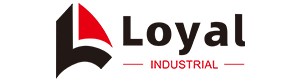
- Shandong Loyal Industrial Co.,Ltd.
- Macaroni Production Machine Instant Noodle Machine Biscuit Making Machine

Home> Company News> The Ultimate Guide to Grain Machines in 2024

The Ultimate Guide to Grain Machines in 2024
2024-04-24 15:21:25Introduction to Grain Machinery
Grain machinery stands at the forefront of industrial food processing, revolutionizing the way grains are handled and processed in 2024. These sophisticated machines are instrumental in meeting the escalating demands of consumers and ensuring the efficiency and quality of grain-based products.
Grain machines encompass a wide range of equipment designed to facilitate various stages of grain processing, from cleaning and sorting to milling and packaging. In today's food production landscape, the importance of grain machinery cannot be overstated, as it significantly streamlines operations, minimizes waste, and maintains product consistency.
In the following sections, we will delve deeper into the advanced features, applications, regulatory considerations, and future trends of grain machinery, providing comprehensive insights into its pivotal role in the food processing industry.
Advanced Features and Technology
In 2024, grain machines have undergone significant advancements, revolutionizing the landscape of industrial food processing. These cutting-edge technologies have propelled grain processing to new heights of efficiency and precision, meeting the ever-evolving demands of the food industry.
1. Automation and Integration:
Grain machines in 2024 boast advanced levels of automation and integration. Integrated control systems streamline the operation of various components, from cleaning and sorting to milling and packaging. Automated processes minimize manual intervention, enhancing efficiency and reducing labor costs.
2. AI and Machine Learning:
Artificial intelligence (AI) and machine learning algorithms are seamlessly integrated into modern cereals machines, enabling predictive maintenance and real-time optimization. These intelligent systems analyze vast amounts of data to anticipate equipment failures, optimize process parameters, and enhance overall performance.
3. Precision Engineering:
Precision is paramount in grain processing, and advanced cereals machines deliver unparalleled accuracy. High-precision sensors and actuators ensure precise control over variables such as moisture content, particle size, and temperature, resulting in consistent product quality and uniformity.
4. IoT Connectivity:
Internet of Things (IoT) connectivity allows grain machines to communicate and share data in real-time. This connectivity facilitates remote monitoring and control, enabling operators to oversee multiple machines from a centralized location. Additionally, IoT-enabled sensors provide valuable insights into equipment performance and maintenance needs.
5. Energy Efficiency:
Sustainability is a key focus in 2024, and grain machines are designed with energy efficiency in mind. Innovations such as regenerative braking, variable frequency drives, and heat recovery systems minimize energy consumption and reduce environmental impact without compromising productivity.
6. Customization and Flexibility:
Modern grain machines offer unprecedented levels of customization and flexibility to meet diverse processing requirements. Modular designs and adaptable configurations allow for seamless integration into existing production lines, while customizable settings accommodate variations in grain types and processing parameters.
Applications and Advantages in Food Production
Sure, here's a concise guide focusing on the applications and advantages of cereals machines in food production, presented in a tabular format:
Application |
Advantages |
Grain Cleaning |
- Removes impurities such as dirt, stones, and foreign particles - Improves overall grain quality and purity - Enhances food safety by eliminating contaminants |
Grain Milling |
- Converts grains into flour, meal, or powder form for further processing - Increases versatility in product development and recipe formulation - Enables customization of grain particle size for specific food applications |
Grain Mixing and Blending |
- Homogenizes multiple grain types and ingredients for uniform product texture - Facilitates consistent flavor distribution and nutritional balance - Enhances product stability and shelf life through proper ingredient dispersion |
Grain Cooking and Extrusion |
- Cooks grains to desired consistency and texture - Creates expanded cereals, snacks, and breakfast products with appealing texture - Increases digestibility and palatability of grain-based products |
Grain Drying and Cooling |
- Removes excess moisture from grains to prevent spoilage - Extends shelf life and maintains product quality - Prevents microbial growth and mycotoxin formation |
Grain Packaging and Labeling |
- Ensures hygienic and efficient packaging of finished grain products - Provides product information, branding, and regulatory compliance - Enhances product visibility and consumer appeal |
This table provides a comprehensive overview of the various applications of cereals machines in food production, along with their associated advantages.
Comparison between loyal and FEN companies
Comparison Factor |
Loyal |
FEN |
Product Range |
Specializes in bakery equipment, including mixers, ovens, and dough sheeters. Offers a wide range of options for small to large-scale bakeries. |
Offers a diverse selection of food processing equipment, such as slicers, dicers, and blenders, catering to various food production needs. |
Technology and Innovation |
Known for incorporating advanced technology, such as touchscreen interfaces and automated controls, to enhance efficiency and productivity. |
Emphasizes innovation in food processing machinery, integrating features like IoT connectivity and precision engineering for optimal performance. |
Customization Options |
Offers customizable solutions tailored to specific bakery requirements, allowing for adjustments in size, capacity, and functionality. |
Provides flexible customization options to meet the unique needs of food manufacturers, including customization of equipment configurations and production capacities. |
Quality and Durability |
Renowned for producing robust and durable equipment built to withstand the rigors of commercial bakery operations. |
Prioritizes quality craftsmanship and materials, ensuring reliable performance and longevity in demanding food processing environments. |
Customer Support |
Provides comprehensive customer support services, including technical assistance, training programs, and spare parts availability, to ensure smooth operation of equipment. |
Offers responsive customer support, including troubleshooting assistance, maintenance services, and rapid delivery of replacement parts, to minimize downtime for customers. |
Maintenance and Troubleshooting
Maintenance and troubleshooting are vital aspects of ensuring the optimal performance and longevity of cereals machines in 2024. Proper maintenance procedures and timely troubleshooting can prevent downtime and maximize efficiency in grain processing operations.
Maintenance Procedures
Regular maintenance is essential to keep cereals machines operating smoothly. Maintenance tasks include:
1. Cleaning: Regular cleaning of cereals machines prevents the buildup of debris and contaminants, ensuring hygienic processing conditions.
2. Lubrication: Lubricating moving parts of the machine reduces friction and wear, prolonging the lifespan of components.
3. Inspection: Routine inspections help identify potential issues early on, allowing for timely repairs and preventing costly breakdowns.
Troubleshooting Tips
Despite preventive measures, cereals machines may encounter issues during operation. Here are some troubleshooting tips:
1. Check for Blockages: Blockages in hoppers, conveyors, or chutes can disrupt the flow of grains. Clearing blockages promptly restores normal operation.
2. Inspect Sensors: Faulty sensors can lead to inaccurate readings or system malfunctions. Regularly check sensors for damage or calibration issues.
3. Monitor Power Supply: Fluctuations in power supply can cause cereals machines to malfunction. Ensure stable power sources and consider installing surge protectors.
Proactive Maintenance Schedule
Developing a proactive maintenance schedule is key to preventing unexpected breakdowns and optimizing cereals machine performance. Consider the following:
1. Regular Inspections: Conduct routine inspections at scheduled intervals to identify and address potential issues before they escalate.
2. Scheduled Maintenance Tasks: Implement a schedule for routine maintenance tasks, such as cleaning, lubrication, and parts replacement.
3. Documentation: Keep detailed records of maintenance activities, including dates, tasks performed, and any issues encountered, to track machine performance and identify trends over time.
In conclusion, prioritizing maintenance and troubleshooting procedures is essential for maximizing the efficiency and longevity of cereals machines in 2024. By adhering to proactive maintenance schedules and promptly addressing issues as they arise, food manufacturers can ensure uninterrupted operation and consistently high-quality grain processing.
Sustainability and Environmental Impact
Sustainability and environmental impact are critical considerations in the utilization of cereals machines within the food processing industry. As the demand for processed cereals continues to rise, it's imperative to assess the ecological footprint of these machines and implement strategies to minimize environmental harm while maximizing efficiency.
Cereals machines, comprising a range of equipment from sorting and cleaning to milling and packaging, have a significant environmental impact across their lifecycle. From energy consumption during operation to the generation of waste and emissions, every aspect of their usage must be scrutinized for sustainability.
Energy Efficiency and Resource Conservation
Efforts to improve the sustainability of cereals machines often focus on enhancing energy efficiency and conserving resources. This involves the adoption of advanced technologies such as energy-efficient motors, optimized processes, and automated systems that minimize energy waste and resource consumption.
Additionally, implementing measures to recover and reuse waste materials and byproducts generated during cereal processing can further reduce environmental impact. For example, utilizing waste heat from machinery for other processes or converting cereal byproducts into animal feed or biofuels can contribute to resource conservation and waste reduction.
Waste Management and Recycling Initiatives
Effective waste management practices are essential for mitigating the environmental impact of cereals machines. Implementing recycling initiatives for materials such as packaging, plastic, and metal components can help minimize landfill waste and reduce the depletion of natural resources.
Furthermore, exploring alternative packaging materials that are biodegradable or recyclable can significantly reduce the environmental footprint of cereal products. Investing in compostable packaging materials or utilizing innovative packaging designs that minimize material usage can contribute to sustainable packaging practices.
Carbon Emissions Reduction
Addressing carbon emissions associated with cereals machine operations is another crucial aspect of sustainability. Implementing measures to reduce energy consumption, such as optimizing machine settings, scheduling production runs during off-peak hours, and utilizing renewable energy sources, can help lower carbon emissions.
Moreover, exploring carbon offsetting initiatives, such as investing in reforestation projects or participating in carbon credit programs, can further mitigate the environmental impact of cereals machine operations. By offsetting carbon emissions generated during production processes, companies can contribute to global efforts to combat climate change.
In conclusion, ensuring the sustainability of cereals machines in 2024 requires a multifaceted approach that addresses energy efficiency, waste management, and carbon emissions reduction. By implementing strategies to minimize environmental impact while maximizing efficiency, the food processing industry can contribute to a more sustainable future.
Post-maintenance guide
After conducting maintenance on your cereals machine, it's crucial to follow a post-maintenance guide to ensure optimal performance and longevity of the equipment. Here are some key steps to take:
1. Inspect the Machine: After completing maintenance tasks, thoroughly inspect the cereals machine for any signs of damage or wear. Check all components, including belts, gears, and bearings, to ensure they are in good condition and properly aligned.
2. Test Run: Before resuming normal operations, perform a test run of the cereals machine. Monitor its performance closely, paying attention to any unusual noises, vibrations, or irregularities. This step allows you to identify any issues that may have been overlooked during maintenance.
3. Calibration: If your cereals machine requires calibration after maintenance, follow the manufacturer's instructions carefully. Calibration ensures that the machine operates with precision and accuracy, producing consistent results.
4. Documentation: Keep detailed records of the maintenance activities performed on the cereals machine. Note the date, tasks completed, and any parts replaced or repaired. This documentation serves as a valuable reference for future maintenance and troubleshooting.
5. Training: Ensure that operators and maintenance personnel are adequately trained on post-maintenance procedures. They should be familiar with the steps outlined in the post-maintenance guide and know how to respond to any issues that may arise.
6. Monitoring: After the cereals machine has been returned to service, continue to monitor its performance closely. Regularly inspect the equipment for signs of wear and tear, and address any maintenance issues promptly to prevent costly downtime.
By following this post-maintenance guide, you can maximize the efficiency and reliability of your cereals machine, prolonging its lifespan and ensuring consistent product quality. Remember, proper maintenance is key to achieving optimal performance and minimizing the risk of unexpected breakdowns.
Regulatory Compliance and Safety Standards
Regulatory compliance and adherence to safety standards are paramount in the operation of cereals machines in 2024. As industrial food processing continues to evolve, ensuring that grain machines meet regulatory requirements is essential for both consumer safety and industry reputation.
To begin with, regulatory bodies such as the FDA (Food and Drug Administration) and USDA (United States Department of Agriculture) set stringent guidelines for the design, construction, and operation of cereals machines. These guidelines encompass various aspects, including sanitation, hygiene, equipment materials, and processing conditions.
For instance, cereals machines must be constructed using food-grade materials that are safe for contact with food products. This ensures that there is no risk of contamination or chemical leaching during the processing of cereals. Additionally, machines should be designed to facilitate thorough cleaning and sanitation procedures to prevent the buildup of bacteria or other pathogens.
In terms of processing conditions, cereals machines must operate within specified parameters to ensure the safety and quality of the final product. This includes maintaining proper temperature, humidity, and processing times to minimize the risk of microbial growth or spoilage.
Furthermore, safety standards dictate the implementation of safeguards to protect operators and workers from potential hazards associated with cereals machines. This may include installing safety guards, emergency stop mechanisms, and providing adequate training on machine operation and safety protocols.
Compliance with regulatory requirements not only mitigates the risk of foodborne illnesses but also fosters consumer trust and confidence in the quality and safety of cereals products. Manufacturers must stay informed about updates to regulations and standards and proactively adapt their operations to remain compliant.
Reference
1. Food Processing:
Website: [Food Processing](https://www.foodprocessing.com/)
2. Food Engineering:
Website: [Food Engineering](https://www.foodengineeringmag.com/)
3. Process Industry Forum:
Website: [Process Industry Forum](https://www.processindustryforum.com/)
4. Food Manufacture:
Website: [Food Manufacture](https://www.foodmanufacture.co.uk/)