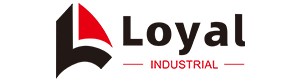
- Shandong Loyal Industrial Co.,Ltd.
- Macaroni Production Machine Instant Noodle Machine Biscuit Making Machine

Home> Company News> Everything you need to know about automatic instant nutritional powder cereal food porridge production line in 2024

Everything you need to know about automatic instant nutritional powder cereal food porridge production line in 2024
2024-07-11 16:26:33Overview of the Growing Demand for Instant Nutritional Powder Cereal Food Porridge
In today's fast-paced world, convenience and nutrition are paramount for consumers. This shift in consumer preferences has led to a significant increase in the demand for instant nutritional powder cereal food porridge. As lifestyles become busier, more people are seeking quick and healthy meal options that can be prepared with minimal effort. Instant nutritional powder cereal food porridge fits this need perfectly, offering a balanced meal that is easy to prepare and consume on the go.
The rise in health consciousness has also contributed to the growing popularity of these products. Consumers are increasingly aware of the importance of a nutritious diet and are looking for foods that provide essential vitamins and minerals. Instant nutritional powder cereal food porridge, often enriched with additional nutrients, meets these health requirements while offering convenience.
Importance of High Efficiency and Energy Saving in Food Production
To meet this growing demand, manufacturers are turning to advanced production technologies that enhance efficiency and reduce energy consumption. The implementation of a fully automatic instant nutritional powder cereal food porridge production line is a critical step in this direction. These systems streamline the production process, enabling manufacturers to produce large quantities of high-quality porridge efficiently.
High efficiency in production not only meets market demands but also ensures that manufacturers remain competitive. By optimizing production processes, companies can reduce costs, increase output, and improve product consistency. Energy-saving solutions are equally important, as they help reduce the environmental impact of production and lower operational costs. In an era where sustainability is becoming increasingly important, adopting energy-efficient practices is not just beneficial but necessary.
A fully automatic instant nutritional powder cereal food porridge production line combines these aspects, offering a solution that boosts production capacity while minimizing energy usage. This integration of high efficiency and energy-saving technologies represents the future of food manufacturing, aligning with both consumer needs and environmental goals.
Understanding the Production Line
Key Components and Their Functions
A fully automatic instant nutritional powder cereal food porridge production line is an intricate system designed to streamline the manufacturing process from raw materials to finished products. Understanding the key components and their functions is essential for grasping how these systems enhance efficiency and energy savings.
1. Raw Material Handling System: This is the starting point of the production line where raw ingredients such as cereals, vitamins, minerals, and other additives are received and prepared. Advanced handling systems ensure accurate dosing and mixing, which is critical for maintaining the nutritional value and consistency of the porridge.
2. Mixing and Blending Equipment: Once the raw materials are prepared, they are transferred to mixers and blenders. These machines are designed to create a homogeneous mixture, ensuring that each portion of the instant nutritional powder cereal food porridge contains the right balance of ingredients. High-speed blenders equipped with precision controls maintain consistency while minimizing processing time.
3. Extrusion Machines: The mixed ingredients are then fed into extrusion machines, which play a pivotal role in shaping and cooking the product. Extrusion technology allows for precise control over texture and density, which is crucial for producing high-quality instant porridge. These machines use heat and pressure to cook the ingredients, transforming them into a form that is easy to rehydrate and consume.
4. Drying Systems: After extrusion, the product needs to be dried to achieve the desired moisture content and shelf stability. Advanced drying systems, such as fluid bed dryers or rotary dryers, ensure that the product is dried evenly and efficiently. These systems often incorporate energy-saving technologies such as heat recovery to reduce overall energy consumption.
5. Milling and Sifting Machines: Once dried, the product is milled to a fine powder. Milling machines are designed to achieve the desired particle size, which is critical for the texture and rehydration properties of the porridge. Sifting machines then remove any oversized particles, ensuring uniformity in the final product.
6. Packaging Systems: The final stage of the production line involves packaging the instant nutritional powder cereal food porridge. Automated packaging systems fill and seal the product in various formats, such as pouches, cans, or sachets. These systems are designed to be flexible and efficient, ensuring that the product is packaged quickly and safely.
Overview of the Production Process from Raw Ingredients to Finished Product
The production process for an automatic instant nutritional powder cereal food porridge production line involves several critical stages, each designed to ensure high efficiency and energy savings while maintaining product quality.
Receiving and Preparing Raw Materials |
The process begins with the careful selection and preparation of raw materials. Ingredients are received, weighed, and inspected to ensure they meet quality standards. This initial step sets the foundation for the entire production process. |
Mixing and Blending |
The prepared raw materials are then mixed and blended to create a uniform mixture. This step is crucial for ensuring that the nutritional profile of the porridge is consistent throughout each batch. Precision mixing equipment ensures that all ingredients are evenly distributed. |
Extrusion |
The mixed ingredients are extruded, a process that involves cooking the mixture under controlled conditions of heat and pressure. This step not only shapes the product but also enhances its nutritional value by making the nutrients more bioavailable. |
Drying |
The extruded product is dried to remove excess moisture, which is essential for shelf stability. Advanced drying systems ensure that the product is dried uniformly and efficiently, reducing the risk of spoilage. |
Milling and Sifting |
The dried product is milled to achieve the desired particle size and then sifted to remove any inconsistencies. This step ensures that the final product is a fine powder that rehydrates easily and consistently. |
Packaging |
Finally, the product is packaged using automated systems. These systems fill and seal the product in airtight containers, protecting it from contamination and extending its shelf life.
|
Benefits of a Fully Automatic System
Increased Efficiency and Productivity
The implementation of a fully automatic instant nutritional powder cereal food porridge production line significantly enhances efficiency and productivity. Automated systems streamline each step of the production process, from raw material handling to packaging, minimizing manual intervention and reducing the likelihood of human error. This leads to a more consistent and reliable production output.
1. Continuous Operation: Unlike manual or semi-automatic systems, fully automatic production lines can operate continuously with minimal downtime. This ensures a steady production flow, meeting high-demand requirements without interruption. The seamless integration of various components—mixers, extruders, dryers, and packaging machines—ensures that the entire process runs smoothly and efficiently.
2. Precision and Consistency: Automation brings precision to the production process. Advanced control systems and sensors monitor each stage, ensuring that parameters such as temperature, pressure, and mixing times are maintained within optimal ranges. This results in a consistent product quality, batch after batch, which is critical for maintaining brand reputation and consumer trust.
Energy Savings and Cost Reduction
One of the most significant advantages of a fully automatic instant nutritional powder cereal food porridge production line is its ability to save energy and reduce costs. Energy-efficient machinery and optimized processes contribute to lower operational costs and a smaller environmental footprint.
1. Energy-Efficient Machinery: Modern production lines are equipped with energy-efficient machines that consume less power while maintaining high performance. For example, advanced drying systems utilize heat recovery technologies to minimize energy waste. This not only reduces energy consumption but also lowers utility bills, leading to significant cost savings over time.
2. Reduced Waste: Automation helps in minimizing material wastage by ensuring precise measurements and reducing the chances of errors. Automated dosing and mixing systems ensure that the exact amount of ingredients is used, reducing excess and preventing wastage. This not only conserves resources but also lowers raw material costs.
Enhanced Product Quality and Safety
Automation plays a crucial role in enhancing the quality and safety of the products. Fully automatic systems ensure that each step of the production process adheres to strict quality standards, resulting in a superior final product.
1. Hygiene and Safety: Automated systems are designed to meet stringent hygiene and safety standards. The use of stainless steel and other non-corrosive materials ensures that the machinery is easy to clean and maintain. Automated cleaning-in-place (CIP) systems further enhance hygiene by allowing for thorough cleaning without disassembling the equipment, reducing the risk of contamination.
2. Quality Control: Real-time monitoring and control systems continuously check the quality parameters of the product. Any deviations from the set standards are detected and corrected immediately, ensuring that the final product meets the desired quality specifications. This level of control is difficult to achieve with manual processes, making automation a critical component in quality assurance.
Labor Savings and Workforce Optimization
The transition to a fully automatic instant nutritional powder cereal food porridge production line can lead to significant labor savings and better workforce optimization. Automation reduces the need for manual labor, allowing companies to reallocate their workforce to more strategic roles.
1. Reduced Labor Costs: By automating repetitive and labor-intensive tasks, companies can significantly reduce their labor costs. Fewer operators are needed to monitor and control the production line, which translates to lower payroll expenses. This is particularly beneficial in regions with high labor costs.
2. Workforce Optimization: With automation handling routine tasks, employees can focus on more critical and strategic functions such as quality control, maintenance, and process optimization. This not only enhances overall productivity but also leads to a more motivated and skilled workforce.
In conclusion, the benefits of a fully automatic instant nutritional powder cereal food porridge production line are manifold. From increased efficiency and energy savings to enhanced product quality and labor optimization, automation transforms the production process, making it more competitive and sustainable. Adopting these advanced systems is a strategic move for any manufacturer looking to stay ahead in the food industry.
Real-time Monitoring and Adjustments
Real-time monitoring and adjustments are pivotal in maximizing the efficiency and quality of the automatic instant nutritional powder cereal food porridge production line. The integration of advanced sensors and control systems ensures that every phase of the production process operates within optimal parameters, guaranteeing consistency and high-quality output.
Advanced Sensor Integration
1. Precision and Accuracy: Modern production lines are equipped with an array of sensors that monitor various parameters such as temperature, humidity, and pressure in real-time. These sensors provide precise and accurate data, enabling the system to make instantaneous adjustments to maintain optimal conditions. This level of precision is critical in the production of nutritional powder cereal food porridge, where even minor deviations can affect the product's quality and nutritional value.
2. Data Collection and Analysis: The sensors continuously collect data throughout the production process. This data is analyzed in real-time to detect any anomalies or deviations from the set standards. By leveraging sophisticated algorithms and machine learning, the system can predict potential issues and make proactive adjustments to prevent disruptions and maintain consistent product quality.
Automated Control Systems
1. Instantaneous Adjustments: Automated control systems use the data provided by the sensors to make instantaneous adjustments to the production parameters. For instance, if the temperature in a drying chamber starts to deviate from the optimal range, the control system can immediately adjust the heating elements to bring the temperature back to the desired level. This ensures that each batch of nutritional powder cereal food porridge is produced under ideal conditions.
2. Reduced Human Intervention: With real-time monitoring and automated adjustments, the need for manual intervention is significantly reduced. This not only minimizes the risk of human error but also allows the production line to operate continuously without interruptions. The automated system can handle complex adjustments more quickly and accurately than human operators, leading to more efficient and reliable production.
Benefits to Quality and Efficiency
1. Consistent Product Quality: The ability to monitor and adjust production parameters in real-time ensures that the final product meets the highest quality standards. Consistency in quality is essential for maintaining consumer trust and brand reputation, particularly in the food industry where nutritional content and safety are paramount.
2. Enhanced Efficiency: Real-time monitoring and adjustments contribute to overall production efficiency. By maintaining optimal conditions throughout the production process, the system reduces waste, lowers energy consumption, and minimizes downtime. This results in a more cost-effective operation and a higher yield of quality products.
3. Proactive Maintenance: The data collected by the sensors can also be used for predictive maintenance. By analyzing trends and identifying patterns, the system can predict when a component is likely to fail and schedule maintenance before a breakdown occurs. This proactive approach reduces unplanned downtime and extends the lifespan of the production line equipment.
In conclusion, real-time monitoring and adjustments are integral components of a fully automatic instant nutritional powder cereal food porridge production line. The combination of advanced sensors and automated control systems ensures that the production process is efficient, consistent, and of the highest quality. This technology not only enhances the overall performance of the production line but also provides significant cost savings and a competitive edge in the market.
Reference
The following are five authoritative foreign literature websites in the field of Industrial food machinery:
1. Food Engineering Magazine
Website: https://www.foodengineeringmag.com/
2.Food Processing Magazine
Website: https://www.foodprocessing.com/
3.Journal of Food Engineering
Website:https://www.journals.elsevier.com/journal-of-food-engineering
4. Food Manufacturing Magazine
Website:https://www.foodmanufacturing.com/
5. International Journal of Food Science & Technology
Website:https://onlinelibrary.wiley.com/