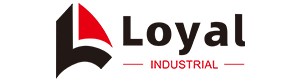
- Shandong Loyal Industrial Co.,Ltd.
- Macaroni Production Machine Instant Noodle Machine Biscuit Making Machine

Home> Company News> Everything You Need To Know About Snack Food Production Line

Everything You Need To Know About Snack Food Production Line
2025-02-08 15:23:52Introduction
Overview of Snack Food Production Lines:
Snack food production lines are complex systems designed to process raw ingredients into a variety of ready-to-eat products, such as chips, crisps, nuts, and other packaged snacks. These production lines typically consist of multiple interconnected machines, including mixers, fryers, ovens, and packaging units, all working together to create consistent, high-quality snack foods. Over the years, snack food production lines have evolved to meet growing consumer demand, incorporating advancements in automation, energy efficiency, and quality control.
Importance of Energy Efficiency and Automation in Modern Factories
In today’s competitive market, modern factories must prioritize both efficiency and sustainability to maintain a profitable edge. The importance of energy efficiency cannot be overstated, as the food manufacturing industry is among the most energy-intensive sectors. Reducing energy consumption not only lowers operational costs but also reduces the environmental footprint of production facilities. Automation plays a critical role in achieving these goals, as it allows for precise control over production processes, minimizes waste, and ensures consistent product quality, all while reducing the need for manual labor.
Brief Introduction to the Fully Automatic Snack Food Production Line
A fully automatic snack food production line integrates cutting-edge technology to automate the entire manufacturing process, from ingredient mixing to packaging. These advanced systems are designed to increase production speed, enhance product consistency, and reduce the risk of human error. Additionally, they include energy-saving features that optimize machine operation and minimize downtime. As the demand for snack foods continues to rise globally, factories that adopt fully automated and energy-efficient production lines position themselves for long-term success by increasing throughput and decreasing energy consumption.
Key Components of an Energy-Efficient Snack Food Production Line
Overview of Critical Machinery
A snack food production line consists of several key machines, each playing a crucial role in converting raw ingredients into finished products. These machines include:
Mixers: Used to combine ingredients uniformly, ensuring that the texture and flavor are consistent throughout the final product. In energy-efficient systems, mixers are designed to operate at optimal speeds, reducing energy consumption while still achieving the necessary consistency.
Extruders: These are responsible for shaping and cooking snack foods by forcing ingredients through a die under high pressure and temperature. Advanced extruders in energy-efficient lines use precise temperature and pressure controls, minimizing energy waste.
Ovens: Ovens cook snack foods by applying heat. Modern snack food production lines utilize energy-efficient fryers with high thermal efficiency, reducing the amount of energy required to achieve the desired cooking results.
Packaging Machines: Once snacks are produced, they must be packaged for sale. Automated packaging machines ensure that snacks are packed quickly and accurately. Energy-efficient packaging systems use less power by optimizing the speed and operational time of packaging processes.
Role of Energy-Saving Technologies in Each Component
Each machine within the snack food production line is designed with energy-saving technologies to optimize energy use and reduce overall consumption. For instance:
Energy-Efficient Motors: The use of high-efficiency motors ensures that the production line operates with minimal electrical consumption, particularly in machines like mixers and conveyors.
Automation Features That Enhance Efficiency
Automation is a key driver of efficiency in modern snack food production lines. Key automation features include:
Smart Control Systems: These systems allow for real-time monitoring and adjustment of production parameters such as temperature, pressure, and speed. By constantly optimizing these parameters, energy consumption is minimized while maintaining high production quality.
Benefits of Fully Automatic Snack Food Production Lines
Increased Production Capacity
One of the primary advantages of a fully automatic snack food production line is the significant boost in production capacity. Automation allows for continuous, high-speed processing, which is essential to meet the growing global demand for snack foods. With minimal downtime and efficient material handling, automated systems can process large volumes of ingredients and produce snacks at a much faster rate than manual production methods. This increased capacity enables factories to scale up operations, cater to larger markets, and achieve higher output without compromising on product quality.
Consistent Product Quality
Maintaining consistent product quality is crucial in the food industry, and fully automated snack food production lines are designed to ensure this with precision. Automation eliminates the variability that comes with manual labor, ensuring that every batch of snacks is produced under identical conditions. Key factors such as ingredient mixing, cooking times, and packaging are monitored and controlled automatically, resulting in uniform textures, flavors, and appearances. This consistency not only meets consumer expectations but also reduces the likelihood of waste due to substandard products.
Reduced Labor Costs and Human Error
By automating the production process, factories can significantly reduce their reliance on manual labor. This reduction in labor costs is one of the main drivers of profitability for modern snack food factories. Automation also decreases the likelihood of human error, which can lead to defects in the product, inefficient use of materials, or safety risks. Automated systems handle repetitive tasks with high precision, ensuring that the production process runs smoothly and that products are consistently high-quality.
Improved Safety and Hygiene Standards
The implementation of automation in snack food production lines also enhances food safety and hygiene. Automated systems are designed with strict compliance to health and safety regulations, ensuring that the handling of ingredients, cooking processes, and packaging are all done under sanitary conditions. For example, fully automated systems reduce the need for direct human interaction with raw ingredients, minimizing the risk of contamination. Additionally, the precise control over cooking and packaging processes ensures that each product meets the required food safety standards, reducing the risk of recalls or foodborne illness outbreaks.
Energy Efficiency Features in Snack Food Production Lines
Energy-Saving Techniques Used in Machinery
In the real-world application of snack food production lines, manufacturers have adopted several practical techniques to improve energy efficiency without relying on cutting-edge technologies that may be costly or difficult to implement. These techniques focus on improving the energy consumption of traditional machinery and enhancing operational efficiency.
Optimized Machine Design: Many snack food production lines feature equipment that is designed with energy efficiency in mind. For example, efficient motors are commonly used in mixers, extruders, and conveyors to ensure that power consumption is kept to a minimum while maintaining the necessary output levels. These motors are often combined with geared drives that optimize performance during various stages of production.
Insulation and Heat Retention: Ovens used in snack food production require significant amounts of energy to reach and maintain the necessary cooking temperatures. To mitigate energy loss, many manufacturers install high-quality insulation around these machines. This insulation helps retain heat within the cooking area, reducing the need for constant energy input to maintain temperature, thus improving energy efficiency.
Use of Renewable Energy Sources in Production
While renewable energy sources are still not widespread across all snack food production lines, some factories have started integrating these systems to improve sustainability and reduce reliance on grid power.
Innovations in Heat Recovery and Waste Management
In many snack food production facilities, heat recovery and waste management are critical to improving overall energy efficiency.
Heat Recovery in Fryers and Ovens: Fryers and ovens are some of the most energy-intensive equipment in a snack food production line. Many factories have incorporated simple heat recovery systems, which capture excess heat generated during the frying or baking process and reuse it to preheat air or ingredients. By recovering heat, these systems reduce the energy required to heat up equipment for subsequent batches, leading to lower overall energy consumption.
Efficient Waste Management: Effective waste management not only helps reduce operational costs but also improves energy efficiency. Some snack food production lines adopt techniques such as compacting food waste or sending it to anaerobic digesters, where organic waste is broken down to produce biogas. This biogas can be used to generate energy for the factory, providing a renewable energy source while minimizing waste disposal costs.
Role of Smart Sensors and Monitoring Systems in Reducing Energy Consumption
While not always as advanced as the most cutting-edge smart technologies, some snack food production lines do make use of basic monitoring systems to optimize energy use.
Basic Monitoring and Control Systems: Production lines often use basic sensors to monitor temperature, humidity, and pressure during key stages of production, such as frying or baking. By ensuring that these conditions are always within optimal ranges, manufacturers can avoid overuse of energy. For example, temperature sensors in fryers can prevent the system from heating beyond the necessary point, reducing excess energy consumption.
Automated Process Control: Some snack food lines incorporate simple automated control systems that adjust production parameters based on real-time feedback. For instance, conveyor speeds and cooking temperatures may be adjusted automatically based on the quantity of product being processed, preventing overuse of energy and improving overall efficiency.
How Automation Enhances Efficiency in Snack Food Production
Streamlined Production Process from Start to Finish
Automation plays a crucial role in streamlining snack food production from the initial stages of ingredient preparation to the final packaging. By replacing manual labor with automated systems, production lines can operate more smoothly and efficiently. In an automated production line, machines are programmed to handle repetitive tasks such as mixing, extruding, frying, and packaging, significantly reducing human intervention.
For instance, automated mixing machines ensure that ingredients are combined uniformly and consistently, improving both product quality and production speed. Automated extruders create uniform shapes and textures, ensuring that each snack meets the required specifications. In the frying or baking stages, automated systems monitor cooking times and temperatures, ensuring that the snacks are processed with minimal energy use and maintaining consistent quality.
Overall, the entire production process becomes more cohesive, reducing bottlenecks and eliminating delays that may arise from human input or manual errors.
Real-Time Monitoring and Adjustments to Optimize Production
Automation systems often include real-time monitoring features that allow for continuous observation of production parameters such as temperature, speed, and pressure. These systems are designed to detect deviations in real-time and make immediate adjustments to optimize efficiency. For example, if an extruder begins to overheat or a fryer uses too much energy, the system will adjust parameters automatically to restore optimal conditions.
Additionally, data-driven insights from automated systems enable operators to identify potential inefficiencies and areas for improvement. Automated sensors collect real-time data on energy consumption, production rates, and product quality, helping factory managers pinpoint opportunities for reducing waste or improving processes. By addressing inefficiencies as they arise, manufacturers can maximize throughput while minimizing energy consumption and material waste.
Integration of Data-Driven Insights for Performance Improvement
The use of data analytics in automated snack food production lines enables continuous performance improvement. By collecting large volumes of data from different stages of production, these systems can identify trends, patterns, and areas for optimization that may not be immediately visible to human operators.
Predictive Analytics: By analyzing historical data and real-time production metrics, automated systems can predict when machinery is likely to need maintenance or when energy consumption is likely to spike. Predictive analytics help minimize unexpected breakdowns, reduce downtime, and optimize energy usage.
Automated systems empower snack food manufacturers to continuously improve production performance, making adjustments in real time to meet demand while maintaining energy efficiency and product quality.
Conclusion
Summary of the Advantages of an Energy-Efficient, Fully Automatic Snack Food Production Line
An energy-efficient, fully automatic snack food production line offers numerous benefits to modern food manufacturers, significantly enhancing both operational efficiency and sustainability. Through the integration of automated systems, manufacturers can achieve higher production capacity, consistent product quality, and reduced labor costs, while minimizing energy consumption and waste.
Energy-saving technologies, such as optimized motor systems, heat recovery, and basic automation, provide both short-term and long-term cost savings, while ensuring that snack food production is both environmentally responsible and economically viable. By replacing manual labor with automation, snack food producers can ensure a more streamlined and reliable production process, leading to higher output and lower chances of error.
Future Trends and Innovations in Snack Food Manufacturing
Looking to the future, the snack food industry is expected to see continued advancements in energy-efficient technologies and automation. As manufacturing processes become even more sophisticated, the use of artificial intelligence (AI) and machine learning to predict and optimize production conditions is likely to expand. These technologies will enable real-time decision-making that enhances operational efficiency, improves sustainability, and reduces production costs even further.
Moreover, there will likely be an increasing focus on integrating sustainable sourcing practices and renewable energy systems, as consumers and businesses alike demand more environmentally friendly production methods. Innovations in biodegradable packaging and water-efficient processes will further contribute to the industry's sustainability goals.
Final Thoughts on Why Modern Factories Should Invest in This Technology
Investing in an energy-efficient, fully automatic snack food production line is no longer a luxury for modern factories—it is a necessity for staying competitive in today’s market. As consumer demand for high-quality, affordable, and sustainably produced snack foods continues to rise, factories must adopt technologies that improve both productivity and environmental stewardship.
Not only does automation and energy efficiency lead to cost savings, but it also ensures that snack food manufacturers are prepared for future challenges, such as stricter environmental regulations and fluctuating energy prices. By embracing these technologies, manufacturers can create more resilient, profitable, and sustainable operations, positioning themselves as leaders in a rapidly evolving industry.
Reference
The following are five authoritative foreign literature websites in the field of Industrial food machinery:
1. Food Engineering Magazine
Website: https://www.foodengineeringmag.com/
2.Food Processing Magazine
Website: https://www.foodprocessing.com/
3.Journal of Food Engineering
Website:https://www.journals.elsevier.com/journal-of-food-engineering
4. Food Manufacturing Magazine
Website:https://www.foodmanufacturing.com/
5. International Journal of Food Science & Technology
Website:https://onlinelibrary.wiley.com/