustainability: Advances in sustainable manufacturing practices have been incorporated into modern baby food powder machinery. This includes the use of eco-friendly materials, waste reduction technologies, and systems that lower water and energy consumption.
Choosing the Right Baby Food Powder Machinery
Selecting the appropriate Baby Food Powder Machinery is critical for ensuring efficient production and high-quality output. Here are the key factors to consider:
1. Production Capacity: Evaluate the production capacity of the machinery to match your operational needs. Consider machines that can handle your required volume, whether it's small-scale production or large-scale industrial output.
2. Automation Level: Modern baby food powder machinery offers various levels of automation. Choose equipment with advanced automation features such as PLCs and real-time monitoring systems to enhance efficiency and reduce manual intervention.
3. Hygiene Standards: Ensure the machinery complies with strict hygiene standards. Look for features like CIP (Clean-in-Place) systems, stainless steel construction, and easy-to-clean surfaces to minimize contamination risks.
4. Energy Efficiency: Opt for machines designed with energy-efficient components to reduce operational costs. Consider equipment with low-energy drying techniques and heat recovery systems to conserve energy.
5. Mixing and Drying Technology: The quality of the final product depends heavily on the mixing and drying technology used. Choose machinery with advanced mixing systems for uniform blending and spray dryers that preserve nutritional value.
6. Customization Options: Depending on your specific requirements, you may need machinery with customizable configurations. Select equipment that can be tailored to meet your unique production needs and specifications.
7. Safety Features: Prioritize machinery with comprehensive safety features, including emergency stop buttons, safety interlocks, and fail-safe mechanisms to protect operators and maintain product safety.
8. Regulatory Compliance: Ensure the machinery meets international food safety standards and regulations, such as those set by the FDA and EU. Compliance with these standards is crucial for the legal and safe production of baby food powders.
9. Maintenance and Support: Choose machinery that offers easy maintenance and comes with robust technical support. Look for manufacturers who provide comprehensive maintenance manuals and quick access to spare parts.
10. Cost: While cost is an important factor, it should not compromise quality and features. Balance the initial investment with the long-term benefits of reliability, efficiency, and lower operational costs.
Maintenance and Troubleshooting Tips
Maintaining Baby Food Powder Machinery is crucial for ensuring continuous operation and high product quality. Here are essential maintenance and troubleshooting tips to keep your equipment running smoothly:
1. Regular Cleaning and Inspection:
Cleaning: Regularly clean all parts of the machinery, including mixing tanks, spray dryers, and conveying systems, to prevent buildup of residue and contaminants.
Inspection: Conduct routine inspections of critical components such as seals, filters, and belts to identify wear and tear early.
2. Lubrication:
Use of Proper Lubricants: Ensure all moving parts are adequately lubricated according to manufacturer recommendations. Use food-grade lubricants to maintain hygiene standards.
3. Calibration of Sensors and Controls:
Sensor Calibration: Regularly calibrate sensors and monitoring systems to ensure accurate readings of temperature, humidity, and other critical parameters.
Control Systems: Verify the accuracy of PLCs and SCADA systems to maintain precise control over the production process.
4. Scheduled Maintenance:
Follow Manufacturer Guidelines: Adhere to the manufacturer's recommended maintenance schedule for specific components and systems.
Predictive Maintenance: Implement predictive maintenance practices using data analytics to anticipate and prevent potential equipment failures.
5. Troubleshooting:
Identify Common Issues: Familiarize yourself with common issues such as clogging in spray nozzles, motor malfunctions, and airflow disruptions.
Quick Response: Develop a troubleshooting checklist and train operators to respond promptly to equipment alarms and abnormalities.
6. Emergency Preparedness:
Emergency Procedures: Establish clear emergency procedures, including shutdown protocols and emergency contact information, to minimize downtime during critical failures.
Spare Parts Inventory: Maintain an inventory of essential spare parts and components to facilitate quick repairs and replacements.
7. Training and Documentation:
Operator Training: Provide comprehensive training for operators on equipment operation, maintenance procedures, and safety protocols.
Documentation: Keep detailed records of maintenance activities, repairs, and equipment modifications for reference and audit purposes.
Future Trends in Baby Food Powder Machinery
As we look forward to 2024 and beyond, several emerging trends are shaping the landscape of Baby Food Powder Machinery. These advancements are poised to revolutionize the industry with improved efficiency, sustainability, and product innovation.
1. Integration of IoT and Industry 4.0:
IoT (Internet of Things): Baby food powder machinery is increasingly adopting IoT technology to enable real-time monitoring of equipment performance and predictive maintenance. Sensors embedded in machinery collect data on operational parameters, facilitating proactive troubleshooting and optimizing production processes.
Industry 4.0: The convergence of digital technologies under Industry 4.0 principles enhances automation and connectivity across the manufacturing ecosystem. This includes seamless integration of production systems, data analytics for decision-making, and enhanced supply chain management.
2. Advancements in Sustainability:
Green Technologies: Manufacturers are focusing on developing eco-friendly baby food powder machinery that minimizes environmental impact. This includes energy-efficient designs, use of sustainable materials, and waste reduction strategies throughout the production cycle.
Circular Economy: Embracing principles of the circular economy, future machinery designs aim to maximize resource efficiency by optimizing material use, promoting recycling, and reducing waste generation.
3. Precision and Customization:
Precision Engineering: Future machinery will feature enhanced precision in mixing, drying, and packaging processes. This ensures consistent product quality and allows for customization of formulations to meet diverse consumer preferences and nutritional requirements.
Flexible Production Lines: Modular and adaptable production lines will enable manufacturers to swiftly adjust production volumes and product variations in response to market demands and regulatory changes.
4. Enhanced Hygiene and Safety Standards:
Hygienic Design: Machinery designs will continue to prioritize hygienic standards with improved cleaning-in-place (CIP) systems, sanitary construction materials, and automated sanitation protocols. These measures ensure compliance with stringent food safety regulations and maintain product integrity.
5. Innovative Packaging Solutions:
Smart Packaging: Integration of smart packaging technologies such as RFID tags and QR codes will enhance traceability, shelf-life monitoring, and consumer engagement. Packaging machinery will evolve to accommodate these features while maintaining product freshness and safety.
Sustainable Packaging: Emphasis on sustainable packaging solutions, including biodegradable materials and minimalistic designs, will align with consumer preferences for environmentally conscious products.
6. Global Regulatory Compliance:
Adherence to Standards: Manufacturers will continue to prioritize compliance with global food safety regulations, including FDA, EU, and other regional standards. Future machinery designs will incorporate features that facilitate documentation, auditing, and regulatory reporting.
References
The following are five authoritative foreign literature websites on industrial Nutritional Powder production:
1.PubMed
Website: [https://pubmed.ncbi.nlm.nih.gov/]
2.IEEE Xplore
Website: [https://ieeexplore.ieee.org/Xplore/home.jsp]
3.SpringerLink
Website: [https://link.springer.com/]
4.ScienceDirect
Website: [https://www.sciencedirect.com/]
5.ResearchGate
Website: [https://www.researchgate.net/]