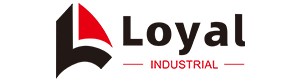
- Shandong Loyal Industrial Co.,Ltd.
- Macaroni Production Machine Instant Noodle Machine Biscuit Making Machine

Home> Company News> Discovering The World Of nutritional powder production line

Discovering The World Of nutritional powder production line
2024-08-09 12:04:16Thesis statement highlighting the benefits of such a production line
In the realm of food manufacturing, the production of nutritional powders has evolved significantly over the years, driven by advancements in technology and the ever-growing demand for high-quality, nutritious supplements. At the forefront of this evolution stands the fully automated, high-efficiency nutritional powder production line, which represents a game-changing approach to streamlining the production process.
The adoption of such a production line offers numerous benefits that cannot be overlooked. Firstly, it significantly enhances production capacity and throughput, allowing manufacturers to meet the escalating market demands with ease. By automating key processes, the line eliminates bottlenecks and ensures a smooth, continuous flow of production, resulting in increased efficiency and reduced downtime.
Moreover, the precision control and customization capabilities of a fully automated production line ensure that every batch of nutritional powder produced meets the highest standards of quality and consistency. This is crucial in the highly competitive nutritional supplement market, where consumers demand products that are not only effective but also safe and reliable.
Another significant advantage lies in the cost savings associated with automation. By reducing the reliance on manual labor, the production line minimizes labor costs and eliminates the risk of human error, which can lead to costly mistakes and product recalls. Furthermore, the energy-saving features of modern automated equipment contribute to a more sustainable production process, aligning with the growing consumer preference for eco-friendly products.
From a workplace safety perspective, a fully automated nutritional powder production line also offers significant benefits. It eliminates the need for workers to perform hazardous or repetitive tasks, reducing the risk of injuries and improving overall workplace safety. Additionally, the enhanced hygiene and safety standards achieved through automation help to maintain the integrity of the product and ensure consumer trust.
In conclusion, the benefits of a fully automated, high-efficiency nutritional powder production line are multifaceted and far-reaching. From increased production capacity and cost savings to improved product quality and workplace safety, the adoption of such a production line represents a strategic move for any manufacturer looking to stay ahead in the competitive nutritional supplement market. As an industrial food machinery expert, I strongly recommend that businesses consider investing in this cutting-edge technology to streamline their production processes and drive long-term success.
Traditional Methods of Nutritional Powder Production and Their Limitations
Before delving into the benefits of a fully automated, high-efficiency nutritional powder production line, it is essential to understand the traditional methods of production and their inherent limitations.
In the past, the production of nutritional powders often relied heavily on manual labor and semi-automated equipment. This involved a series of steps, including mixing raw ingredients, drying the mixture, and grinding it into a fine powder. While these methods were effective in producing nutritional powders, they were time-consuming and prone to inconsistencies.
One of the primary limitations of traditional production methods was the lack of precision in ingredient mixing. Manual mixing could lead to uneven distribution of nutrients, resulting in variations in the quality and efficacy of the final product. Furthermore, the drying and grinding processes were often inefficient, requiring significant amounts of time and energy. This not only increased production costs but also limited the scalability of the process.
Another significant limitation was the risk of contamination. Without advanced cleaning and sterilization systems, traditional production methods were vulnerable to microbial and particulate contamination. This posed a significant threat to food safety, particularly when producing powders intended for vulnerable populations such as infants and the elderly.
Moreover, traditional production methods lacked the flexibility to adapt to changing market demands. Customizing formulations and adjusting production volumes required significant downtime and manual intervention, making it difficult for manufacturers to respond quickly to market trends and consumer preferences.
Additionally, the reliance on manual labor made the production process susceptible to human error. Mishandling of raw materials, incorrect dosing of ingredients, or overlooking critical steps in the production process could all lead to product defects or recalls.
In conclusion, while traditional methods of nutritional powder production were once the norm, they are now increasingly being replaced by fully automated, high-efficiency production lines. These modern systems overcome the limitations of traditional methods, providing manufacturers with a more precise, efficient, and safe way to produce nutritional powders. As an industrial food machinery expert, I strongly recommend embracing these advancements to stay competitive in the rapidly evolving food manufacturing industry.
Key Features of a Fully Automated, High-Efficiency Nutritional Powder Production Line
A fully automated, high-efficiency nutritional powder production line represents a significant advancement in the food manufacturing industry. These modern systems integrate advanced technologies and automation to streamline the production process, enhancing quality, safety, and productivity. As an industrial food machinery expert, let's explore the key features that define such a production line.
Precision Ingredient Handling and Mixing |
At the heart of a fully automated nutritional powder production line lies precision ingredient handling and mixing capabilities. The system utilizes automated weighing and dosing systems to ensure accurate ingredient measurements, eliminating the risk of human error. Advanced mixing technologies, such as planetary mixers or twin-screw extruders, ensure uniform distribution of nutrients, resulting in consistent product quality. |
Advanced Drying and Grinding Technologies |
Once the ingredients are mixed, the next critical step is drying and grinding. A fully automated production line employs cutting-edge drying technologies, such as spray drying or freeze-drying, to preserve nutrient integrity while effectively removing moisture. Following drying, the product is then passed through high-precision grinding mills to achieve the desired particle size and texture. These advanced technologies ensure rapid and efficient processing, minimizing energy consumption and production time. |
Integrated Cleaning and Sterilization Systems |
Food safety is paramount in nutritional powder production. A fully automated, high-efficiency line incorporates integrated cleaning and sterilization systems to ensure hygienic conditions throughout the process. These systems use high-pressure water jets, steam, or chemical solutions to remove residues and microorganisms, minimizing the risk of contamination. Additionally, automatic sanitization protocols are in place to maintain equipment cleanliness between batches. |
Flexibility and Scalability |
Another defining feature of a fully automated production line is its flexibility and scalability. Manufacturers can easily adjust formulations and production volumes to meet changing market demands. The system can seamlessly switch between different product recipes, minimizing downtime and production costs. Furthermore, the production line can be scaled up or down depending on production requirements, ensuring optimal resource utilization. |
Real-Time Monitoring and Control |
To maintain consistent product quality and ensure efficient operations, a fully automated nutritional powder production line integrates real-time monitoring and control systems. These systems provide real-time data on critical process parameters, such as temperature, humidity, and mixing time, enabling operators to make adjustments as needed. Furthermore, automated fault detection and diagnosis capabilities minimize downtime and reduce maintenance costs. |
Implementation Considerations
When contemplating the implementation of a fully automated, high-efficiency nutritional powder production line, several critical considerations must be taken into account to ensure a successful transition and maximize the benefits of automation. As an industrial food machinery expert, I outline the key factors that manufacturers should evaluate before embarking on this journey.
Assess Current Production Needs and Goals |
The first step in the implementation process is to thoroughly assess your current production needs and future goals. Identify areas where automation can enhance efficiency, reduce costs, or improve product quality. Consider factors such as production capacity, product diversity, and market demand trends. This assessment will help you determine the scope and scale of the automation project, ensuring that the investment aligns with your business objectives. |
Evaluate Technical Requirements and Infrastructure |
A fully automated nutritional powder production line requires a robust technical infrastructure to support its operation. Evaluate your existing facilities to ensure they can accommodate the new equipment, including power requirements, space allocation, and ventilation systems. Additionally, assess the technical expertise of your team and consider the need for additional training or hiring specialized personnel. |
Choose the Right Equipment and Technology |
Selecting the appropriate equipment and technology is crucial for the success of your automation project. Research various suppliers and compare their offerings based on factors such as performance, reliability, maintenance costs, and compatibility with your existing systems. Consider the latest advancements in automation technologies, such as AI-driven process control, predictive maintenance, and IoT integration, to enhance the efficiency and intelligence of your production line. |
Develop a Comprehensive Implementation Plan |
A detailed implementation plan is essential for a smooth transition to a fully automated production line. This plan should outline the project timeline, milestones, resource allocation, and risk management strategies. It should also include a comprehensive training program for your team to ensure they are proficient in operating and maintaining the new equipment. Additionally, consider the impact of the automation project on your supply chain and logistics operations, and plan accordingly. |
Address Regulatory Compliance and Food Safety |
Food safety and regulatory compliance are paramount in the nutritional powder industry. Ensure that your automation project adheres to all relevant food safety regulations and standards. This includes implementing robust cleaning and sterilization protocols, maintaining accurate records, and ensuring that all equipment meets the necessary hygiene requirements. Additionally, stay informed about any changes in regulations or industry standards to ensure ongoing compliance. |
Monitor and Optimize Performance |
Once the fully automated production line is operational, it's essential to continuously monitor and optimize its performance. Utilize real-time monitoring systems to track key performance indicators (KPIs) such as production rates, energy consumption, and product quality. Regularly review data to identify areas for improvement and make adjustments as needed. Additionally, consider implementing predictive maintenance programs to minimize downtime and extend equipment lifespan. |
Future Trends and Innovations in Nutritional Powder Production
In the realm of nutritional powder production, the landscape is rapidly evolving, driven by advancements in technology, consumer preferences, and regulatory requirements. As an industrial food machinery expert, I delve into the future trends and innovations that are shaping the industry, focusing on how they can streamline production processes and enhance the quality and versatility of nutritional powders.
1. Advanced Automation and Robotics
One of the most significant trends in nutritional powder production is the increasing adoption of advanced automation and robotics. Fully automated production lines equipped with intelligent robots and automation systems are becoming the norm, as they enable manufacturers to achieve unprecedented levels of precision, efficiency, and flexibility. These systems can handle complex tasks such as ingredient blending, drying, milling, and packaging with minimal human intervention, reducing errors and enhancing product consistency.
2. Integration of IoT and AI
The Internet of Things (IoT) and Artificial Intelligence (AI) are transforming the way nutritional powder production is managed. By integrating IoT sensors and AI algorithms into production lines, manufacturers can collect real-time data on process parameters, equipment performance, and product quality. This data can then be analyzed to optimize production processes, predict maintenance needs, and detect potential issues before they become problems. Additionally, AI-driven process control systems can automatically adjust process variables to maintain optimal conditions, ensuring consistent product quality and reducing waste.
3. Sustainability and Eco-Efficiency
Sustainability is becoming a key driver of innovation in the nutritional powder industry. Manufacturers are increasingly focused on reducing their environmental footprint by adopting eco-efficient production methods. This includes the use of energy-efficient equipment, sustainable packaging materials, and recycling programs for waste products. Additionally, research is ongoing to develop new technologies that can convert by-products and waste streams into valuable ingredients for nutritional powders, further enhancing sustainability.
4. Personalization and Customization
Consumer demand for personalized and customized nutritional products is on the rise. To meet this demand, manufacturers are investing in technologies that enable the production of small batches and tailored formulations. This includes the use of flexible production lines that can quickly switch between different products and formulations, as well as the development of novel ingredients and delivery systems that cater to specific dietary needs and preferences.
5. Enhanced Product Quality and Safety
The focus on product quality and safety remains paramount in the nutritional powder industry. To ensure that products meet the highest standards, manufacturers are investing in advanced quality control systems and testing methods. This includes the use of inline sensors and imaging technologies to monitor product characteristics in real-time, as well as the adoption of traceability systems that can track raw materials and finished products throughout the supply chain. Additionally, research is ongoing to develop new preservation techniques and packaging solutions that can extend product shelf life and maintain nutritional integrity.
Reference
The following are five authoritative foreign literature websites in the field of Industrial food machinery:
1. Food Engineering Magazine
Website: https://www.foodengineeringmag.com/
2.Food Processing Magazine
Website: https://www.foodprocessing.com/
3.Journal of Food Engineering
Website:https://www.journals.elsevier.com/journal-of-food-engineering
4. Food Manufacturing Magazine
Website:https://www.foodmanufacturing.com/
5. International Journal of Food Science & Technology
Website:https://onlinelibrary.wiley.com/