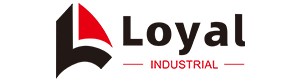
- Shandong Loyal Industrial Co.,Ltd.
- Macaroni Production Machine Instant Noodle Machine Biscuit Making Machine

Home> Company News> Everything You Need To Know About nutritional powder processing line

Everything You Need To Know About nutritional powder processing line
2024-08-08 11:33:54Brief Overview of the Nutritional Powder Industry and Its Significance
The nutritional powder industry has emerged as a vital segment within the broader food and beverage sector, catering to the evolving health and wellness needs of consumers globally. This industry specializes in the production of powdered formulations enriched with essential nutrients, vitamins, minerals, proteins, and other bioactive compounds, tailored to meet specific dietary requirements or health goals.
The significance of the nutritional powder industry lies in its ability to provide convenient, shelf-stable, and easily customizable nutrition solutions. These powders can be consumed directly, mixed into beverages or smoothies, or incorporated into various food products, offering flexibility and versatility in nutrition delivery. They are particularly popular among athletes, fitness enthusiasts, the elderly, and individuals with specific dietary restrictions or nutritional deficiencies.
In recent years, the industry has witnessed significant growth, fueled by several key factors. Firstly, there is a heightened awareness among consumers regarding the importance of maintaining optimal nutrition for overall health and wellbeing. This has led to a surge in demand for high-quality, fortified nutritional products. Secondly, advancements in food technology and processing methods have enabled manufacturers to produce more sophisticated and efficacious powders with improved bioavailability and stability.
Furthermore, the nutritional powder industry plays a pivotal role in addressing global health challenges such as malnutrition, anemia, and micronutrient deficiencies. By providing accessible and affordable nutrition solutions, these powders contribute to improving public health outcomes and reducing healthcare costs associated with nutrient deficiencies.
As the industry continues to evolve, there is a growing emphasis on sustainability, traceability, and transparency. Consumers are increasingly seeking products that are not only effective but also ethically and environmentally responsible. This trend has prompted manufacturers to adopt more sustainable production practices, such as using renewable energy sources, minimizing waste, and implementing circular economy principles.
Amidst this backdrop, the fully automated nutritional powder processing line emerges as a game-changer. By integrating advanced automation technologies, these processing lines enable manufacturers to achieve unprecedented levels of efficiency, consistency, and quality control while minimizing energy consumption and environmental impact. As the industry progresses, it is evident that the fully automated nutritional powder processing line will play a pivotal role in shaping the future of nutrition and health.
Understanding the Fully Automated Nutritional Powder Processing Line
In the fast-paced world of the food and beverage industry, manufacturers are constantly seeking innovative solutions to streamline production processes, enhance product quality, and reduce operational costs. The fully automated nutritional powder processing line stands as a testament to this relentless pursuit of excellence, offering pioneering high-efficiency and energy-saving solutions that redefine the standard for nutritional powder production.
Core Components of the Processing Line
At the foundation of the fully automated nutritional powder processing line lies a complex yet highly orchestrated system of machinery and technology. Key components include:
Automated Feeders & Conveyors |
These precision-engineered devices automatically meter and deliver raw materials to the mixing stage, ensuring consistent and accurate ingredient ratios. The elimination of manual handling reduces the risk of contamination and streamlines the entire production process. |
High-Shear Mixers & Homogenizers |
Equipped with advanced mixing technologies, these machines thoroughly blend ingredients to create a uniform and smooth powder. Customizable settings allow manufacturers to tailor the mixing process to meet specific product requirements, ensuring optimal nutrient distribution and consistent quality. |
Drying Systems |
After mixing, the powder undergoes a controlled drying process to remove moisture and stabilize the product. Automated temperature and humidity control systems optimize the drying process for each product, preserving nutritional integrity and extending shelf life. |
Milling Equipment |
Precision milling machines grind the dried powder to achieve the desired particle size and texture. Adjustable settings and precision screens ensure consistent particle distribution, eliminating the need for manual sieving or sorting. |
Automated Packaging Machines |
The final stage of the processing line involves packaging the nutritional powder into containers or sachets. Automated filling and sealing machines ensure accurate packaging, minimizing waste and maximizing production speed. |
Benefits of Automation:
Increased Efficiency |
Automation eliminates manual tasks, reducing labor costs and freeing up employees for more value-added activities. This results in faster production cycles and increased throughput. |
Improved Product Quality |
Precision control over mixing, drying, and milling parameters ensures consistent product quality and eliminates variations caused by human error. |
Enhanced Food Safety |
Automated systems minimize the risk of contamination by reducing human contact with raw materials and finished products. This helps manufacturers comply with strict food safety regulations. |
Reduced Energy Consumption |
Advanced energy-saving technologies integrated into the processing line help manufacturers reduce their carbon footprint and lower operational costs. Conclusion |
The fully automated nutritional powder processing line represents a game-changing solution for manufacturers in the food and beverage industry. By combining high-efficiency and energy-saving technologies, this system enables the production of high-quality nutritional powders with minimal human intervention. As the industry continues to evolve, the adoption of automated processing lines will become increasingly crucial for manufacturers seeking to stay ahead of the competition and meet the demands of consumers worldwide.
Energy-Saving Strategies in the Processing Line
In the realm of industrial food machinery, energy efficiency is not just a buzzword; it's a vital aspect of sustainable production that can significantly impact a manufacturer's bottom line. The fully automated nutritional powder processing line, being a pinnacle of modern food production technology, incorporates various energy-saving strategies that minimize the environmental footprint and maximize operational efficiency. Here, we delve into some of these innovative approaches that contribute to the pioneering high-efficiency and energy-saving solutions offered by these advanced systems.
1. Optimized Heating and Drying Processes
One of the most energy-intensive stages in nutritional powder production is the drying process. To mitigate this, modern processing lines incorporate advanced drying systems that utilize optimized heating profiles and energy-efficient heat exchangers. These systems precisely control the temperature and humidity during drying, ensuring that energy is used efficiently while maintaining product quality. Furthermore, heat recovery systems capture and reuse waste heat generated during the process, further reducing energy consumption.
2. Variable Speed Drives (VSDs) for Motors
Throughout the processing line, motors power various machines, including mixers, conveyors, and packaging equipment. By equipping these motors with variable speed drives (VSDs), manufacturers can adjust their speed according to the specific requirements of each stage of the process. This not only enhances precision and control but also significantly reduces energy consumption, as motors can operate at optimal efficiency points, rather than running at fixed speeds.
3. Energy-Efficient Lighting and HVAC Systems
Facilities housing fully automated nutritional powder processing lines often require extensive lighting and heating, ventilation, and air conditioning (HVAC) systems to maintain optimal production conditions. By adopting energy-efficient LED lighting and implementing smart HVAC systems that automatically adjust based on occupancy and production needs, manufacturers can significantly reduce their energy usage.
4. Automation and Intelligent Control Systems
At the heart of every fully automated nutritional powder processing line lies an intelligent control system that oversees and optimizes the entire production process. These systems leverage advanced algorithms and real-time data analytics to identify inefficiencies and make adjustments to minimize energy consumption. For instance, they can automatically adjust machine settings to minimize energy usage during low-demand periods or optimize production schedules to reduce idle time.
5. Regenerative Braking and Energy Recovery
In processing lines where heavy machinery is involved, regenerative braking systems can harness the energy generated during deceleration and braking to recharge the system or power other components. This energy recovery mechanism not only reduces energy waste but also minimizes wear and tear on braking components, extending the overall lifespan of the machinery.
Real-time monitoring and control systems
In the realm of modern food machinery, the integration of real-time monitoring and control systems into the fully automated nutritional powder processing line represents a significant leap forward in terms of operational efficiency, product quality, and energy savings. As an industrial food machinery expert, I will delve into the intricacies of these systems and their pivotal role in pioneering high-efficiency and energy-saving solutions.
The Essence of Real-Time Monitoring |
Real-time monitoring refers to the continuous and instantaneous tracking of critical process parameters throughout the nutritional powder production cycle. These parameters can include temperature, pressure, flow rates, humidity levels, and even the chemical composition of raw materials and intermediates. By capturing this data in real-time, manufacturers can gain unparalleled insights into the status of their production line, enabling them to identify and address potential issues before they escalate into full-blown problems. |
The Power of Control Systems |
The real-time monitoring capabilities are complemented by sophisticated control systems that automatically adjust process variables to maintain optimal conditions. These control systems employ advanced algorithms and predictive analytics to anticipate changes in process dynamics and preemptively adjust equipment settings to ensure consistent product quality and maximize energy efficiency. For instance, if the system detects a slight deviation in temperature, it can automatically adjust the cooling or heating elements to maintain the desired temperature range. |
Integration with Automation |
The seamless integration of real-time monitoring and control systems with the overall automation architecture of the nutritional powder processing line is crucial. This integration ensures that data is seamlessly transmitted between different stages of the production process, enabling operators to have a comprehensive view of the entire line's performance. Additionally, it allows for the coordination of multiple machines and equipment, ensuring that they operate in harmony to achieve the desired production outcomes. |
Benefits of Real-Time Monitoring and Control:
Enhanced Product Quality: By maintaining tight control over process variables, manufacturers can ensure consistent product quality, reducing the risk of batch-to-batch variability.
Increased Efficiency: Real-time monitoring and control systems enable manufacturers to optimize production processes, reducing waste and downtime, and increasing overall throughput.
Reduced Energy Consumption: By preemptively adjusting equipment settings to maintain optimal conditions, these systems minimize energy waste and contribute to energy-saving solutions.
Improved Safety: Continuous monitoring of critical process parameters can help prevent accidents and ensure the safe operation of the production line.
Data-Driven Decision Making: The vast amounts of data generated by these systems provide manufacturers with valuable insights into their production processes, enabling them to make data-driven decisions that drive continuous improvement.
Emerging technologies and their impact on the processing line
In the ever-evolving landscape of food machinery, emerging technologies are reshaping the fully automated nutritional powder processing line, driving it towards unprecedented levels of high-efficiency and energy-saving solutions. As an industrial food machinery expert, I will delve into the latest technological advancements and their profound impact on this critical production process.
1.Precision Instrumentation and Sensors
One of the most significant emerging technologies transforming the nutritional powder processing line is the use of precision instrumentation and sensors. These advanced devices enable real-time monitoring of critical process parameters with unprecedented accuracy and reliability. From temperature and pressure sensors to flow meters and particle size analyzers, these instruments provide manufacturers with a wealth of data that can be leveraged to optimize production processes and ensure consistent product quality.
2.Artificial Intelligence and Machine Learning
The integration of artificial intelligence (AI) and machine learning (ML) algorithms into the processing line is another game-changing technology. By analyzing vast amounts of data generated by sensors and instrumentation, AI and ML systems can identify patterns, predict trends, and make autonomous decisions that optimize production efficiency and reduce energy consumption. For instance, these systems can automatically adjust equipment settings based on real-time process data, minimizing waste and downtime.
3.Automation and Robotics
Advancements in automation and robotics technologies are also having a profound impact on the nutritional powder processing line. Highly automated systems, including robotic arms and automated conveyors, streamline material handling, reduce human error, and enhance safety. These technologies enable manufacturers to operate their processing lines with minimal human intervention, freeing up labor resources for more value-added tasks.
4.Internet of Things (IoT) Integration
The Internet of Things (IoT) is another emerging technology that is revolutionizing the nutritional powder processing line. By connecting various machines, equipment, and sensors to the cloud, IoT enables manufacturers to remotely monitor and control their production processes from anywhere in the world. This connectivity also facilitates data sharing and collaboration between different departments and stakeholders, leading to more informed decision-making and continuous improvement.
5.Sustainability and Environmental Considerations
Emerging technologies are also driving the nutritional powder processing line towards greater sustainability and environmental responsibility. For instance, advanced energy management systems can optimize energy consumption, reducing the carbon footprint of production processes. Additionally, innovative waste reduction technologies, such as recycling and repurposing systems, are being integrated into processing lines to minimize waste generation and promote circular economy principles.
Reference
The following are five authoritative foreign literature websites in the field of Industrial food machinery:
1. Food Engineering Magazine
Website: https://www.foodengineeringmag.com/
2.Food Processing Magazine
Website: https://www.foodprocessing.com/
3.Journal of Food Engineering
Website:https://www.journals.elsevier.com/journal-of-food-engineering
4. Food Manufacturing Magazine
Website:https://www.foodmanufacturing.com/
5. International Journal of Food Science & Technology
Website:https://onlinelibrary.wiley.com/