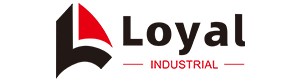
- Shandong Loyal Industrial Co.,Ltd.
- Macaroni Production Machine Instant Noodle Machine Biscuit Making Machine

Home> Company News> Discover The Secret To Perfect nutritional instant rice powder processing line: nutritional instant rice powder processing line Recipes

Discover The Secret To Perfect nutritional instant rice powder processing line: nutritional instant rice powder processing line Recipes
2024-08-02 12:05:46Understanding the Fully Automated Nutritional Instant Rice Powder Processing Line
In the rapidly evolving landscape of the food production industry, the pursuit of efficiency and sustainability has become paramount. This quest has led to the emergence of innovative technologies, one of which is the fully automated nutritional instant rice powder processing line. This advanced system not only revolutionizes the way nutritional instant rice powder is produced but also sets new benchmarks for efficiency and energy conservation.
At its core, the fully automated nutritional instant rice powder processing line is a comprehensive solution designed to streamline the entire production process from start to finish. It encapsulates a series of interconnected machines and equipment, each optimized to perform a specific function within the production cycle. From the initial cleaning and milling stages to the final blending, drying, and packaging, this processing line ensures that every step is executed with precision and efficiency.
One of the key features of this processing line is its automation capabilities. By eliminating the need for manual labor in various stages of production, it significantly reduces the risk of human error and contamination. Moreover, the integration of advanced control systems allows for real-time monitoring and adjustment of production parameters, ensuring optimal performance and consistency in the final product.
Another critical aspect of the fully automated nutritional instant rice powder processing line is its ability to preserve the nutritional value of the rice during processing. This is achieved through the use of gentle yet effective processing methods that minimize heat exposure and mechanical stress, thereby preserving essential nutrients such as vitamins, minerals, and dietary fibers.
Furthermore, the design of this processing line incorporates energy-efficient features that contribute to reduced power consumption and waste minimization. For instance, the use of high-efficiency motors and optimized drying processes can significantly cut down on energy usage. Additionally, the system is designed to recycle and reuse water and other resources where possible, further enhancing its environmental credentials.
Overall, the fully automated nutritional instant rice powder processing line represents a significant advancement in food production technology. Its ability to unlock high efficiency and energy savings while preserving the nutritional integrity of the product makes it an attractive option for manufacturers looking to stay ahead in a competitive market. As the demand for nutritious, convenient, and sustainable food products continues to grow, the role of this processing line in shaping the future of the food industry becomes increasingly important.
Key Components and Their Functions of the Fully Automated Nutritional Instant Rice Powder Processing Line
The fully automated nutritional instant rice powder processing line is a sophisticated system comprised of various components, each playing a vital role in ensuring the smooth and efficient production of high-quality rice powder. In this section, we delve into the key components of this processing line and their respective functions, highlighting how they contribute to unlocking high efficiency and energy savings.
Rice Cleaning and Sorting Station |
The initial stage of the processing line begins with a rice cleaning and sorting station. This component is responsible for removing impurities such as stones, husks, and other foreign materials from the raw rice. Advanced optical and mechanical sorting technologies are employed to ensure that only the purest grains proceed to the next stage. This step is crucial in maintaining the overall quality and purity of the final product. |
Milling and Grinding System |
Following cleaning and sorting, the rice grains enter the milling and grinding system. This component comprises a series of mills and grinders that progressively reduce the size of the rice grains into a fine powder. The precision of this process is essential for achieving a consistent and homogeneous product. Modern milling and grinding systems are designed to minimize heat generation and mechanical stress, thereby preserving the nutritional value of the rice powder. |
Nutrient Enrichment and Blending Unit |
The next step involves the enrichment and blending of the rice powder with essential nutrients and other ingredients. This component ensures that the final product meets specific nutritional requirements and offers a balanced blend of vitamins, minerals, and other health-promoting compounds. Advanced blending technologies are utilized to achieve a uniform distribution of nutrients throughout the powder. |
Drying and Cooling System |
After blending, the rice powder is subjected to a drying and cooling process. This step is crucial in removing moisture and preventing the growth of microorganisms. The drying system employs high-efficiency heaters and air circulation mechanisms to gently and evenly dry the powder, while the cooling system ensures that the product is cooled to an optimal temperature for packaging and storage. |
Packaging and Weighing Machinery |
The final stage of the processing line involves packaging and weighing the dried rice powder. Automated packaging machines are designed to fill pre-formed pouches or containers with precise amounts of powder, ensuring that each package meets the required specifications. These machines are often equipped with sophisticated weighing systems to guarantee accurate and consistent filling. |
Control and Monitoring System |
Underlying the entire processing line is a comprehensive control and monitoring system. This component integrates advanced sensors, processors, and software to monitor and adjust various production parameters in real-time. It ensures that the entire process runs smoothly and efficiently, minimizing downtime and maximizing productivity. The system also provides valuable data for quality control and process optimization. |
Enhanced Efficiency in Production
The fully automated nutritional instant rice powder processing line represents a significant leap forward in terms of enhancing production efficiency. By integrating cutting-edge technologies and automation throughout the entire process, this system streamlines workflows, reduces manual intervention, and optimizes resource utilization, ultimately unlocking new levels of productivity.
Streamlined Workflows |
One of the primary factors contributing to the enhanced efficiency of this processing line is the streamlined nature of its workflows. Each stage of the process, from rice cleaning and sorting to packaging and weighing, is designed to operate seamlessly with the next, minimizing downtime and eliminating bottlenecks. This seamless integration of components ensures that the entire production process runs smoothly, maximizing throughput and minimizing waste. |
Reduced Manual Intervention |
Automation plays a pivotal role in enhancing the efficiency of the nutritional instant rice powder processing line. By automating tasks such as rice cleaning, grinding, blending, drying, and packaging, the need for manual labor is significantly reduced. This not only frees up human resources for more value-added tasks but also eliminates the potential for human error, which can lead to quality issues and downtime. With fewer hands on deck, the production process becomes more streamlined and efficient. |
Optimized Resource Utilization |
Another key factor in the enhanced efficiency of this processing line is its ability to optimize resource utilization. By precisely controlling production parameters such as temperature, humidity, and flow rates, the system ensures that each component operates at peak efficiency. This, in turn, reduces energy consumption, minimizes waste, and extends the lifespan of equipment. Additionally, advanced control and monitoring systems provide real-time insights into the production process, allowing for quick adjustments and optimizations as needed. |
Scalability and Flexibility |
The fully automated nutritional instant rice powder processing line is also designed with scalability and flexibility in mind. As production demands change, the system can be easily adapted to accommodate increased throughput or modified product specifications. This flexibility ensures that the processing line remains efficient and effective, even as market trends and consumer preferences evolve. |
Energy Conservation through Automation
The fully automated nutritional instant rice powder processing line is a testament to the power of automation in unlocking not only high production efficiency but also significant energy savings. By leveraging advanced technologies and innovative designs, this processing line minimizes energy consumption throughout the entire production cycle, aligning with the global push towards sustainable and eco-friendly food manufacturing practices.
1.Precision Control Systems
At the heart of the energy conservation strategy lies the precision control systems employed in the processing line. These systems continuously monitor and adjust production parameters such as temperature, humidity, and motor speeds to ensure optimal operating conditions. By maintaining precise control over these variables, the system minimizes energy waste and ensures that energy is only used when and where it is needed.
2.Efficient Heating and Drying Processes
One of the most energy-intensive stages in rice powder processing is the drying process. However, the fully automated line utilizes highly efficient heating and drying systems that optimize energy usage. Advanced heat recovery systems capture and reuse waste heat, reducing the need for additional energy input. Additionally, intelligent drying algorithms adjust the drying process based on real-time data, ensuring that rice powder is dried to the desired moisture content without over-drying or under-drying, which can both lead to energy waste.
3.Optimized Motor and Drive Systems
The motors and drive systems used in the processing line are designed for maximum efficiency. Energy-efficient motors, coupled with advanced drive technologies, ensure that power is delivered to the equipment with minimal losses. These systems are also programmed to operate only when needed, further reducing energy consumption.
4.Standby and Idle Power Reduction
During periods of downtime or low production, the fully automated nutritional instant rice powder processing line is equipped with features that minimize standby and idle power consumption. By automatically shutting down or placing equipment in low-power modes when not in use, the system ensures that energy is not wasted.
5.Continuous Improvement and Monitoring
To maintain optimal energy conservation, the processing line is equipped with advanced monitoring and analytics tools. These tools provide real-time insights into energy usage and identify areas for improvement. With this data, manufacturers can continuously refine their processes and further reduce energy consumption.
Quality Assurance and Nutritional Integrity
The fully automated nutritional instant rice powder processing line stands as a testament to the integration of cutting-edge technology with rigorous quality assurance measures, ensuring the preservation of nutritional integrity throughout the production process. As consumers become increasingly conscious about the nutritional value of their food, maintaining high standards of quality and nutrition is paramount in today's market.
1.Rigorous Raw Material Selection
At the outset, the processing line begins with the meticulous selection of raw materials. Only the finest, nutrient-rich rice grains are sourced, ensuring that the foundation of the nutritional instant rice powder is of the highest quality. Stringent quality control checks are conducted at the point of entry, verifying the authenticity, purity, and nutritional content of each batch of rice.
2.Precision Cleaning and Milling
Once the raw materials are approved, they undergo a precise cleaning process to remove impurities and debris. This is followed by milling, where advanced milling equipment gently grinds the rice grains into a fine powder, preserving their nutritional properties. The milling process is carefully controlled to ensure uniform particle size and minimal loss of nutrients.
3.Nutrient Retention Techniques
The fully automated line incorporates innovative nutrient retention techniques throughout the processing cycle. Low-temperature drying methods are employed to minimize the loss of heat-sensitive vitamins and minerals. Additionally, gentle handling mechanisms are designed to prevent oxidation and degradation of essential fatty acids and other nutrients.
4.In-Process Quality Control
To maintain the highest level of quality assurance, the processing line is equipped with advanced sensors and monitoring systems that continuously track key quality indicators. From moisture content to nutrient levels, these systems provide real-time data, enabling immediate corrective actions if necessary. Regular sampling and laboratory testing further reinforce the quality control process, ensuring that every batch of nutritional instant rice powder meets or exceeds industry standards.
5.Packaging and Storage Solutions
The final stage of the processing line focuses on preserving the nutritional integrity of the product during packaging and storage. Airtight, light-resistant packaging materials are used to minimize exposure to oxygen and light, which can degrade nutrients over time. Proper storage conditions, including temperature and humidity control, are maintained to ensure that the nutritional value of the rice powder is preserved until it reaches the consumer.
Reference
The following are five authoritative foreign literature websites in the field of Industrial food machinery:
1. Food Engineering Magazine
Website: https://www.foodengineeringmag.com/
2.Food Processing Magazine
Website: https://www.foodprocessing.com/
3.Journal of Food Engineering
Website:https://www.journals.elsevier.com/journal-of-food-engineering
4. Food Manufacturing Magazine
Website:https://www.foodmanufacturing.com/
5. International Journal of Food Science & Technology
Website:https://onlinelibrary.wiley.com/