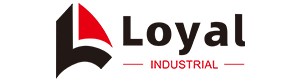
- Shandong Loyal Industrial Co.,Ltd.
- Macaroni Production Machine Instant Noodle Machine Biscuit Making Machine

Home> Company News> Unlock The Secrets Of Efficient nutrition baby powder food production line Manufacturing

Unlock The Secrets Of Efficient nutrition baby powder food production line Manufacturing
2024-07-22 14:23:37Understanding Fully Automatic Nutrition Baby Powder Food Production Lines
The modern landscape of food production demands precision, consistency, and efficiency, especially in nutrition baby powder food production lines. These lines are designed with advanced technologies that automate various stages of production, from ingredient handling to packaging.
At the core of these fully automatic systems are sophisticated machinery and software solutions that work seamlessly together. Key components include automated mixing and blending units, precise dosing systems for vitamins and minerals, automated filling and sealing machines, and integrated quality control sensors. These elements not only ensure uniform product quality but also contribute significantly to operational efficiency.
One of the primary benefits of fully automatic nutrition baby powder food production lines is their ability to minimize human intervention while maximizing output. This reduces the margin of error and enhances overall production efficiency. By automating repetitive tasks, manufacturers can achieve higher throughput rates and meet increasing market demands without compromising on product consistency or safety.
Energy savings are another crucial aspect of these advanced production lines. Through innovative design and technology, modern systems are engineered to optimize energy consumption at every stage of the production process. This includes efficient heating and cooling mechanisms, smart energy management systems, and the use of eco-friendly materials where possible. Such initiatives not only lower operational costs but also align with global sustainability goals.
Definition and Characteristics of Fully Automatic Production Lines
In the realm of food machinery, fully automatic production lines represent the pinnacle of efficiency and precision. These systems are meticulously engineered to handle the entire production process of nutrition baby powder foods with minimal human intervention, leveraging advanced technologies to optimize every stage from ingredient handling to packaging.
A fully automatic nutrition baby powder food production line typically consists of interconnected modules that work seamlessly together. These modules include:
Automated Ingredient Handling |
Advanced systems for precise measurement and dispensing of ingredients, ensuring consistency and accuracy in recipe formulation. |
Processing Equipment |
High-performance machinery such as mixers, blenders, and reactors equipped with automation features to control mixing times, temperatures, and other critical parameters. |
Cooking and Heating Systems |
Automated ovens, steamers, and heating chambers that maintain uniform cooking conditions, essential for achieving desired product characteristics. |
Packaging and Labeling |
: Integrated packaging lines with robotic arms for efficient filling, sealing, and labeling of final products, reducing manual labor and packaging errors. |
Key characteristics of these systems include real-time monitoring and control capabilities, allowing operators to oversee production metrics and adjust processes as needed for optimal efficiency and quality. Remote accessibility and data analytics further enhance operational insights, enabling proactive maintenance and continuous improvement.
In summary, fully automatic production lines for nutrition baby powder foods embody precision, efficiency, and reliability. They enable food manufacturers to meet stringent production demands while achieving significant savings in time, labor, and resources.
Technological Innovations for Efficiency
In the realm of nutrition baby powder food production lines, technological advancements have been pivotal in enhancing both efficiency and energy savings. These innovations encompass various aspects of production, from ingredient handling to final packaging.
1.Advanced Ingredient Handling Systems
One of the critical areas of improvement lies in ingredient handling systems. Automated systems now feature precise dosing mechanisms controlled by advanced sensors and software algorithms. This ensures that ingredients are accurately measured and mixed, reducing waste and optimizing raw material usage. Integrated conveyor systems further streamline the flow of ingredients, minimizing manual intervention and enhancing throughput.
2.Precision Mixing and Blending Technology
The advent of precision mixing and blending technology has revolutionized the production of nutrition baby powder foods. High-speed mixers equipped with automated controls ensure consistent product quality batch after batch. These systems can adjust mixing parameters in real-time based on feedback from sensors, maintaining optimal blend homogeneity while minimizing energy consumption.
3.Energy-Efficient Drying and Packaging Systems
Efficient drying and packaging are crucial stages in the nutrition baby powder food production line, where advancements have significantly boosted overall efficiency and energy savings.
4.Innovative Drying Techniques
Modern production lines integrate innovative drying techniques such as vacuum drying and infrared drying. These methods reduce drying time and energy consumption compared to traditional methods like hot air drying. Vacuum drying, for instance, operates at lower temperatures, preserving the nutritional integrity of the product while minimizing energy expenditure. Infrared drying, on the other hand, uses radiant heat to quickly evaporate moisture, further enhancing efficiency.
6.Automated Packaging Solutions
Automation in packaging has revolutionized the final stages of production. Fully automated packaging systems now include robotic arms equipped with vision systems for precise product handling and packaging. These systems can handle various packaging formats and sizes, optimizing material usage and reducing packaging waste. Automated labeling and barcode systems ensure traceability and compliance with regulatory standards, enhancing operational efficiency and product safety.
Advanced Machinery and Equipment Used in Automated Production
In the realm of nutrition baby powder food production lines, the adoption of advanced machinery and equipment has been instrumental in achieving high efficiency and energy-saving goals.
Automated Mixing and Processing Systems
Central to the efficiency of nutrition baby powder food production lines are automated mixing and processing systems. These systems incorporate sophisticated technologies such as PLC (Programmable Logic Controller) integration and SCADA (Supervisory Control and Data Acquisition) systems. PLCs manage and regulate the entire production process, from ingredient dosing to final blending, ensuring precise control over every aspect of production. SCADA systems provide real-time monitoring and data acquisition, allowing operators to optimize production parameters for maximum efficiency and quality consistency.
High-Speed Filling and Sealing Machines
The introduction of high-speed filling and sealing machines has significantly enhanced the packaging efficiency of nutrition baby powder food production lines. These machines utilize advanced filling techniques, such as volumetric and gravimetric filling, to ensure accurate portioning and minimize product giveaway. Automated sealing mechanisms, including heat sealing and ultrasonic sealing, maintain product freshness and integrity while reducing energy consumption through optimized sealing times and temperatures.
Robotic Handling and Palletizing Systems
Robotic handling and palletizing systems have revolutionized material handling within nutrition baby powder food production lines. These systems feature articulated robotic arms equipped with end-of-arm tools (EOAT) tailored for specific tasks such as product picking, sorting, and palletizing. Vision-guided robotics enable precise and efficient handling of products, minimizing errors and downtime. Integrated palletizing systems further streamline operations by automatically stacking finished products onto pallets according to predefined patterns, optimizing warehouse space and facilitating seamless logistics.
IoT Integration in Fully Automatic Nutrition Baby Powder Food Production Line
Introduction to IoT Integration
In recent years, the integration of Internet of Things (IoT) technology has revolutionized the landscape of industrial food machinery, particularly in the production of nutrition baby powder food. IoT refers to the network of interconnected devices that collect and exchange data seamlessly, enabling real-time monitoring and control of manufacturing processes.
Role of IoT in Optimizing Efficiency
IoT plays a pivotal role in enhancing the efficiency of fully automatic nutrition baby powder food production lines. By embedding sensors and smart devices throughout the production process, manufacturers gain unprecedented visibility into operational metrics such as temperature, humidity, production speed, and equipment performance.
Real-time Monitoring and Control
One of the key advantages of IoT integration is real-time monitoring and control capabilities. Through continuous data acquisition and analysis, operators can proactively identify inefficiencies or potential issues before they escalate, thereby minimizing downtime and optimizing production output.
Predictive Maintenance
IoT-enabled systems facilitate predictive maintenance practices by monitoring the condition and performance of machinery in real time. By analyzing data patterns and equipment metrics, maintenance schedules can be optimized, reducing the likelihood of unexpected breakdowns and ensuring uninterrupted production cycles.
Enhanced Quality Control
Another significant benefit of IoT integration is enhanced quality control measures. By monitoring critical parameters throughout the production line, such as ingredient proportions and mixing consistency, manufacturers can maintain high standards of product quality and consistency.
Data-Driven Decision Making
Furthermore, IoT-generated data empowers decision makers with actionable insights. By leveraging analytics and machine learning algorithms, manufacturers can make informed decisions regarding process optimization, resource allocation, and product innovation.
Strategies for Energy Saving
Introduction to Energy Efficiency
Energy consumption is a critical factor in the operation of fully automatic nutrition baby powder food production lines. Implementing effective strategies for energy saving not only reduces operational costs but also enhances sustainability efforts in food manufacturing.
Utilization of Energy-Efficient Equipment
The first strategy involves the deployment of energy-efficient machinery and technologies. Modern production lines are equipped with state-of-the-art components such as variable frequency drives (VFDs), energy-efficient motors, and LED lighting systems. These upgrades minimize energy wastage during operation without compromising production output.
Optimal Process Design
Optimizing the process design plays a crucial role in energy conservation. By streamlining workflow sequences and minimizing idle times between production stages, manufacturers can achieve significant energy savings. Continuous process improvement initiatives, guided by data analytics from IoT-enabled systems, help identify bottlenecks and optimize energy-intensive operations.
Heat Recovery Systems
Integrating heat recovery systems is another effective strategy for energy conservation. In production environments where heat is generated as a byproduct, such as drying or baking processes, capturing and recycling this thermal energy reduces reliance on external heating sources. Heat exchangers and thermal insulation techniques maximize the efficiency of heat recovery systems, contributing to overall energy savings.
Automation and Control Systems
Automation plays a pivotal role in energy management by ensuring precise control over equipment operation and energy consumption. Advanced control systems optimize energy usage based on real-time production demands, adjusting settings such as temperature, pressure, and airflow to minimize energy waste. Integration with IoT platforms enables continuous monitoring and adjustment of energy parameters, further enhancing efficiency.
Employee Training and Awareness
Lastly, fostering a culture of energy awareness among employees is essential for sustaining energy-saving initiatives. Training programs on energy-efficient practices and proactive maintenance routines empower staff to contribute to energy conservation efforts. Engaging employees in continuous improvement processes encourages innovative ideas for optimizing energy consumption across all operational levels.
Lessons Learned and Potential for Industry Adoption
Evolution of Automation in Food Machinery
The journey towards fully automatic nutrition baby powder food production lines has been marked by significant advancements in automation technology. From manual operations to semi-automated systems and now to fully integrated solutions, the industry has witnessed a transformative shift in production capabilities and efficiency.
Benefits of Fully Automatic Systems
Fully automatic production lines offer unparalleled benefits in terms of productivity, consistency, and quality control. By eliminating human error and streamlining workflows, manufacturers can achieve higher throughput rates with reduced labor costs. Moreover, the precision of automated systems ensures consistent product quality, meeting stringent regulatory and consumer standards.
Case Studies of Successful Implementations
Several industry leaders have successfully implemented fully automatic nutrition baby powder food production lines, showcasing exemplary use cases. These case studies highlight measurable improvements in production efficiency, energy savings, and overall operational agility. Companies that have embraced automation early on have gained a competitive edge by optimizing resource utilization and enhancing product innovation capabilities.
Overcoming Challenges and Obstacles
While the adoption of fully automatic systems promises substantial benefits, it also presents challenges that require careful consideration. Common obstacles include initial investment costs, technical integration complexities, and the need for specialized workforce training. Overcoming these challenges involves strategic planning, collaboration with technology partners, and continuous adaptation to evolving industry standards.
Potential for Industry-wide Adoption
The potential for widespread adoption of fully automatic nutrition baby powder food production lines is immense. As technology continues to evolve, solutions become more accessible and cost-effective for medium to small-scale manufacturers. The scalability of automated systems enables companies to customize production processes according to market demands while maintaining operational flexibility and sustainability.
Future Outlook and Innovation
Looking ahead, the future of food machinery lies in continuous innovation and integration of emerging technologies. Trends such as artificial intelligence (AI), machine learning, and predictive analytics will further enhance the capabilities of automated production lines. These advancements will not only optimize energy efficiency but also pave the way for smarter, more adaptive manufacturing practices across the food industry.
Reference
The following are five authoritative foreign literature websites in the field of Industrial food machinery:
1. Food Engineering Magazine
Website: https://www.foodengineeringmag.com/
2.Food Processing Magazine
Website: https://www.foodprocessing.com/
3.Journal of Food Engineering
Website:https://www.journals.elsevier.com/journal-of-food-engineering
4. Food Manufacturing Magazine
Website:https://www.foodmanufacturing.com/
5. International Journal of Food Science & Technology
Website:https://onlinelibrary.wiley.com/