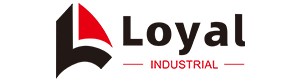
- Shandong Loyal Industrial Co.,Ltd.
- Macaroni Production Machine Instant Noodle Machine Biscuit Making Machine

Home> Processing> Unlock The Secrets Of Efficient nutrition bar production line Manufacturing

Unlock The Secrets Of Efficient nutrition bar production line Manufacturing
2025-05-27 15:39:27If you want to know more story about LOYAL brand, here can help you - https://www.facebook.com/foodmachineloyal
Introduction
In today’s health-conscious world, nutrition bars have carved out a significant share of the snack food market. Consumers are increasingly looking for quick, convenient, and nutrient-rich food options, and nutrition bars perfectly meet that demand. According to a report by the International Food Information Council, over 60% of consumers actively seek healthier snack alternatives—this has led to a substantial rise in the global demand for nutrition bars.
Setting up a nutrition bar production line from scratch is a critical endeavor for any manufacturer entering this fast-growing sector. A well-organized production system is essential not only for ensuring consistent product quality but also for maintaining high output levels and reducing operational inefficiencies. Every piece of equipment, from mixers to cooling tunnels, plays a vital role in the seamless functioning of the entire line.
Understanding the Core Components of a Nutrition Bar Production Line
A successful nutrition bar production line depends on a structured series of processes that convert raw ingredients into consistent, high-quality bars. Each phase of production requires specific nutrition bar equipment to ensure smooth, efficient, and hygienic operations. The most common stages include mixing, forming, and cutting.
Every machine in the nutrition bar production line is engineered to perform its role with precision. As food technology specialist Dr. Elaine Murray states, “The synergy between each stage of production—when supported by the right machinery—is what transforms a basic recipe into a market-ready product.”
Each step of this process contributes to a streamlined, repeatable operation that supports consistent output and high product standards. Understanding these components is the foundation for planning and operating a successful nutrition bar manufacturing facility.
Nutrition bar production line flow chart
Sugar boiled pot--- Mixer--- Cereals bar cutting machine--- Packaging machine
Nutrition bar equipment is not limited to the ones mentioned above, and other equipment can be added as needed.
For example, if you want to make a rounded arched nutrition bar, you need a mold forming machine. If the raw material has high viscosity, you need to add a refrigerator and a strip cutter. If you want coating and latte art, you need to add a coating machine and a latte art machine.
The function of nutrition bar production line
1.Sugar boiled pot: can melt sugar, stir, and boil sugar together
2.Mixer: mixing raw materials. With heat preservation effect, the inner wall is sprayed with Teflon, and the stirring shaft and stirring claws are sprayed with Teflon
3.Cereals bar cutting machine: used for leveling, cooling, cutting and forming of products.
4.Packaging machine: finally, the dried bar is packaged in a suitable container and labeled for distribution. Packaging is an important step to ensure that the product remains fresh and free from contamination during transportation and storage.
Layout for the nutrition bar production line
Our machines can be flexibly arranged according to the size and dimensions of the factory. We can also customize the size of the machine according to the data you provide.
Sample of nutrition bar production line
Other substances and nutrients can be added as needed, such as chocolate, nuts, fruits, iron, calcium, vitamin D, etc.
Planning Your Production Line Layout
The layout of a nutrition bar production line plays a fundamental role in ensuring operational efficiency, product quality, and worker safety. Proper planning of the line layout minimizes material waste, prevents unnecessary delays, and helps maintain a clean, organized manufacturing environment.
One of the first key considerations is space allocation. Manufacturers must assess the available floor area and determine how to accommodate various types of nutrition bar equipment—including mixers, forming units, cooling tunnels, and cutting machines—while maintaining clear pathways for both raw materials and finished products. Equipment spacing should allow for easy access during cleaning, maintenance, and inspection.
Equally important is workflow optimization. The production flow should follow a logical, linear sequence—from ingredient preparation through to packaging—reducing backtracking or crossover between zones. A streamlined layout prevents bottlenecks and enables staff to manage the nutrition bar production line more efficiently.
When arranging machines, it's essential to consider factors such as the direction of product flow, proximity of related processes, and environmental control (e.g., ventilation or temperature management).
As process engineer Thomas Grady notes, “A logical layout based on product flow and equipment function is one of the most effective ways to increase throughput without increasing overhead.” Following this principle ensures that your nutrition bar making machine setup is both practical and scalable as production volumes grow.
In summary, a thoughtfully planned production layout is more than just placing machines in a room—it is the framework that supports a reliable and efficient nutrition bar production line from day one.
Choosing the Right Nutrition Bar Making Machines
Selecting the appropriate nutrition bar making machine is one of the most impactful decisions when establishing a successful production line. The right equipment ensures consistency, durability, hygiene, and operational efficiency—all essential qualities in today’s competitive food industry.
To start, manufacturers must consider their desired output capacity. Machines come in a variety of sizes and speeds to meet different production targets. A small startup operation may opt for semi-automatic machines, while a high-volume facility requires fully automated solutions to meet market demand without compromising on quality.
Material compatibility is another crucial factor. Nutrition bars often include ingredients like sticky syrups, nuts, protein powders, and chocolate—all of which require machines built with food-grade surfaces that prevent clumping or residue buildup. Stainless steel construction is generally preferred for its durability and ease of cleaning.
Ease of cleaning and maintenance should also guide your decision. Machines designed with simple disassembly and minimal hard-to-reach areas can significantly reduce downtime between shifts or product changeovers. As food safety consultant Emily Rhodes explains, “In food production, equipment hygiene is not optional—it’s integral to quality assurance and regulatory compliance.”
Choosing the right nutrition bar equipment is not about buying the most advanced technology, but about selecting machinery that aligns with your production goals, ingredient profile, and operational capabilities.
Installing and Assembling the Equipment
Once the appropriate nutrition bar making machines have been selected, proper installation and assembly are critical to ensure the nutrition bar production line operates safely and efficiently from the start. This phase sets the foundation for consistent performance, hygiene compliance, and product quality.
The installation process begins with positioning the equipment according to the planned layout. Each unit—whether it’s a mixer, forming system, cooling tunnel, or cutting machine—must be aligned in a logical flow sequence. Machines should be placed on a level, non-slip surface with adequate spacing to allow for cleaning access, operator mobility, and future maintenance.
After positioning, the mechanical assembly begins. Connectors, fasteners, and modular attachments must be secured per the equipment manufacturer’s guidelines. Follow detailed checklists to confirm each component is correctly attached and functions freely without resistance.
Safety checks are essential before powering any machine. Verify that emergency stop switches are functional, belts and chains are properly tensioned, and guarding is in place to protect operators from moving parts. All electrical connections should be handled by certified technicians to ensure compliance with food industry safety standards.
Once assembled, the line should undergo calibration and trial runs. These tests help fine-tune settings such as mixing speeds, forming thickness, conveyor speeds, and cutting dimensions. For instance, if bars are too soft when cut, adjustments to cooling time or forming pressure may be necessary.
As food manufacturing technician Daniel Carter advises, “The trial run is not just a formality—it’s your opportunity to align machine output with your product expectations before scaling full production.”
By following structured installation procedures and performing thorough trial operations, your nutrition bar equipment will be set up for efficient, reliable production. Skipping or rushing these steps can lead to misalignments, product loss, or equipment failure down the line.
If the above introduction makes you interested in the nutritional bar production line and want to find a supplier, I will introduce it to you next.
Recommended Company
Shandong Loyal Industrial Co.,Ltd. Is a Manufacturer Of Snacks Extruder Machine , Industrial Microwave Oven , Corn Flakes Production Line , And a Standing Director Of China Food And Drying Equipment Industry Association.
The Self-developed Twin-screw Extruder And Single-screw Equipment of Shandong Loyal Machinery Have Been Used In Production: Puffed Snack Food, Breakfast Cereal Corn Flakes, Fried Pasta, Bread Crumbs, Fruit Chips, Baby Food, Textured Soy Protein (tsp) Food, Fish Feed And Pet Food. a Variety of Snack Production Line Supporting Products.at The Same Time, The Batching, Drying, Flaking, Baking, Frying And Spraying Equipment Matching The Twin-screw Extrusion System Have All Achieved Independent Design And Production.
Our Extrusion System Is Widely Used In: Puffed Snack Foods, Breakfast Cereals, Vegetable Protein Meat Products, Soy Based Nutrition Bars, Reconstituted Rice, Grain Nutrition Powder, Modified Starch, Starch-based Sticky Music Children's Educational Toys, Degradable Starch-based Packaging Filling Materials, Bread Crumbs And Other Food Additives, Pet Food, Aquatic Feed, Biology And Chemical Industries.
Customer-specific Food Processing Plant Project Solutions
As one of the leading manufacturers of food processing equipment, we are always searching for new solutions that benefit our snack food customers. Our experienced frying engineers always find the optimal solution for your industrial batch and continuous frying system line application. That's why we also develop, design and produce custom fried snack production line.
Close collaboration with our customer is important to us even in the early development phase. No matter what the special requirements of instant noodles production line, snack food extruder machine, pasta production line application, we can develop a custom made food processing equipment to match your needs.
Loyal have a unique and efficient industrial continuous frying equipment for snack food extruder machine that provides the right crunch and desired moisture level.
The Industrial Microwave Sterilization Defrosting Drying Machine can be designed as a dry powder dosing system and a wet slurry dosing system as required.
Some snacks can also be fried according to taste requirements, and we also provide Fried Snack Production Line for the processing and packaging of fried extruded snacks.
Loyal Food Production Line meet the needs of customers to obtain snack food that meet the needs.
In ovens or drying units, electric or gas can be used as heating sources.
Loyal have a unique and efficient industrial continuous frying equipment for snack food extruder machine that provides the right crunch and desired moisture level.
The Industrial Microwave Sterilization Defrosting Drying Machine can be designed as a dry powder dosing system and a wet slurry dosing system as required.
Some snacks can also be fried according to taste requirements, and we also provide Fried Snack Production Line for the processing and packaging of fried extruded snacks.
About packaging and after-sales service
Packing: Plastic Film Suitable For Ocean Carriage
Technical Support: The customer can inform machine related problems to us via telephone, email or fax. All information will be recorded and will be reported to the After-sale Service team. Meanwhile, the sales person will be tracking the case until problem solved.
Service Team: We have a professional After-sale Service team including10 professional engineers with at least 6 years working experience. They can handle technical consultation about manufacturing process, maintenance, fault diagnosis and troubleshooting, etc.
After-sale Service available :1.Check & test before delivery 2.Instruction for installation 3.On site commissioning 4.Repair & maintenance
After the receipt the advanced payment, we will provide allocation chart at the buyer’s request. When effect the shipment, we’ll provide operation manual, etc. in English.
Reference
The following are five authoritative foreign literature websites in the field of Industrial food machinery:
1. Food Engineering Magazine
Website: https://www.foodengineeringmag.com/
2.Food Processing Magazine
Website: https://www.foodprocessing.com/
3.Journal of Food Engineering
Website:https://www.journals.elsevier.com/journal-of-food-engineering
4. Food Manufacturing Magazine
Website:https://www.foodmanufacturing.com/
5. International Journal of Food Science & Technology
Website:https://onlinelibrary.wiley.com/