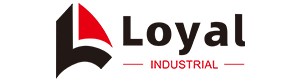
- Shandong Loyal Industrial Co.,Ltd.
- Macaroni Production Machine Instant Noodle Machine Biscuit Making Machine

Home> Company News> Everything You Need To Know About baby food/nutrition powder processing line

Everything You Need To Know About baby food/nutrition powder processing line
2024-07-13 14:17:02Introduction to Fully Automatic Baby Food/Nutrition Powder Processing Line
The baby food/nutrition powder industry has undergone significant transformations over the past few decades. With increasing demand for high-quality, safe, and nutritious products, manufacturers are constantly seeking ways to enhance their production processes. One of the most notable advancements in this sector is the implementation of fully automatic systems in baby food/nutrition powder processing lines. These systems are designed to optimize efficiency, reduce energy consumption, and ensure the highest standards of product quality.
The importance of efficiency in production processes cannot be overstated. In a highly competitive market, manufacturers need to produce large volumes of baby food and nutrition powder quickly and cost-effectively. Fully automatic systems are equipped with advanced technologies that streamline various stages of production, from mixing and blending to packaging and distribution. By minimizing human intervention, these systems not only accelerate production but also significantly reduce the risk of contamination and human error.
Fully automatic baby food/nutrition powder processing lines are engineered to handle complex formulations with precision. These systems incorporate state-of-the-art machinery that ensures consistent mixing and blending of ingredients, accurate dosing, and precise packaging. As a result, manufacturers can maintain the nutritional integrity of their products while meeting stringent safety standards. Moreover, the integration of automated cleaning and maintenance processes further enhances operational efficiency, allowing for uninterrupted production cycles.
In summary, the introduction of fully automatic systems in the baby food/nutrition powder processing line marks a revolutionary step forward for the industry. These systems not only improve production efficiency and product quality but also contribute to energy savings and sustainability. As the demand for high-quality baby food and nutrition powder continues to rise, the adoption of advanced, fully automatic processing lines will play a crucial role in meeting market needs and setting new industry standards.
Precision dosing and ingredient handling systems
Precision Dosing and Ingredient Handling Systems |
Precision dosing and ingredient handling are critical components of a fully automatic baby food/nutrition powder processing line. Ensuring that each product batch meets stringent nutritional and safety standards requires advanced technology and meticulous control over every step of the process. Fully automatic systems are designed to deliver unparalleled accuracy and consistency in these areas, contributing significantly to high efficiency and product quality. |
Advanced Dosing Technologies |
In the realm of baby food and nutrition powder production, precise dosing is essential. Fully automatic processing lines utilize sophisticated dosing technologies that ensure exact measurements of ingredients. These systems often incorporate electronic scales, volumetric dispensers, and flow meters, all of which are calibrated to provide precise quantities of raw materials. By eliminating manual measurement errors, these systems guarantee that each batch of product adheres to the specified nutritional composition, thus maintaining the brand’s commitment to quality and safety. |
Automated Ingredient Handling |
Ingredient handling is another crucial aspect of the production process. Fully automatic systems are equipped with advanced handling mechanisms that manage the movement, storage, and delivery of raw materials. These systems include automated conveyors, hoppers, and feeders that transport ingredients from storage to mixing and blending stations. This automation not only speeds up the production process but also minimizes the risk of contamination, as human contact with raw materials is significantly reduced. |
Consistency and Quality Control |
Consistency is a hallmark of high-quality baby food and nutrition powder products. Fully automatic baby food/nutrition powder processing lines are equipped with real-time monitoring and control systems that oversee every stage of production. These systems ensure that all ingredients are handled and dosed accurately, maintaining uniformity across all batches. Advanced sensors and feedback mechanisms detect any deviations from the set parameters and make immediate adjustments, ensuring that the final product meets the highest quality standards. |
Efficiency and Cost Savings |
The integration of precision dosing and automated ingredient handling systems in baby food/nutrition powder processing lines leads to significant efficiency gains and cost savings. By optimizing the use of raw materials and reducing waste, manufacturers can lower production costs. Additionally, the speed and accuracy of automated systems allow for higher production volumes, meeting market demands without compromising on quality. |
Enhanced Product Quality and Safety Measures
In the competitive market of baby food and nutrition powder, product quality and safety are paramount. A fully automatic baby food/nutrition powder processing line is designed to enhance these aspects significantly, ensuring that every product that reaches the consumer meets the highest standards. The integration of advanced technologies and stringent control measures plays a crucial role in achieving this objective.
Advanced Quality Control Systems |
A key feature of fully automatic baby food/nutrition powder processing lines is the incorporation of advanced quality control systems. These systems utilize cutting-edge technology to monitor every stage of production. High-precision sensors and automated inspection tools continuously check for consistency in texture, weight, and composition. Any deviations from the specified parameters are detected in real time, allowing for immediate corrective actions. This ensures that each batch of baby food and nutrition powder maintains uniform quality, providing consumers with reliable and safe products. |
Hygienic Design and Contamination Prevention |
Hygiene is critical in baby food production, where contamination can have severe consequences. Fully automatic processing lines are designed with hygiene as a top priority. The machinery is constructed from high-grade stainless steel and other materials that are resistant to corrosion and easy to clean. Automated cleaning systems, such as Clean-in-Place (CIP), are integrated into the production line to ensure thorough cleaning without the need for disassembly. These measures prevent cross-contamination and maintain a sterile production environment, safeguarding the purity and safety of the baby food/nutrition powder. |
Traceability and Compliance |
Traceability is another vital aspect of quality and safety in the baby food industry. Fully automatic baby food/nutrition powder processing lines are equipped with sophisticated traceability systems that track every ingredient and process step. This comprehensive tracking capability ensures that any issues can be quickly identified and addressed, reducing the risk of widespread product recalls. Moreover, these systems help manufacturers comply with stringent regulatory requirements, ensuring that all products meet international safety standards. |
Automated Packaging Solutions |
Packaging plays a crucial role in preserving the quality and safety of baby food and nutrition powder. Fully automatic processing lines include advanced packaging solutions that seal products in a controlled environment, protecting them from contamination and spoilage. Automated packaging machines precisely measure and fill containers, ensuring consistent product amounts and reducing human error. Additionally, tamper-evident seals and other security features enhance product safety, giving consumers confidence in the integrity of the products they purchase. |
Real-Time Data and Analytics |
The integration of real-time data and analytics in fully automatic baby food/nutrition powder processing lines further enhances product quality and safety. These systems collect and analyze data from various stages of the production process, providing valuable insights into operational performance and product quality. Manufacturers can use this data to optimize production parameters, identify potential issues before they become problems, and continuously improve their processes. This proactive approach to quality control helps maintain high standards and ensures that products consistently meet consumer expectations. |
In conclusion, enhanced product quality and safety measures are fundamental to the success of a fully automatic baby food/nutrition powder processing line. Through advanced quality control systems, hygienic design, traceability, automated packaging, and real-time data analytics, manufacturers can produce high-quality, safe baby food products. As the demand for nutritious and safe baby food continues to rise, the adoption of these advanced automated systems will be essential for meeting consumer expectations and maintaining a competitive edge in the market.
Innovations Driving Efficiency in Fully Automatic Baby Food/Nutrition Powder Processing Line
In the dynamic landscape of food machinery, innovations play a pivotal role in driving efficiency and productivity. The baby food/nutrition powder processing line has seen significant advancements, thanks to the integration of fully automatic systems. These innovations not only enhance production speed and output but also ensure the highest standards of quality and safety.
1. Automated Mixing and Blending
One of the critical innovations in fully automatic baby food/nutrition powder processing lines is automated mixing and blending systems. These systems use precise control algorithms to ensure consistent mixing of ingredients, which is crucial for maintaining the nutritional value and texture of the final product. By automating this process, manufacturers can achieve uniformity in every batch, reducing the risk of human error and increasing overall efficiency.
2. Advanced Drying Technologies
Efficient drying is essential in the production of baby food and nutrition powder. Innovative drying technologies, such as microwave and vacuum drying, have been integrated into fully automatic processing lines. These technologies offer faster drying times and better energy efficiency compared to traditional methods. By reducing moisture content quickly and uniformly, they help preserve the nutritional quality of the products while minimizing energy consumption.
3. Intelligent Control Systems
Intelligent control systems are at the heart of modern fully automatic baby food/nutrition powder processing lines. These systems use sensors, data analytics, and machine learning algorithms to monitor and control every aspect of the production process. They can adjust parameters in real-time to optimize performance, ensuring that the machinery operates at peak efficiency. This not only improves productivity but also reduces waste and energy consumption.
4. Robotic Packaging Solutions
Packaging is a critical step in the production of baby food and nutrition powder. Robotic packaging solutions have revolutionized this process by providing high-speed, accurate, and flexible packaging options. These systems can handle different packaging formats and sizes with ease, ensuring that products are sealed and labeled correctly. By automating the packaging process, manufacturers can reduce labor costs and increase throughput.
5. Integration of IoT and Big Data
The integration of the Internet of Things (IoT) and big data analytics has transformed the way fully automatic baby food/nutrition powder processing lines operate. IoT devices collect data from various parts of the production line, providing insights into machine performance, product quality, and operational efficiency. Big data analytics can then be used to identify patterns and trends, allowing manufacturers to make data-driven decisions to enhance efficiency and reduce downtime.
6. Energy-Efficient Equipment Design
Energy efficiency is a crucial consideration in the design of modern food processing machinery. Innovations in equipment design, such as the use of energy-efficient motors and optimized process flows, have significantly reduced the energy consumption of fully automatic baby food/nutrition powder processing lines. These advancements help manufacturers meet sustainability goals and reduce operational costs.
7. Enhanced Cleaning and Maintenance Systems
Maintaining cleanliness and hygiene is paramount in baby food production. Fully automatic processing lines now incorporate enhanced cleaning and maintenance systems, such as Clean-in-Place (CIP) technology. These systems automate the cleaning process, ensuring that all parts of the machinery are thoroughly cleaned without the need for disassembly. This reduces downtime and labor costs while maintaining high standards of hygiene.
Outlook for the Industry's Technological Evolution
The future of the baby food/nutrition powder processing line industry is set to be marked by rapid technological evolution. As consumer demand for high-quality, safe, and nutritious products continues to rise, manufacturers are increasingly investing in advanced technologies to meet these expectations. The integration of fully automatic systems is at the forefront of this transformation, promising unprecedented levels of efficiency, quality, and sustainability.
1. Greater Integration of Artificial Intelligence (AI) and Machine Learning (ML)**
The application of AI and ML in the baby food/nutrition powder processing line is expected to deepen, driving further automation and precision in production processes. These technologies will enable real-time monitoring and predictive maintenance, reducing downtime and ensuring consistent product quality. AI-driven analytics will also provide insights into consumer preferences and production trends, allowing manufacturers to optimize their operations and product offerings.
2. Enhanced Connectivity through the Industrial Internet of Things (IIoT)
The IIoT will play a crucial role in the technological evolution of the baby food/nutrition powder processing line. By connecting various components of the production line, IIoT-enabled systems will facilitate seamless communication and data exchange. This connectivity will lead to more efficient supply chain management, better resource allocation, and improved traceability of ingredients and finished products. Enhanced connectivity will also enable remote monitoring and control, providing manufacturers with greater flexibility and responsiveness.
Reference
The following are five authoritative foreign literature websites in the field of Industrial food machinery:
1. Food Engineering Magazine
Website: https://www.foodengineeringmag.com/
2.Food Processing Magazine
Website: https://www.foodprocessing.com/
3.Journal of Food Engineering
Website:https://www.journals.elsevier.com/journal-of-food-engineering
4. Food Manufacturing Magazine
Website:https://www.foodmanufacturing.com/
5. International Journal of Food Science & Technology
Website:https://onlinelibrary.wiley.com/