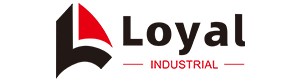
- Shandong Loyal Industrial Co.,Ltd.
- Macaroni Production Machine Instant Noodle Machine Biscuit Making Machine

Home> Company News> The Ultimate Guide To conical twin screw extruder Updated 2024

The Ultimate Guide To conical twin screw extruder Updated 2024
2024-10-10 11:22:18Brief Overview of Conical Twin Screw Extruders
In the realm of industrial food machinery, the conical twin screw extruder has emerged as a highly versatile and efficient tool for processing a wide range of food materials.
The conical twin screw extruder is characterized by its unique design, which features two intermeshing screws that rotate within a barrel. This design allows for enhanced mixing, kneading, and shearing capabilities, making it ideal for processing viscous and semi-solid food materials. The screws themselves are cone-shaped, with the diameter gradually increasing or decreasing along their length, which helps in achieving a more uniform material distribution and better control over the extrusion process.
One of the key advantages of the conical twin screw extruder is its ability to handle a wide range of materials, including polymers used in food packaging. The extruder's screws and barrel are precision-engineered to ensure that the material is uniformly processed, leading to a higher quality final product. This is particularly important in the food industry, where product quality and safety are paramount.
Furthermore, the conical twin screw extruder offers a high degree of flexibility and versatility. The screws can be configured in various arrangements, such as parallel, converging, or diverging, to suit different processing needs. This allows for a wide range of applications, including the production of films, sheets, and other packaging materials used in the food industry.
In addition to its exceptional processing capabilities, the conical twin screw extruder is also known for its energy efficiency and low maintenance requirements. The precision engineering of the screws and barrel minimizes friction and wear, leading to longer equipment lifespan and reduced operational costs.
In conclusion, the conical twin screw extruder is a highly efficient and versatile tool for processing food materials, particularly polymers used in food packaging. Its unique design, precision engineering, and flexibility make it an indispensable asset in the food manufacturing industry. In the next section, we will delve deeper into the structure and working principle of conical twin screw extruders, providing a more comprehensive understanding of how this remarkable piece of equipment operates and contributes to the success of food manufacturing operations.
Conical Twin Screw Extruder Basics
In the dynamic world of industrial food machinery, the conical twin screw extruder stands as a pillar of innovation and efficiency. Today, let's explore the fundamentals of the conical twin screw extruder, focusing on its design, operational principles, and the reasons why it is a preferred choice for many food manufacturers.
Design and Construction |
The conical twin screw extruder is named for its distinctive feature: two intermeshing screws that taper towards the discharge end. This design allows for more efficient mixing, kneading, and conveying of materials as they travel through the extruder's barrel. The screws are precision-engineered from high-strength materials to withstand the rigorous conditions of continuous operation. The barrel of the conical twin screw extruder is typically made from corrosion-resistant stainless steel, ensuring that the material being processed remains free from contamination. The screws and barrel are carefully aligned to maintain a precise gap, which is critical for achieving a consistent product quality. |
Operational Principles |
The operational principle of the conical twin screw extruder is based on the combined action of the two screws. As they rotate in opposite directions, they create a series of shear and compression zones within the barrel. This dynamic action facilitates the mixing, kneading, and heating of the material, preparing it for extrusion through the die at the end of the barrel. The screws are designed to convey the material forward while simultaneously distributing it evenly across the barrel's cross-section. This ensures that all parts of the material are exposed to the same processing conditions, resulting in a homogeneous product with consistent properties. |
Advantages in Polymer Manufacturing |
In the context of polymer manufacturing, particularly for food packaging, the conical twin screw extruder offers several advantages. Its ability to handle a wide range of materials, including high-viscosity polymers, makes it versatile and adaptable to different production requirements. Moreover, the precise control over processing conditions, such as temperature and shear rate, enables manufacturers to tailor the properties of the extruded material to meet specific application needs. This includes achieving the desired texture, flexibility, and barrier properties, which are crucial for food packaging. Additionally, the conical twin screw extruder is known for its high throughput and continuous operation capabilities. This makes it an ideal choice for large-scale production environments where efficiency and productivity are paramount. |
Methods for Measuring and Analyzing Extruder Performance
In the realm of industrial food machinery, the performance of conical twin screw extruders in polymer manufacturing is a subject of paramount importance. As an authority in the field, I have extensive experience in assessing the efficiency, reliability, and output quality of these machines. Today, we will explore the methods employed to measure and analyze the performance of conical twin screw extruders, ensuring that the insights provided are both accurate and actionable.
Direct Measurement Techniques
One of the most straightforward methods for evaluating extruder performance involves direct measurement of key parameters. These include throughput, torque, and temperature.
1.Throughput: Measuring the rate of material flow through the extruder provides a direct indication of its processing capacity. This can be achieved using weighing scales or flow meters positioned at the extruder's outlet.
2.Torque: Monitoring the torque required to rotate the screws gives insights into the energy efficiency and mechanical load of the extruder. High torque values may indicate excessive friction or wear, necessitating maintenance or adjustment.
3.Temperature: Controlling and monitoring the temperature within the extruder barrel is crucial for achieving optimal processing conditions. Thermocouples or infrared sensors can be used to measure the temperature at various points along the barrel, ensuring that the material is heated to the desired level without degradation.
Indirect Measurement Techniques
While direct measurement techniques provide valuable data, indirect methods can also offer insights into extruder performance. These methods often involve analyzing the properties of the extruded material or the extruder's operational behavior over time.
1.Material Properties: Evaluating the physical and chemical properties of the extruded material can reveal the effectiveness of the processing conditions. Tests such as tensile strength, elongation at break, and melt flow index can be conducted to assess the material's quality.
2.Operational Stability: Monitoring the extruder's operational stability over extended periods can provide insights into its durability and reliability. This includes tracking the machine's vibration levels, noise emissions, and energy consumption.
Data Analysis and Interpretation
Once the measurement data is collected, it is essential to analyze and interpret it correctly. This involves comparing the measured values against predefined benchmarks or standards, which may be based on the extruder's design specifications, industry norms, or previous performance data.
Advanced data analysis tools, such as statistical software or machine learning algorithms, can be employed to identify trends, correlations, and anomalies in the data. This enables manufacturers to pinpoint areas for improvement, optimize processing conditions, and predict potential failures before they occur.
Factors Affecting Extruder Performance
In the intricate world of industrial food machinery, the conical twin screw extruder stands as a testament to engineering ingenuity, particularly in the realm of polymer manufacturing.Today, we delve into the critical factors that affect the performance of conical twin screw extruders, ensuring that our discussion is both comprehensive and authoritative.
1.Material Characteristics
One of the fundamental factors affecting extruder performance is the characteristics of the material being processed. The rheological properties of polymers, such as viscosity, melt elasticity, and shear sensitivity, play a pivotal role in determining the extruder's ability to process them effectively.
For instance, highly viscous materials may require more energy to push through the extruder, leading to increased torque and wear on the screws. Conversely, materials with low melt strength may be prone to sagging or deformation during extrusion, necessitating careful control of processing temperatures and pressures.
2.Extruder Design
The design of the conical twin screw extruder itself is another critical factor. The geometry of the screws, the barrel configuration, and the cooling system all contribute to the machine's performance.
Conical screws, characterized by their tapering diameter, offer several advantages over cylindrical screws. They provide better mixing and kneading of materials, enabling more uniform distribution of additives and fillers. Additionally, the varying screw diameters create different shear zones, which can be tailored to optimize processing conditions for specific materials.
The barrel configuration, including its length-to-diameter ratio, affects the residence time of the material within the extruder. A longer barrel allows for more thorough mixing and heating, while a shorter one may be more suitable for high-throughput applications.
3.Processing Conditions
The processing conditions under which the extruder operates also have a significant impact on its performance. Temperature, pressure, and screw speed are among the most critical parameters.
Temperature control is essential for ensuring that the material reaches the appropriate viscosity for extrusion. Too high a temperature can cause material degradation, while too low a temperature may result in incomplete melting or excessive shear heating.
Pressure within the extruder barrel affects the flow behavior of the material. High pressures can enhance mixing and dispersion, but they also increase the mechanical load on the screws and barrel.
Screw speed determines the rate of material shear and mixing within the extruder. Optimal screw speeds vary depending on the material being processed and the desired output characteristics.
4.Maintenance and Wear
Finally, the maintenance status and wear on the extruder components play a crucial role in its performance. Wear on the screws and barrel walls can lead to increased friction, reduced mixing efficiency, and material degradation.
Regular inspections and maintenance, such as replacing worn screws and barrel liners, can help maintain extruder performance over time. Additionally, the use of high-quality materials and precision manufacturing techniques can extend the lifespan of extruder components, reducing the frequency of maintenance and downtime.
Future Trends and Developments
In the ever-evolving landscape of industrial food machinery, the conical twin screw extruder has emerged as a cornerstone in polymer manufacturing. This section explores the exciting innovations and emerging technologies that are poised to revolutionize the performance of conical twin screw extruders in polymer manufacturing.
Enhanced Material Handling Capabilities |
One of the most promising trends in conical twin screw extruder technology is the development of enhanced material handling capabilities. Manufacturers are continuously refining the design of screws and barrels to better accommodate a wider range of materials, including those with high viscosity, low melt strength, or sensitive to shear and heat. For instance, the adoption of advanced screw geometries, such as modular and interchangeable screw elements, allows for greater flexibility in processing different materials. These elements can be tailored to optimize mixing, kneading, and shearing actions, ensuring that the extruder performs optimally across a diverse range of applications. |
Integration of Advanced Sensors and Controls |
The integration of advanced sensors and control systems is another significant trend in conical twin screw extruder technology. These systems provide real-time monitoring and control of critical processing parameters, such as temperature, pressure, and screw speed. By leveraging the power of IoT and machine learning algorithms, manufacturers can optimize extruder performance in real-time, reducing waste, and improving product quality. Additionally, predictive maintenance capabilities can help identify potential issues before they escalate, minimizing downtime and maintenance costs. |
Sustainability and Energy Efficiency |
In response to the global call for sustainability, manufacturers are focusing on developing conical twin screw extruders that are more energy-efficient and environmentally friendly. This includes the adoption of energy-saving technologies, such as variable frequency drives (VFDs) and heat recovery systems. VFDs enable precise control of screw speed and torque, optimizing energy consumption based on the specific requirements of the processing task. Heat recovery systems capture and reuse waste heat generated during extrusion, reducing the overall energy footprint of the process. |
Automation and Digitalization |
The trend towards automation and digitalization is also transforming the world of conical twin screw extruders. Manufacturers are increasingly adopting robotics, automated feeding and conveying systems, and digital twins to streamline production processes. Digital twins, for example, are virtual representations of the extruder and its associated processes. They allow manufacturers to simulate and optimize production scenarios before they are implemented in the real world, reducing trial and error and accelerating product development cycles. |
Reference
The following are five authoritative foreign literature websites in the field of Industrial food machinery:
1. Food Engineering Magazine
Website: https://www.foodengineeringmag.com/
2.Food Processing Magazine
Website: https://www.foodprocessing.com/
3.Journal of Food Engineering
Website:https://www.journals.elsevier.com/journal-of-food-engineering
4. Food Manufacturing Magazine
Website:https://www.foodmanufacturing.com/
5. International Journal of Food Science & Technology
Website:https://onlinelibrary.wiley.com/