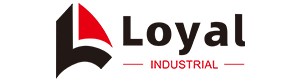
- Shandong Loyal Industrial Co.,Ltd.
- Macaroni Production Machine Instant Noodle Machine Biscuit Making Machine

Home> Company News> The Ultimate Guide to Automatic Japan Panko Bread Crumbs Production Line in 2024

The Ultimate Guide to Automatic Japan Panko Bread Crumbs Production Line in 2024
2024-06-12 17:37:25Introduction to Automatic Japan Panko Bread Crumbs Production Line
In 2024, the Automatic Japan Panko Bread Crumbs production line stands at the forefront of the food processing industry, representing a significant leap in technology and efficiency. This advanced production line is designed to meet the growing demand for panko bread crumbs, known for their light, airy texture that enhances a wide range of culinary dishes. With automation playing a crucial role, these production lines ensure consistent quality and high throughput, making them indispensable for large-scale manufacturers.
The development of the Automatic Japan Panko Bread Crumbs production line integrates cutting-edge technologies, ensuring minimal human intervention and maximizing operational efficiency. Key features include precise temperature control, automated mixing, and continuous baking processes. These lines are engineered to produce uniform bread crumbs that meet stringent quality standards, essential for maintaining the authentic taste and texture that panko bread crumbs are known for.
Investing in an Automatic Japan Panko Bread Crumbs production line offers numerous benefits, including reduced labor costs, enhanced product consistency, and increased production capacity. As the food industry continues to evolve, the adoption of such automated systems is crucial for staying competitive and meeting consumer demands.
Key Components of the Production Line
Component |
Description |
Mixing System |
Ensures consistent dough preparation with precise ingredient measurements and automated mixing. |
Extrusion Unit |
Shapes the dough into uniform strands, essential for achieving the characteristic panko texture. |
Pre-Baking Oven |
Partially bakes the dough strands to set their structure before final baking. |
Final Baking Oven |
Completes the baking process with controlled temperature and humidity to ensure optimal texture. |
Cooling Conveyor |
Cools the baked strands efficiently, preparing them for the next stage of processing. |
Crushing System |
Breaks the baked strands into the desired crumb size with minimal dust and waste. |
Sieving Unit |
Separates the panko crumbs by size, ensuring uniformity and quality control. |
Packaging Machine |
Automates the packaging process, sealing the panko crumbs in moisture-proof bags to maintain freshness. |
This table highlights the key components that make up an Automatic Japan Panko Bread Crumbs production line. Each component plays a critical role in ensuring the production of high-quality panko bread crumbs that meet industry standards and consumer expectations. The integration of these components into a seamless, automated process not only boosts efficiency but also guarantees consistency and quality in the final product.
Technology Behind Panko Bread Crumbs Production
Panko bread crumbs, renowned for their light and crispy texture, have been a staple in Japanese cuisine for decades. The meticulous process of producing these delicate crumbs demands precision and advanced technology. In this section, we delve into the intricate technology that powers the automatic Japan Panko bread crumbs production line.
Key Technologies:
High-Speed Milling Machines: Central to the production line is the high-speed milling machine. These machines are equipped with sharp blades that finely grind the bread into fluffy crumbs. The process is optimized to ensure uniformity in texture and size, a crucial aspect of Panko crumbs.
Air Classification Systems: After milling, the crumbs undergo air classification. This innovative technology separates the crumbs based on their particle size, ensuring consistency in the final product. The larger crumbs are sifted out for reprocessing, while the finer ones proceed to the next stage.
Coating and Crisping: Coating Technology, Crisping Process. Once the crumbs are sorted, they undergo a coating process to enhance their texture and flavor. This involves spraying the crumbs with a precise mixture of oil and seasonings before subjecting them to a controlled crisping process. This step is critical in achieving the signature light and airy texture of Panko crumbs.
Automated Packaging Systems: In the final stage of production, automated packaging systems ensure efficient packaging of the Panko bread crumbs. These systems utilize advanced weighing and sealing technology to package the crumbs in various quantities, catering to different consumer needs.
Benefits of Automation in Bread Crumbs Production
Automation has revolutionized the bread crumbs production industry, offering a plethora of benefits to manufacturers. Below is a detailed table outlining the advantages of automation in bread crumbs production:
Benefits of Automation |
Description |
Increased Efficiency |
Automation streamlines the production process, reducing manual labor and minimizing production time. This results in higher output and increased overall efficiency. |
Consistent Quality |
Automated systems ensure uniformity in product quality, eliminating variations that may arise from manual processes. This consistency is crucial in meeting consumer expectations and maintaining brand reputation. |
Cost Savings |
By minimizing labor costs and optimizing resource utilization, automation leads to significant cost savings for manufacturers. Additionally, automated systems reduce the risk of errors and product wastage, further enhancing cost-effectiveness. |
Enhanced Food Safety |
Automated production lines adhere to strict food safety standards, minimizing the risk of contamination and ensuring product integrity. By implementing automated sanitation processes and real-time monitoring systems, manufacturers can uphold the highest standards of food safety and regulatory compliance. |
Flexibility and Scalability |
Automated systems offer greater flexibility and scalability, allowing manufacturers to adapt to changing market demands and scale production seamlessly. Whether it's adjusting recipe formulations or increasing output capacity, automation provides the agility needed to stay competitive in the dynamic food industry landscape. |
Data-Driven Decision Making |
Automation generates valuable data insights throughout the production process, enabling manufacturers to make informed decisions and optimize their operations. By analyzing production metrics and performance indicators, companies can identify areas for improvement, enhance efficiency, and drive continuous innovation. |
Choosing the Right Equipment for Your Production Line
Selecting the appropriate equipment for your bread crumbs production line is crucial to ensuring optimal performance and product quality. Below is a comprehensive table outlining the key factors to consider when choosing equipment for your production line:
Equipment Type |
Description |
Milling Machines |
Consider the capacity and efficiency of milling machines, ensuring they can process the desired volume of bread into fine crumbs. Look for machines with adjustable settings to achieve the desired texture and particle size. |
Coating Systems |
Evaluate the capabilities of coating systems, including their ability to evenly coat the crumbs with oil and seasonings. Opt for systems that offer precise control over the coating process to achieve consistent flavor and texture. |
Crisping Equipment |
Choose crisping equipment that can uniformly crisp the coated crumbs while maintaining their light and airy texture. Look for systems with temperature and airflow controls to ensure precise crisping without overcooking or burning the crumbs. |
Packaging Machinery |
Assess the packaging machinery based on its speed, accuracy, and flexibility. Select systems that can efficiently package the crumbs in various formats, such as bags or containers, while minimizing downtime for changeovers and maintenance. |
Automation Software |
Invest in automation software that integrates seamlessly with your equipment and provides comprehensive monitoring and control capabilities. Look for features such as real-time data analytics, remote monitoring, and predictive maintenance to optimize production efficiency and performance. |
Safety and Compliance |
Prioritize equipment that meets industry standards for food safety and regulatory compliance. Ensure that all components are made from food-grade materials and that the equipment is designed for easy cleaning and sanitation to minimize the risk of contamination. |
By carefully considering these factors and selecting equipment that aligns with your production requirements and quality standards, you can build a robust and efficient bread crumbs production line that meets the demands of today's market.
Installation and Setup Process
Setting up an Automatic Japan Panko Bread Crumbs Production Line requires meticulous planning and precise execution. The installation process involves several key steps to ensure optimal functionality and efficiency.
Before installing the production line, it is crucial to assess the designated site thoroughly. Ensure the area is spacious enough to accommodate the machinery and allows for seamless workflow. Additionally, check for adequate ventilation and access to utilities such as electricity, water, and drainage systems. Clear any obstacles or debris from the site to create a safe working environment.
Once the site is ready, carefully position each component of the production line according to the layout plan. Begin with the main equipment, such as the mixer, conveyor belts, and ovens, ensuring they are securely anchored to the floor for stability. Pay close attention to the arrangement to optimize the flow of ingredients and finished products throughout the production process.
Connect each machine to the power supply and verify that all electrical connections are properly grounded to prevent any safety hazards. Follow the manufacturer's instructions for wiring and configuration to ensure compatibility and functionality. Similarly, establish mechanical connections between the various components, such as conveyor belts and mixers, ensuring smooth operation and minimal downtime.
Once the installation is complete, conduct comprehensive testing and calibration of the production line. Run a series of trial runs to identify any potential issues or inefficiencies and make necessary adjustments. Verify the accuracy of temperature controls, conveyor speeds, and other critical parameters to guarantee consistent quality and performance.
Maintenance Tips for Long-Lasting Equipment
Proper maintenance is essential for maximizing the lifespan and efficiency of your Automatic Japan Panko Bread Crumbs Production Line. Follow these maintenance tips to ensure smooth operation and minimize downtime.
1. Regular Cleaning
Maintain a strict cleaning schedule to prevent the buildup of debris and contaminants on the machinery. Clean all surfaces, including conveyor belts, mixers, and ovens, using approved cleaning agents and sanitizers. Pay special attention to areas prone to accumulation, such as corners and crevices, to maintain optimal hygiene standards.
2. Lubrication and Inspection
Regularly lubricate moving parts and bearings to reduce friction and prevent premature wear and tear. Inspect all components for signs of damage or deterioration, such as worn belts or loose fittings, and replace them as needed. Conduct routine inspections of motors, gears, and other critical components to detect potential issues early and avoid costly repairs.
3. Calibration and Adjustment
Periodically recalibrate the production line to ensure accuracy and consistency in product quality. Verify the calibration of temperature sensors, timers, and other control mechanisms to maintain precise control over the production process. Make any necessary adjustments to conveyor speeds, ingredient ratios, or baking temperatures to optimize performance and efficiency.
4. Training and Education
Invest in comprehensive training programs for your maintenance staff to ensure they are proficient in troubleshooting and servicing the equipment. Provide ongoing education on best practices for equipment operation, maintenance, and safety to empower your team to identify and address issues proactively. Encourage open communication and collaboration between operators and maintenance personnel to foster a culture of continuous improvement.
Quality Control in Panko Bread Crumbs Production
Quality control is paramount in ensuring the consistency and excellence of Panko bread crumbs. Implementing rigorous quality control measures throughout the production process is essential to meet industry standards and customer expectations. Below is a detailed table outlining key quality control parameters and corresponding inspection methods:
Quality Control Parameter |
Inspection Method |
Texture and Consistency |
Visual inspection |
Texture analysis |
|
Particle size measurement |
|
Moisture Content |
Moisture analyzer |
Oven drying method |
|
Color |
Colorimeter |
Visual comparison |
|
Foreign Material |
Metal detectors |
Sieving |
|
Magnetic separation |
|
Packaging Integrity |
Seal integrity test |
Package leak detection |
|
Visual inspection |
Implementing robust quality control protocols not only ensures product consistency and customer satisfaction but also safeguards your brand reputation and market competitiveness in the rapidly evolving food industry landscape.
Market Trends and Demand for Panko Bread Crumbs
The market for Panko bread crumbs has witnessed remarkable growth in recent years, fueled by evolving consumer preferences and the increasing demand for convenience foods. As people embrace busier lifestyles, the need for quick and easy meal solutions has propelled the popularity of Panko bread crumbs, renowned for their light, crispy texture and versatile applications in various cuisines.
In tandem with this surge in demand, the adoption of automatic Japan Panko bread crumbs production lines has become increasingly prevalent among food manufacturers. These advanced production lines offer enhanced efficiency, consistency, and scalability, catering to the requirements of modern food processing facilities.
One of the notable trends driving the market is the growing consumer inclination towards healthier eating habits. With an emphasis on cleaner labels and natural ingredients, manufacturers are responding by offering Panko bread crumbs made from high-quality ingredients, devoid of artificial additives or preservatives. Automatic production lines equipped with state-of-the-art technology facilitate the production of premium-grade Panko bread crumbs while ensuring adherence to stringent quality standards.
Additionally, the rise of e-commerce platforms and online grocery channels has facilitated greater accessibility to Panko bread crumbs for consumers worldwide. This accessibility factor, coupled with the convenience of automatic production lines, has contributed to the expansion of the global Panko bread crumbs market, transcending geographical boundaries and reaching new demographics.
Case Studies of Successful Production Lines
In the realm of Panko bread crumbs production, several case studies exemplify the efficacy and benefits of automated production lines in meeting the evolving needs of the industry.
One such case study involves a leading food manufacturer based in Japan, renowned for its premium-quality Panko bread crumbs. By investing in state-of-the-art automatic production lines, the company achieved significant improvements in production efficiency and product consistency. With the capacity to adjust processing parameters in real-time, the production lines enabled seamless adaptation to fluctuating demand patterns while maintaining optimal product quality.
Similarly, a European food processing facility specializing in artisanal bread products successfully integrated automatic Japan Panko bread crumbs production lines into its operations. By leveraging advanced equipment with customizable features, the facility enhanced its ability to meet bespoke client requirements while streamlining production workflows. The flexibility offered by the automated lines empowered the facility to diversify its product portfolio and capitalize on emerging market opportunities.
These case studies collectively highlight the transformative impact of automatic Japan Panko bread crumbs production lines on the efficiency, quality, and competitiveness of food manufacturing operations. As the industry continues to evolve, embracing automation remains imperative for meeting the dynamic demands of modern consumers while driving sustained growth and innovation in the global Panko bread crumbs market.
Reference
1.Baker Perkins - bakerperkins.com
2.GEA Group - gea.com
3.Heat and Control - heatandcontrol.com
4.Hosokawa Micron - hosokawamicron.com
5.Fritsch Group - fritsch-group.com