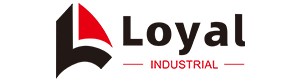
- Shandong Loyal Industrial Co.,Ltd.
- Macaroni Production Machine Instant Noodle Machine Biscuit Making Machine

Home> Company News> Everything you Need to Know About Fish Food Production Line

Everything you Need to Know About Fish Food Production Line
2024-04-23 16:27:42Introduction to Fish Food Production Machinery
Fish food production machinery plays a crucial role in the efficient and hygienic manufacturing of fish feed. These specialized machines are designed to handle various stages of the production process, from raw material preparation to packaging. Understanding the different types of machinery involved in fish food production is essential for optimizing productivity and ensuring product quality.
One of the key pieces of equipment in a fish food production line is the extruder. Extruders are versatile machines capable of processing a wide range of ingredients into various shapes and sizes of fish feed pellets. They work by forcing a mixture of ingredients through a die under high pressure and temperature, resulting in the formation of pellets with consistent texture and nutritional content. Extruders are essential for achieving uniformity in fish feed production and can accommodate different formulations to meet the specific dietary requirements of different fish species.
In addition to extruders, fish food production lines typically include equipment for ingredient preparation, mixing, and drying. Ingredient preparation equipment such as grinders and crushers are used to process raw materials such as grains, fish meal, and additives into a uniform particle size suitable for extrusion. Mixers are then employed to blend the ingredients together and ensure even distribution of nutrients throughout the feed mixture. Finally, dryers are used to reduce the moisture content of the extruded pellets to enhance their shelf life and stability.
Components and Functions of Fish Food Processing Equipment
Fish food processing equipment comprises various components, each with specific functions aimed at optimizing the production process and ensuring product quality. Understanding the roles of these components is essential for effective operation and maintenance of fish food processing equipment.
One of the primary components of fish food processing equipment is the extruder barrel. The extruder barrel is a cylindrical chamber through which the feed mixture passes during extrusion. It is equipped with heating elements and cooling jackets to precisely control the temperature of the feed mixture as it undergoes extrusion. The barrel's design and configuration play a crucial role in determining the texture, size, and nutritional quality of the extruded pellets.
Another important component of fish food processing equipment is the screw or auger. The screw is responsible for conveying the feed mixture through the extruder barrel and applying pressure to the mixture to facilitate extrusion. It is typically equipped with a series of flights or paddles that help move the feed mixture along the barrel and ensure uniform processing. The design and geometry of the screw can be customized to achieve specific processing objectives, such as controlling the density and shape of the extruded pellets.
Furthermore, fish food processing equipment often includes control systems and sensors to monitor and adjust process parameters in real-time. These systems enable operators to maintain precise control over factors such as temperature, moisture content, and pressure, ensuring consistent product quality and minimizing waste. Additionally, safety features such as emergency stop buttons and interlocks are incorporated into the equipment to protect operators and prevent accidents during operation.
Benefits of Automated Fish Food Production Systems
Automated fish food production systems offer numerous advantages over traditional manual or semi-automated processes, including increased efficiency, consistency, and product quality. By leveraging advanced technology and robotics, automated systems streamline the production process and minimize human intervention, leading to improved productivity and profitability.
One of the primary benefits of automated fish food production systems is their ability to reduce labor costs and increase production capacity. By automating repetitive tasks such as ingredient weighing, mixing, extrusion, and packaging, manufacturers can significantly reduce the need for manual labor and increase the throughput of the production line. This allows for faster production cycles and higher output volumes, ultimately leading to greater profitability and competitiveness in the market.
Additionally, automated fish food production systems offer greater consistency and control over product quality. By precisely controlling process parameters such as temperature, moisture content, and mixing ratios, automated systems ensure uniformity in the texture, size, and nutritional composition of the extruded pellets. This results in a more consistent product that meets the stringent quality standards demanded by consumers and regulatory agencies.
Automated systems enable manufacturers to enhance food safety and traceability throughout the production process. By incorporating advanced sensors and monitoring technologies, automated systems can detect and eliminate potential hazards such as foreign objects, microbial contamination, and equipment malfunctions in real-time. This helps ensure the safety and integrity of the final product and provides greater transparency to consumers regarding the origin and quality of the fish feed.
Key Considerations for Selecting Fish Food Machinery
When selecting fish food machinery for your production line, several key considerations should be taken into account to ensure optimal performance, efficiency, and product quality. Two reputable manufacturers in the industry, LOYAL and American Extrusion, offer a range of machines suitable for fish food production. Let's compare their machines in various aspects:
Aspect |
LOYAL Machinery |
American Extrusion Machinery |
Quality and Reliability |
Known for durable, reliable machines with a long lifespan. |
Renowned for high-quality, robust machinery designed for heavy-duty use. |
Technology and Innovation |
Incorporates advanced technology and innovative features to enhance performance and efficiency. |
Offers cutting-edge technology and innovative solutions to meet evolving industry demands. |
Customization Options |
Provides customizable options to tailor machines to specific production needs and requirements. |
Offers a range of customization options to accommodate various production scenarios and product specifications. |
Customer Support |
Offers comprehensive customer support services, including technical assistance, training, and maintenance programs. |
Provides excellent customer support, with responsive service teams and timely assistance for troubleshooting and maintenance. |
Types of Fish Food Extruders and Their Applications
Fish food extruders play a crucial role in the production of high-quality fish feed, offering versatility, efficiency, and consistency in processing. Several types of extruders are commonly used in the fish food production industry, each with its unique features and applications.
1. Single-Screw Extruders: Single-screw extruders are the most common type of extruder used in fish food production. They feature a single rotating screw that pushes the raw material through a barrel, where it is heated and compressed before being extruded through a die. Single-screw extruders are versatile and suitable for a wide range of fish feed formulations, including floating and sinking pellets.
2. Twin-Screw Extruders: Twin-screw extruders consist of two intermeshing screws that work together to process the raw material. These extruders offer greater flexibility and control over the extrusion process, allowing for precise adjustment of parameters such as temperature, pressure, and screw speed. Twin-screw extruders are ideal for producing high-quality fish feed with enhanced digestibility and nutritional value.
3. Co-Extruders: Co-extruders are specialized extrusion machines that enable the encapsulation of liquid or viscous ingredients within a solid extruded product. In fish food production, co-extruders are used to create multilayered pellets with a core of concentrated nutrients surrounded by a protective outer layer. This technology allows for the incorporation of sensitive ingredients such as vitamins, minerals, and additives without compromising product integrity.
4. High-Shear Extruders: High-shear extruders are designed to process high-moisture materials and produce dense, compact pellets with improved texture and durability. These extruders use high-pressure and high-temperature conditions to cook and gelatinize the raw material, resulting in a uniform and stable finished product. High-shear extruders are commonly used in the production of sinking fish feed pellets for bottom-dwelling species.
Importance of Mixing and Blending Equipment in Fish Food Production
Mixing and blending equipment play a crucial role in the fish food production line, ensuring uniformity, consistency, and quality in the final product. These equipment are essential for achieving proper ingredient distribution and homogeneity throughout the fish food formulation.
Firstly, mixing equipment is used to combine various ingredients in the fish food formulation, including proteins, carbohydrates, vitamins, minerals, and additives. Proper mixing is vital to ensure that each batch of fish food contains the correct proportions of ingredients, which is essential for meeting nutritional requirements and maintaining product consistency. Additionally, mixing helps distribute essential nutrients evenly throughout the food to ensure uniformity and balance in every bite consumed by aquatic animals.
Blending equipment is utilized to achieve a uniform mixture of ingredients and create a homogeneous fish food blend. Blending ensures that all ingredients are thoroughly integrated and distributed throughout the mixture, preventing segregation or separation of components. This is critical for ensuring that the nutritional content of the fish food is consistent across batches and that every portion provides the necessary nutrients for fish health and growth.
Mixing and blending equipment facilitate the incorporation of liquid additives and flavorings into the fish food formulation. These equipment enable precise control over the addition of liquids, ensuring accurate dosing and uniform distribution of flavors, colors, and nutritional supplements. This enhances the palatability and appeal of the fish food, encouraging fish consumption and promoting growth and development.
Quality Control Measures in Fish Food Processing Lines
Firstly, raw material inspection is conducted to assess the quality and suitability of incoming ingredients for fish food production. This includes checking for freshness, purity, and compliance with specifications such as moisture content, protein levels, and absence of contaminants. Only high-quality ingredients that meet established standards are approved for use in the production process.
Stringent hygiene and sanitation practices are implemented in fish food processing facilities to prevent contamination and ensure food safety. This includes regular cleaning and sanitization of equipment, surfaces, and processing areas to eliminate bacteria, pathogens, and other potential hazards. Personnel are trained on proper hygiene protocols and wear appropriate protective gear to minimize the risk of cross-contamination.
Quality control checkpoints are established at key stages of the processing line to monitor product quality and consistency. This includes visual inspections, sensory evaluations, and laboratory testing to assess parameters such as texture, color, aroma, and nutritional content. Any deviations from specifications are promptly identified and addressed to maintain product integrity and meet customer expectations.
Traceability systems are implemented to track the journey of each batch of fish food from raw material sourcing to finished product distribution. This enables swift identification and recall of products in the event of quality issues or safety concerns, ensuring timely corrective actions and minimizing risk to consumers.
Energy Efficiency in Fish Food Processing Equipment
Energy efficiency is a key consideration in the design, operation, and maintenance of fish food processing equipment to minimize energy consumption, reduce costs, and mitigate environmental impact. Several practices and technologies can be employed to improve the energy efficiency of fish food processing equipment.
One energy-efficient practice in fish food processing equipment is the use of high-efficiency motors and variable frequency drives (VFDs). These components enable precise control of motor speed and power consumption, reducing energy waste during operation. Additionally, modern machinery designs incorporate features such as insulation and heat recovery systems to minimize energy losses and maximize efficiency.
Optimizing production processes and equipment layouts can help minimize energy consumption in fish food processing facilities. Streamlining workflows, reducing idle time, and optimizing equipment usage can all contribute to energy savings. Additionally, implementing energy management systems and monitoring tools can help track energy usage and identify opportunities for further efficiency improvements.
Utilizing renewable energy sources such as solar and wind power can help reduce reliance on fossil fuels and lower carbon emissions in fish food production. Installing solar panels or wind turbines onsite can generate clean, renewable energy to power machinery and equipment, reducing energy costs and environmental impact.
Safety Features and Regulations for Fish Food Machinery
Ensuring the safety of fish food machinery is paramount to protect workers, prevent accidents, and maintain product quality and hygiene. Manufacturers of fish food machinery must comply with stringent safety standards and regulations to ensure the safety of their equipment.
First and foremost, fish food machinery must adhere to industry-specific safety standards and regulations set forth by regulatory bodies such as the Occupational Safety and Health Administration (OSHA) and the Food and Drug Administration (FDA). These standards outline requirements for equipment design, installation, maintenance, and operation to ensure worker safety and product quality. Manufacturers are required to undergo rigorous testing and certification processes to ensure compliance with these standards.
One key aspect of safety compliance for fish food machinery is the incorporation of guards and enclosures to prevent access to moving parts and hazardous areas. Guards are designed to shield operators from rotating blades, conveyor belts, and other potential hazards, while enclosures provide a barrier to contain spills and debris. Additionally, emergency stop buttons and safety interlocks are installed on equipment to immediately halt operations in the event of an emergency or malfunction, allowing workers to quickly shut down machinery and prevent accidents or injuries.
Regular maintenance and inspection of fish food machinery are essential to identify and address potential safety hazards. Manufacturers and operators must follow maintenance schedules and conduct thorough inspections to ensure that equipment is functioning properly and meets safety standards. By implementing robust safety features and adhering to regulations, manufacturers can create a safe working environment and minimize the risk of accidents or injuries in fish food production facilities.
FAQs: Frequently Asked Questions about Fish Food Production Line
1. What is a fish food production line?
A fish food production line is a series of interconnected machinery and equipment designed to process raw ingredients into finished fish food products. It typically includes various stages such as ingredient mixing, extrusion, drying, cooling, and packaging.
2. What are the key components of a fish food production line?
The key components of a fish food production line include extruders, mixers, dryers, conveyors, coolers, and packaging machines. Each component plays a crucial role in the production process, from blending ingredients to packaging the final product.
3. How does a fish food production line work?
In a fish food production line, raw ingredients such as fish meal, grains, vitamins, and minerals are first mixed together in precise proportions. The mixture is then fed into an extruder, where it is cooked under high pressure and temperature to form the desired shape and texture. The extruded product is then dried, cooled, and packaged for distribution.
4. What types of fish food can be produced using a fish food production line?
A fish food production line can be used to produce a wide range of fish food products, including floating and sinking pellets, flakes, granules, and sticks. These products can be formulated to meet the nutritional requirements of various species of fish, such as freshwater and saltwater fish, as well as carnivorous and herbivorous fish.
References
1. Petfoodindustry.com: https://www.petfoodindustry.com/
2. Petfoodprocessing.net: https://www.petfoodprocessing.net/
3. Foodengineeringmag.com: https://www.foodengineeringmag.com/
4. Foodprocessing.com: https://www.foodprocessing.com/
5. Foodtechconnect.com: https://foodtechconnect.com/