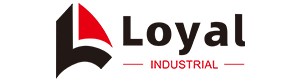
- Shandong Loyal Industrial Co.,Ltd.
- Macaroni Production Machine Instant Noodle Machine Biscuit Making Machine

Home> Company News> Everything you need to know about automatic nutrition powder processing eauipment in 2024

Everything you need to know about automatic nutrition powder processing eauipment in 2024
2024-07-11 16:37:39Overview of the Health Food Industry
The health food industry has seen exponential growth over the past few decades, driven by increasing consumer awareness of nutrition and wellness. As people become more health-conscious, the demand for nutritious, convenient food products has surged. Among these products, nutrition powders have gained significant popularity due to their ease of use, long shelf life, and ability to deliver essential nutrients efficiently.
Nutrition powders come in various forms, including protein powders, meal replacements, and dietary supplements, catering to diverse dietary needs and preferences. They are used by athletes for performance enhancement, by individuals aiming for weight management, and by those seeking to supplement their diet with additional vitamins and minerals.
Importance of Nutrition Powder in Health Food
Nutrition powders play a critical role in the health food sector due to their versatility and effectiveness. They offer a convenient way to intake essential nutrients, making them ideal for busy lifestyles. Furthermore, these powders are formulated to meet specific nutritional requirements, whether it’s to build muscle, lose weight, or boost overall health.
With the rising popularity of these products, the production process has had to keep pace with demand. This has led to significant advancements in the technology and machinery used to produce nutrition powders. High-quality, fully automatic equipment is now essential to ensure efficiency, consistency, and quality in production.
Introduction to Automatic Nutrition Powder Processing Equipment
The advent of automatic nutrition powder processing equipment has revolutionized the health food industry. This machinery has brought about a new era of production capabilities, enabling manufacturers to meet the high demand for nutrition powders while maintaining superior quality and consistency.
Understanding Automatic Nutrition Powder Processing Equipment
Definition and Basic Functions
Automatic nutrition powder processing equipment refers to a range of advanced machinery designed to streamline and optimize the production of nutrition powders. These machines automate various stages of the production process, from mixing raw ingredients to packaging the final product, ensuring consistency, quality, and efficiency.
The basic functions of automatic nutrition powder processing equipment include
Mixing |
Combining raw ingredients uniformly to ensure a consistent nutrient profile across all batches. |
Blending |
Further refining the mix to achieve the desired texture and homogeneity. |
Drying |
Removing moisture from the mixture to extend shelf life and prevent spoilage. |
Packaging |
Accurately filling and sealing packages to maintain product integrity and facilitate distribution. |
Key Components and Machinery
Automatic nutrition powder processing equipment typically consists of several key components and specialized machinery, each designed to perform specific tasks within the production line:
1.Raw Material Feeders:These systems automate the precise feeding of raw ingredients into the production line, ensuring accurate measurements and consistent quality.
2.Mixers and Blenders:Advanced mixing and blending machines combine ingredients uniformly, crucial for maintaining the nutritional integrity of the final product. These machines often feature variable speed controls and programmable settings to cater to different recipes.
3.Dryers:Drying equipment, such as fluid bed dryers or spray dryers, efficiently removes moisture from the mixed ingredients. This step is critical for ensuring the stability and shelf life of nutrition powders.
4.Sieving and Screening Machines:These machines remove any impurities or oversized particles from the mixture, ensuring a fine, consistent powder.
5.Packaging Machines:Automatic packaging machines fill, seal, and label the nutrition powder packages. They are designed for high-speed operations and can handle various packaging formats, from sachets to large containers.
Advantages Over Traditional Processing Methods
The adoption of automatic nutrition powder processing equipment offers several advantages over traditional, manual methods:
1.Efficiency:Automation significantly speeds up the production process, enabling higher output rates and reducing production time. This efficiency is crucial for meeting the growing demand for nutrition powders in the health food industry.
2.Consistency:Automated systems ensure that each batch of nutrition powder is consistent in terms of composition and quality. This consistency is essential for maintaining consumer trust and meeting regulatory standards.
3.Quality Control:Advanced sensors and monitoring systems integrated into automatic nutrition powder processing equipment provide real-time data on various parameters, such as moisture content and particle size. This allows for immediate adjustments and ensures that the final product meets strict quality standards.
4.Labor Savings:By automating labor-intensive tasks, manufacturers can reduce their reliance on manual labor, lowering labor costs and minimizing the risk of human error.
5.Scalability:Automatic systems can be easily scaled up to increase production capacity without compromising quality. This scalability is vital for businesses looking to expand their operations and enter new markets.
Technological Innovations in Automatic Nutrition Powder Processing Equipment
Recent Advancements in Automation Technology
The health food industry has significantly benefited from recent advancements in automation technology, particularly in the development of automatic nutrition powder processing equipment. These innovations have brought about a paradigm shift, enhancing the efficiency, precision, and scalability of nutrition powder production.
One of the most notable advancements is the integration of advanced control systems that allow for precise monitoring and adjustment of various parameters throughout the production process. These control systems utilize state-of-the-art sensors and actuators to ensure optimal conditions are maintained, from ingredient mixing to final packaging. For example, advanced mixing systems can now adjust the speed and duration of the mixing process based on real-time data, ensuring uniformity and consistency in the product.
Another significant advancement is the development of high-speed packaging machines. These machines not only increase the speed of the packaging process but also improve accuracy and reduce waste. They are equipped with sophisticated filling mechanisms that ensure each package contains the exact amount of product, thus maintaining consistency and quality.
Integration of IoT and Smart Systems
The integration of the Internet of Things (IoT) and smart systems in automatic nutrition powder processing equipment has further revolutionized the industry. IoT-enabled devices provide real-time data and analytics, allowing manufacturers to monitor and optimize every aspect of the production process remotely.
Smart systems, powered by machine learning and artificial intelligence, can predict and adjust to potential issues before they occur, minimizing downtime and enhancing productivity. For instance, predictive maintenance algorithms can analyze data from sensors to predict when a machine is likely to fail, allowing for proactive maintenance and reducing unplanned downtime.
IoT integration also facilitates better traceability and transparency in the production process. Every step, from raw material sourcing to final product packaging, can be tracked and recorded. This level of transparency is crucial for maintaining quality standards and complying with regulatory requirements.
Case Studies of Innovative Equipment in Use
Several leading companies in the health food industry have successfully implemented these technological innovations in their production lines, setting new benchmarks for efficiency and quality.
For example, a major nutrition powder manufacturer integrated fully automatic mixing and blending systems with IoT capabilities. This integration resulted in a 20% increase in production efficiency and a significant reduction in product variability. The real-time monitoring and control features allowed the company to maintain consistent quality across all batches, enhancing their market reputation.
Another case study involves a company that adopted advanced drying technology in their automatic nutrition powder processing equipment. By utilizing fluid bed dryers with precise temperature and airflow controls, they were able to achieve uniform drying, improve product stability, and extend shelf life. This technological innovation not only improved product quality but also reduced energy consumption by 15%.
Enhancing Efficiency with Fully Automatic Systems
Benefits of Full Automation in Processing
The shift towards fully automatic systems in the production of nutrition powders has marked a significant improvement in efficiency. Automatic nutrition powder processing equipment, equipped with advanced automation technologies, streamlines the entire production process, leading to substantial gains in productivity and cost savings.
One of the primary benefits of full automation is the significant reduction in manual labor. Automated systems handle complex and repetitive tasks with high precision and speed, minimizing the need for human intervention. This not only reduces labor costs but also mitigates the risk of human error, ensuring a consistently high-quality product.
Furthermore, automated systems facilitate faster production cycles. With the ability to operate continuously without breaks, these systems can significantly increase output. This is particularly advantageous in meeting the growing demand for nutrition powders, allowing manufacturers to scale up their operations efficiently.
Impact on Production Speed and Consistency
Automatic nutrition powder processing equipment enhances production speed through streamlined operations. By automating critical stages such as mixing, drying, and packaging, manufacturers can achieve faster throughput times. Advanced control systems and sensors ensure that each step of the process is executed with precision, maintaining optimal conditions and reducing the likelihood of delays.
Consistency is another crucial advantage of fully automatic systems. Manual processes are prone to variability, which can lead to inconsistencies in product quality. Automatic nutrition powder processing equipment, on the other hand, operates with high repeatability and accuracy. This ensures that every batch of nutrition powder meets the same quality standards, which is essential for maintaining consumer trust and complying with regulatory requirements.
Examples of High-Efficiency Automatic Nutrition Powder Processing Equipment
Several examples of high-efficiency automatic nutrition powder processing equipment illustrate the transformative impact of these technologies:
1.Automated Mixing Systems:These systems are designed to mix raw ingredients uniformly, ensuring a consistent nutrient profile. They feature programmable settings that adjust the mixing parameters based on the specific requirements of each batch. This level of control results in a homogeneous product, free from clumps and inconsistencies.
2.High-Speed Dryers:Fluid bed dryers and spray dryers equipped with precise temperature and airflow controls are used to remove moisture from the mixed ingredients efficiently. These dryers operate at high speeds, significantly reducing drying times while ensuring uniform moisture content across the product.
3.Advanced Packaging Machines:Modern packaging machines are capable of filling, sealing, and labeling packages at high speeds. They utilize accurate filling mechanisms to ensure each package contains the exact amount of product, reducing waste and improving packaging efficiency. These machines are also adaptable to various packaging formats, making them versatile for different product lines.
Quality Control and Consistency
Ensuring Product Quality Through Automation
The implementation of automatic nutrition powder processing equipment plays a pivotal role in ensuring product quality. Automation introduces a level of precision and control that is unattainable through manual processes. Advanced sensors and real-time monitoring systems embedded within the equipment continuously track critical parameters such as temperature, humidity, and mixing times. This data-driven approach allows for immediate adjustments, ensuring optimal processing conditions are maintained throughout the production cycle.
Automatic systems also incorporate sophisticated quality control mechanisms that detect and rectify anomalies in real-time. For instance, metal detectors and X-ray inspection systems can identify and remove foreign particles from the product stream, safeguarding the purity of the nutrition powders. Additionally, automated weighing systems ensure that each package contains the exact amount of product, maintaining consistency in serving sizes and nutritional content.
Standardization and Precision in Processing
The standardization brought about by automatic nutrition powder processing equipment is vital for maintaining product consistency. By automating key stages such as ingredient mixing, blending, and drying, manufacturers can ensure that each batch of nutrition powder is produced to the same exacting standards. This level of precision is crucial for meeting regulatory requirements and consumer expectations.
Automated mixing systems, for example, utilize programmable logic controllers (PLCs) to manage the mixing process. These controllers can be programmed with specific recipes, ensuring that the correct proportions of ingredients are used every time. This not only enhances the nutritional profile of the powders but also prevents variations that could affect taste, texture, and shelf life.
Quality Assurance Protocols and Technologies
To maintain the highest standards of quality, manufacturers employing automatic nutrition powder processing equipment adopt rigorous quality assurance protocols. These protocols encompass a range of technologies and procedures designed to monitor and control the production process.
One such technology is the use of high-resolution optical sorting machines. These machines employ cameras and sensors to inspect the product for defects or impurities. Any anomalies detected are automatically removed from the production line, ensuring that only the highest quality product reaches the consumer.
Another essential technology is the implementation of inline spectroscopy. This technique allows for the real-time analysis of the nutritional content of the powders, ensuring that they meet the specified nutritional claims. By continuously monitoring the composition of the product, manufacturers can make necessary adjustments to maintain consistency and quality.
In addition to technological advancements, stringent hygiene and sanitation protocols are followed. Automated cleaning systems, known as Clean-in-Place (CIP) systems, are integrated into the equipment to ensure thorough cleaning between production runs. This prevents cross-contamination and maintains the integrity of the nutrition powders.
Reference
The following are five authoritative foreign literature websites in the field of Industrial food machinery:
1. Food Engineering Magazine
Website: https://www.foodengineeringmag.com/
2.Food Processing Magazine
Website: https://www.foodprocessing.com/
3.Journal of Food Engineering
Website:https://www.journals.elsevier.com/journal-of-food-engineering
4. Food Manufacturing Magazine
Website:https://www.foodmanufacturing.com/
5. International Journal of Food Science & Technology
Website:https://onlinelibrary.wiley.com/