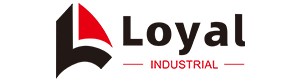
- Shandong Loyal Industrial Co.,Ltd.
- Macaroni Production Machine Instant Noodle Machine Biscuit Making Machine

Home> Company News> Everything You Need To Know About Cereals Powder Making Machines in 2024

Everything You Need To Know About Cereals Powder Making Machines in 2024
2024-07-15 10:04:55Introduction
Cereals powder making machines are essential equipment in the food processing industry, designed to transform raw cereals into fine, consumable powders. These machines play a crucial role in producing a variety of cereal-based products, catering to the growing demand for convenient and nutritious food options. Understanding the functionalities and applications of cereals powder making machines is vital for manufacturers aiming to optimize their production processes and meet market needs.
The importance of cereals powder in the food industry cannot be overstated. Cereals powder is a key ingredient in many food products, including breakfast cereals, baby food, and dietary supplements. Its versatility and ease of use make it a staple in both household and commercial kitchens. With advancements in food technology, cereals powder making machines have evolved to offer higher efficiency, better quality, and enhanced safety features, making them indispensable for modern food production facilities.
In this comprehensive guide, we will explore the various types of cereals powder making machines, their key components, and the production process. We will also delve into technological advancements, maintenance tips, and regulatory compliance to provide a thorough understanding of these machines' capabilities and benefits. Whether you are a seasoned industry professional or new to the field, this guide will equip you with the knowledge needed to make informed decisions about cereals powder making machines.
Types of Cereals Powder Making Machines
Cereals powder making machines are essential in the food processing industry, providing efficient methods to transform whole grains into fine powders. These machines come in various types, each suited for specific production needs. Understanding the different types of cereals powder making machines can help businesses choose the right equipment for their operations.
Dry Milling Machines
Dry milling machines are designed to process cereals without the use of water or other liquids. These machines grind the grains into fine powder through mechanical processes, making them ideal for producing dry cereals powder. Dry milling is typically used for products that require a longer shelf life and less moisture content.
Wet Milling Machines
Wet milling machines use water or other liquids to aid in the grinding process. This method is particularly effective for cereals that require a finer texture and higher moisture content. Wet milling helps in breaking down the cereals more efficiently, resulting in a smoother powder. These machines are commonly used in the production of baby foods and other specialized cereals products.
Multi-functional Machines
Multi-functional cereals powder making machines combine the capabilities of both dry and wet milling. These versatile machines can switch between processes based on the specific requirements of the product being manufactured. Multi-functional machines are ideal for businesses that need to produce a variety of cereals powders, offering flexibility and efficiency.
Choosing the right type of cereals powder making machine is crucial for optimizing production and meeting specific product requirements. Whether opting for dry milling, wet milling, or multi-functional machines, understanding their unique features and benefits will help ensure a successful cereals powder production process.
Key Components and Features
Cereals powder making machines are sophisticated pieces of equipment designed to efficiently convert whole grains into fine powder. Understanding the key components and features of these machines can help in selecting the right model for specific needs.
Component |
Description |
Grinders and Mills |
These are the primary components responsible for breaking down cereals into powder. High-quality grinders ensure consistent and fine grinding. |
Sieves and Filters |
Sieves and filters are used to separate and grade the powdered cereals based on particle size, ensuring uniformity and quality. |
Mixing and Blending Units |
These units ensure that the powdered cereals are evenly mixed, especially important when combining different types of grains or adding nutrients. |
Control Panels and Automation Features |
Modern cereals powder making machines come with advanced control panels and automation features, allowing precise control over the production process and improving efficiency. |
Understanding these components and their features is crucial for optimizing the performance of cereals powder making machines and ensuring high-quality output.
Production Process Overview
Cleaning and Pre-treatment of Cereals
The initial step in using cereals powder making machines involves the cleaning and pre-treatment of cereals. This phase is critical to ensure the removal of impurities such as stones, dirt, and husks. Advanced cleaning equipment, including air classifiers and magnetic separators, are employed to achieve a high degree of purity, ensuring that the cereals entering the grinding phase are free from contaminants.
Grinding and Milling
Following the cleaning process, the cereals are directed to grinding and milling machines. These cereals powder making machines are designed to crush and grind cereals into fine powder. Utilizing various grinding techniques, such as hammer milling or roller milling, the cereals are reduced to the desired particle size. The efficiency and precision of these machines are vital for producing consistent and high-quality cereals powder.
Sieving and Grading
Once grinding is complete, the cereals powder is subjected to sieving and grading. This step ensures uniform particle size distribution, which is crucial for the final product quality. Sieving machines equipped with multiple layers of screens are used to separate fine powder from larger particles. Grading further categorizes the powder based on specific size requirements, ensuring consistency in the final product.
Mixing and Blending
The next phase involves mixing and blending the sieved cereals powder. This step is essential for achieving homogeneity in the product, especially when different types of cereals or additional ingredients are included. High-precision mixing machines ensure that the powder is thoroughly blended, resulting in a uniform and consistent mixture that meets quality standards.
Packaging and Storage
The final step in the cereals powder making process is packaging and storage. Automated packaging machines are used to pack the cereals powder into various formats, such as bags or containers, ensuring that the product is protected from moisture and contaminants. Proper storage conditions are maintained to preserve the quality and shelf life of the cereals powder. Effective packaging and storage practices are essential for maintaining product integrity and safety until it reaches the consumer.
Technological Advancements in Cereals Powder Making Machines
In recent years, the cereals powder making machines industry has seen significant technological advancements. These improvements are primarily aimed at enhancing efficiency, ensuring product quality, and reducing operational costs. Let's explore the key technological advancements in this field.
Automation and Control Systems
Modern cereals powder making machines are equipped with advanced automation and control systems. These systems allow for precise monitoring and control of the production process. Parameters such as temperature, pressure, and humidity can be accurately controlled, ensuring consistent product quality. Additionally, automation reduces the need for manual intervention, minimizing human error and increasing production efficiency.
Energy Efficiency
Energy consumption is a major concern in industrial food processing. Recent technological advancements have led to the development of energy-efficient cereals powder making machines. These machines utilize innovative heating and cooling systems that reduce energy usage without compromising on performance. Energy-efficient designs not only lower operational costs but also contribute to environmental sustainability.
High-Speed Production
To meet the growing demand for cereals powder, manufacturers have developed high-speed production machines. These machines can process large quantities of raw materials quickly, increasing overall production capacity. High-speed production capabilities are essential for maintaining competitiveness in the food processing industry.
Improved Grinding and Milling Techniques
The core function of cereals powder making machines is to grind and mill raw materials into fine powder. Technological advancements have led to the development of improved grinding and milling techniques. These techniques ensure uniform particle size distribution, enhancing the texture and consistency of the final product. Advanced grinding systems also reduce wastage and improve yield.
Integration of IoT and Data Analytics
The integration of the Internet of Things (IoT) and data analytics in cereals powder making machines has revolutionized the industry. IoT-enabled machines can collect real-time data on various production parameters. This data can be analyzed to optimize the production process, identify potential issues, and implement predictive maintenance. Data-driven insights help manufacturers improve efficiency and reduce downtime.
Enhanced Hygiene and Safety Features
Food safety and hygiene are paramount in the production of cereals powder. Modern cereals powder making machines are designed with enhanced hygiene and safety features. Stainless steel construction, easy-to-clean surfaces, and automated cleaning systems ensure compliance with strict hygiene standards. These features minimize the risk of contamination and ensure the production of safe and high-quality cereals powder.
Maintenance and Troubleshooting Tips
When operating cereals powder making machines, proper maintenance is crucial to ensure optimal performance and longevity. Here are essential maintenance and troubleshooting tips to keep your equipment running smoothly:
1. Regular Cleaning Schedule: Establish a routine cleaning schedule to prevent residue buildup, which can affect machine efficiency. Use recommended cleaning agents and methods suitable for food-grade equipment.
2. Inspect Wear Parts: Regularly inspect wear parts such as blades, screens, and conveyor belts for signs of wear and tear. Replace worn parts promptly to avoid production disruptions and ensure consistent product quality.
3. Lubrication: Ensure all moving parts are properly lubricated according to manufacturer guidelines. Over or under-lubrication can lead to equipment malfunction. Use food-grade lubricants suitable for the operating conditions.
4. Monitor Electrical Components: Check electrical components, including wiring and connectors, for signs of damage or corrosion. Ensure all connections are secure and insulated to prevent electrical hazards.
5. Calibration and Adjustment: Periodically calibrate the machine to maintain accurate processing parameters. Adjust settings such as speed, temperature, and pressure as needed to optimize performance for different cereal types and production volumes.
6. Troubleshooting Common Issues: Be prepared to troubleshoot common issues such as uneven powder consistency, clogging, or motor overheating. Refer to the manufacturer's troubleshooting guide for specific solutions and follow safety protocols during maintenance and repairs.
7. Training and Documentation: Provide training for operators on proper machine operation, maintenance procedures, and safety protocols. Keep comprehensive documentation of maintenance records, repairs, and spare parts inventory for reference.
Implementing these maintenance and troubleshooting tips will help maximize the efficiency, reliability, and safety of your cereals powder making machines, ensuring consistent production of high-quality cereal powders.
Regulatory Compliance and Safety Standards
When considering cereals powder making machines, regulatory compliance and safety standards are paramount in ensuring both product quality and operational safety. These machines, designed for efficiently processing various cereal grains into powdered form, must adhere to stringent guidelines to meet industry standards and regulatory requirements.
Regulatory Compliance: Cereals powder making machines are subject to rigorous regulatory frameworks that ensure food safety and quality. Compliance involves adhering to standards set by food safety authorities regarding hygiene, material compatibility, and production processes. Manufacturers must certify their equipment meets these standards, providing assurance to food producers of their reliability and safety in food processing environments.
Safety Standards: Ensuring operator safety and preventing product contamination are critical aspects governed by safety standards. Cereals powder making machines are equipped with safety features such as emergency stop mechanisms, protective guards, and sanitation-friendly designs to mitigate risks during operation and facilitate thorough cleaning between batches.
Quality Assurance: Beyond safety, these machines play a crucial role in maintaining the integrity and quality of cereals during processing. Precision engineering ensures consistent particle size reduction while preserving nutritional value and flavor profiles. Compliance with quality assurance protocols involves testing and validation procedures to verify the machine's performance and adherence to specifications.
Future Trends in Cereals Powder Making
The future of cereals powder making machines is poised for significant advancements driven by innovation, sustainability, and efficiency. As consumer demand for healthy, convenient, and high-quality cereal products increases, manufacturers are investing in state-of-the-art technologies to enhance production processes.
One key trend is the integration of automation and smart technologies. Advanced cereals powder making machines are being equipped with IoT (Internet of Things) capabilities, allowing for real-time monitoring and control of the production line. This ensures consistent quality, reduces downtime, and enhances overall operational efficiency. Manufacturers can remotely monitor machine performance, predict maintenance needs, and optimize production schedules, resulting in reduced operational costs and increased productivity.
Sustainability is another crucial trend shaping the future of cereals powder making machines. With growing environmental concerns, manufacturers are focusing on eco-friendly production methods. This includes the development of energy-efficient machinery, the use of biodegradable packaging materials, and the implementation of waste reduction techniques. By adopting sustainable practices, companies can minimize their environmental footprint and appeal to environmentally conscious consumers.
Innovations in processing technologies are also transforming the cereals powder industry. Techniques such as spray drying, freeze drying, and extrusion are being refined to improve the nutritional profile and sensory properties of cereal powders. These advancements enable the production of high-quality products that retain essential nutrients and have an extended shelf life, meeting the demands of health-conscious consumers.
Customization and flexibility in production are becoming increasingly important. Modern cereals powder making machines are designed to handle a wide range of raw materials and formulations, allowing manufacturers to produce diverse products tailored to specific consumer preferences. This flexibility is crucial for staying competitive in a market where consumer tastes and dietary needs are constantly evolving.
Reference
The following are five authoritative foreign literature websites in the field of Industrial food machinery:
1. Food Engineering Magazine
Website: https://www.foodengineeringmag.com/
2.Food Processing Magazine
Website: https://www.foodprocessing.com/
3.Journal of Food Engineering
Website:https://www.journals.elsevier.com/journal-of-food-engineering
4. Food Manufacturing Magazine
Website:https://www.foodmanufacturing.com/
5. International Journal of Food Science & Technology
Website:https://onlinelibrary.wiley.com/