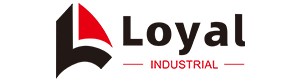
- Shandong Loyal Industrial Co.,Ltd.
- Macaroni Production Machine Instant Noodle Machine Biscuit Making Machine

Home> Company News> Everything you Need to Know About Animal Food Extruder

Everything you Need to Know About Animal Food Extruder
2024-04-25 16:36:33Introduction to Animal Food Extruders
Animal food extruders play a crucial role in the industrial processing of pet and livestock feed. These machines utilize extrusion technology to transform raw ingredients into nutritious and palatable food products for animals.
Extrusion is a versatile process that involves the mechanical and thermal treatment of ingredients under high pressure and temperature. This process not only improves the digestibility of the feed but also enhances its nutritional value and shelf life. Animal food extruders come in various sizes and configurations to cater to different production scales and requirements in the food industry.
History of Extrusion Technology
Extrusion technology, the foundation of modern animal food extruders, has a rich history dating back to the early 20th century. The origins of extrusion can be traced to the development of the first extrusion machine by Alexander Anderson in the United States in the 1930s. Initially used for the production of pasta, this early extruder laid the groundwork for further advancements in the field.
In the following decades, extrusion technology evolved rapidly, driven by innovations in materials science, engineering, and food processing. During World War II, extruders gained prominence in the production of military rations due to their ability to efficiently process a wide range of ingredients into compact and shelf-stable forms.
The post-war period witnessed a surge in the use of extrusion technology across various industries, including the food and agricultural sectors. In the 1950s and 1960s, researchers and engineers began exploring the potential of extrusion for the production of pet food and animal feed, leading to the development of specialized extruders tailored to these applications.
Throughout the latter half of the 20th century, advancements in extrusion technology continued apace, driven by factors such as increasing demand for processed foods, improvements in manufacturing techniques, and growing awareness of the nutritional needs of pets and livestock.
Principles of Animal Food Extrusion
Animal food extrusion is a complex process rooted in fundamental principles of engineering and food science. At its core, extrusion involves the transformation of raw ingredients into a cohesive and palatable product through the application of heat, pressure, and mechanical shear forces. This process relies on several key principles to achieve optimal results.
The principle of heat and pressure dynamics is central to animal food extrusion. As the raw ingredients are fed into the extruder, they pass through a barrel where they are subjected to increasing levels of heat and pressure. This combination softens the ingredients, causing them to become plasticized and malleable. The intense pressure within the extruder forces the softened material through a die, shaping it into the desired form.
Shear and mixing play crucial roles in the extrusion process, ensuring thorough blending of ingredients and uniform distribution of heat. Within the extruder barrel, rotating screws impart shear forces on the material, breaking down particles and promoting homogeneity. This mechanical action facilitates the dispersion of additives and ensures consistent product quality.
Another principle inherent to animal food extrusion is expansion and texturization. As the extruded product exits the die, it encounters a sudden drop in pressure, causing trapped moisture to vaporize and expand. This expansion results in the characteristic puffed texture of many extruded animal foods, enhancing palatability and digestibility.
Components of an Animal Food Extruder
An animal food extruder comprises several essential components, each playing a distinct role in the extrusion process. These components work in harmony to transform raw ingredients into high-quality finished products suitable for animal consumption.
The barrel serves as the primary processing chamber of the extruder, housing the screws and heating elements. It is typically constructed from durable stainless steel to withstand the high temperatures and pressures encountered during extrusion.
Screws are the mechanical drivers responsible for conveying, compressing, and shearing the raw material along the length of the barrel. They come in various designs and configurations, including single-screw and twin-screw arrangements, each tailored to specific processing requirements.
The die is a critical component that shapes the extruded product as it exits the extruder. It defines the final size, shape, and texture of the product and can be customized to produce a wide range of animal feed formulations, from pellets to textured shapes.
Heating elements, such as electric heaters or steam jackets, provide the necessary thermal energy to soften and plasticize the raw ingredients within the extruder barrel. Precise temperature control is essential to achieve optimal cooking and texturization of the final product.
Innovations in Animal Food Extrusion Technology
The field of animal food extrusion continues to evolve with ongoing advancements in technology and process optimization. Innovations in extrusion technology aim to enhance product quality, efficiency, and sustainability, driving the industry forward.
High-pressure extrusion techniques have emerged as a promising innovation in animal food processing. By subjecting the material to elevated pressures, manufacturers can achieve greater control over product texture, nutrient retention, and shelf stability. High-pressure extrusion also enables the production of novel feed formulations tailored to specific dietary requirements.
Advances in precision control systems have revolutionized the extrusion process, allowing for real-time monitoring and adjustment of key parameters such as temperature, pressure, and screw speed. These systems enhance process reliability, consistency, and product quality, while minimizing energy consumption and waste.
In response to growing environmental concerns, there has been a shift towards sustainable ingredients and processing methods in animal food extrusion. Manufacturers are exploring alternative protein sources, such as insect meal and plant-based proteins, to reduce reliance on traditional feedstocks. Additionally, efforts to optimize water and energy usage are driving the adoption of eco-friendly extrusion technologies, such as waterless extrusion and energy-efficient heating systems.
Comparative Analysis of Different Animal Food Extrusion
Aspect |
LOYAL Company Machine |
Coperion Company Machine |
Capacity |
Higher capacity |
Lower capacity |
Efficiency |
Moderate efficiency |
High efficiency |
Cost |
Lower initial cost |
Higher initial cost |
Maintenance |
Simpler maintenance |
More complex maintenance |
Durability |
Moderate durability |
High durability |
Flexibility |
Limited flexibility |
Greater flexibility |
This table provides a brief comparison between LOYAL Company's animal food extruder machine and Coperion Company's machine. LOYAL's machine offers higher capacity and simpler maintenance, making it a cost-effective option for businesses with moderate production needs. However, Coperion's machine boasts higher efficiency and durability, making it suitable for businesses with higher production demands and requiring long-term reliability.
Advantages of Using Extruded Animal Food
Extruded animal food offers numerous advantages over traditional methods of food processing. Firstly, the extrusion process allows for precise control over the texture and shape of the final product, resulting in consistent quality and improved palatability for animals. Additionally, extrusion facilitates the incorporation of various nutrients and additives, ensuring a balanced and nutritionally dense diet for animals.
Moreover, extruded animal food has a higher digestibility compared to non-extruded counterparts, leading to better nutrient absorption and reduced waste. This is especially beneficial for livestock and pets with sensitive digestive systems or specific dietary requirements. Furthermore, extrusion helps to eliminate harmful bacteria and toxins through the high-temperature and high-pressure cooking process, enhancing the safety of the final product.
Another advantage of using extruded animal food is its extended shelf life and reduced spoilage. The extrusion process effectively removes moisture from the ingredients, inhibiting microbial growth and preserving the freshness of the food for longer periods. This is particularly advantageous for large-scale animal feed production and distribution networks where storage and transportation logistics are critical factors.
The advantages of using extruded animal food, including improved palatability, enhanced nutrition, better digestibility, increased safety, and extended shelf life, make it a preferred choice for pet owners, livestock farmers, and commercial feed manufacturers alike.
Applications of Animal Food Extruders
Animal food extruders are commonly used in the production of pet foods, including dry kibble and treats. The extrusion process allows for precise control over the texture, shape, and nutritional content of the final product, meeting the specific dietary requirements of different pets. Additionally, extruded pet foods often undergo a cooking process during extrusion, which enhances palatability and digestibility.
Another significant application of animal food extruders is in the aquafeed industry. Extruded fish and shrimp feeds are widely utilized due to their superior nutrient retention, water stability, and ease of handling. The extrusion process enables the incorporation of various ingredients such as fish meal, grains, and supplements, resulting in balanced and nutritionally dense feeds for aquaculture species.
Beyond traditional animal feeds, extruders are increasingly being used in the production of specialty and functional pet treats. These treats can be customized to meet specific dietary needs, such as weight management, dental health, or allergy management. The flexibility of the extrusion process allows for the incorporation of functional ingredients, such as vitamins, minerals, and additives, to enhance the health and well-being of pets.
In addition to food applications, animal food extruders are utilized in the pharmaceutical industry for the production of medicated feeds and supplements. The precise control over ingredient formulation and processing parameters ensures the uniform distribution of active pharmaceutical ingredients (APIs) in the final product, promoting animal health and disease prevention.
Factors Influencing Extruded Animal Food Quality
The quality of raw materials used in extruded animal foods significantly impacts the nutritional value, palatability, and physical properties of the final product. High-quality ingredients, such as fresh meats, grains, and supplements, contribute to superior product quality, while inferior or contaminated ingredients may compromise safety and nutritional integrity.
Formulation plays a crucial role in determining the nutritional composition and functional attributes of extruded animal foods. Proper balancing of macronutrients (proteins, carbohydrates, and fats), micronutrients (vitamins and minerals), and additives (antioxidants, preservatives, etc.) is essential to meet the dietary requirements of target animal species and achieve desired product characteristics.
The extrusion process itself is a critical determinant of product quality. Factors such as barrel temperature, screw speed, moisture content, and die configuration influence the texture, appearance, and nutritional stability of extruded animal foods. Optimal processing conditions must be carefully controlled to ensure uniform cooking, expansion, and gelatinization of ingredients, while minimizing nutrient degradation and undesirable chemical reactions.
Furthermore, the design and condition of the extrusion equipment play a vital role in achieving consistent product quality. Proper maintenance of machinery, including screw elements, die plates, and cooling systems, is essential to prevent wear and tear, minimize downtime, and ensure product uniformity. Additionally, the selection of appropriate equipment configurations, such as single-screw or twin-screw extruders, can impact processing efficiency and product versatility.
Quality control measures, including regular testing and analysis of raw materials, intermediate products, and finished goods, are essential to monitor and maintain product quality throughout the production process. Analytical techniques such as proximate analysis, amino acid profiling, and microbiological testing provide valuable insights into the nutritional composition, safety, and shelf-life of extruded animal foods.
Market Trends and Outlook for Animal Food Extruders
The global market for animal food extruders is experiencing steady expansion, with a compound annual growth rate (CAGR) projected to exceed X% over the forecast period. This growth can be attributed to the rising consumption of meat, dairy, and aquaculture products worldwide, leading to a surge in demand for efficient and cost-effective methods of producing nutritious animal feed.
One of the key trends driving the market for animal food extruders is the growing preference for customized feed formulations tailored to meet the specific nutritional requirements of different animal species and stages of growth. Extrusion technology enables precise control over ingredient composition, particle size, and digestibility, allowing feed manufacturers to develop specialized diets that optimize animal health, performance, and productivity.
Furthermore, there is increasing emphasis on sustainability and environmental stewardship in the animal feed industry, prompting manufacturers to adopt extrusion processes that minimize waste, energy consumption, and environmental impact. As a result, there is a rising demand for advanced extruders equipped with innovative features such as energy-efficient heating systems, automated controls, and integrated waste management solutions.
Another notable trend in the market for animal food extruders is the growing adoption of digitalization and Industry 4.0 technologies to enhance manufacturing efficiency, product quality, and traceability. Modern extrusion systems are equipped with sensors, data analytics, and connectivity features that enable real-time monitoring of process parameters, predictive maintenance, and remote troubleshooting, thereby optimizing production processes and reducing downtime.
Looking ahead, the outlook for the animal food extruder market remains promising, driven by factors such as increasing investments in research and development, expanding applications in pet food and specialty animal feeds, and growing demand from emerging markets in Asia-Pacific and Latin America. However, manufacturers will need to continue innovating and adapting to evolving consumer preferences, regulatory requirements, and market dynamics to sustain growth and competitiveness in the long term.
FAQs: Frequently Asked Questions about Animal Food Extruders
1. What is an animal food extruder, and how does it work?
An animal food extruder is a specialized machine used in the food industry to process raw ingredients into extruded animal feed products. It works by forcing a mixture of ingredients through a die under high pressure and temperature, resulting in the expansion and shaping of the feed into specific shapes and sizes.
2. What types of animal food extruders are available in the market?
There are various types of animal food extruders available, including single-screw extruders, twin-screw extruders, and laboratory-scale extruders. Each type has its unique features and capabilities, depending on factors such as production capacity, processing flexibility, and extrusion efficiency.
3. What are the key factors influencing the quality of extruded animal feed?
Several factors influence the quality of extruded animal feed, including ingredient selection and formulation, moisture content, temperature and pressure profiles, die configuration, and post-extrusion processing methods. Optimal control of these parameters is essential to ensure the desired nutritional value, texture, and appearance of the final feed product.
4. How can I maintain and troubleshoot an animal food extruder?
Proper maintenance and regular cleaning are crucial for ensuring the smooth operation of an animal food extruder. Routine maintenance tasks include lubrication of moving parts, inspection of wear and tear, and calibration of process controls. In case of troubleshooting issues such as blockages, uneven extrusion, or mechanical failures, refer to the manufacturer's guidelines and seek assistance from qualified technicians if needed.
References
1.Wenger Manufacturing: https://www.wenger.com
2.Clextral: https://www.clextral.com
3.Bühler Group: https://www.buhlergroup.com
4. Baker Perkins: https://www.bakerperkins.com
5.Andritz Group: https://www.andritz.com