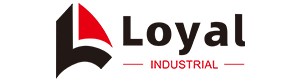
- Shandong Loyal Industrial Co.,Ltd.
- Macaroni Production Machine Instant Noodle Machine Biscuit Making Machine

Home> Company News> Everything you Need to Know About Food Processing Machine

Everything you Need to Know About Food Processing Machine
2024-04-15 17:37:26Introduction to Food Processing Machines
Food processing machines play a pivotal role in the food industry, facilitating the transformation of raw ingredients into finished products ready for consumption. These machines encompass a wide range of equipment designed to perform various tasks such as mixing, grinding, cooking, and packaging. From small-scale operations to large industrial facilities, food processing machines are essential for ensuring efficiency, consistency, and quality in food production processes.
Food processing machines come in diverse forms to cater to different needs and production scales. They can range from simple, manually operated machines used in artisanal food production to highly automated systems utilized in large-scale manufacturing plants. Regardless of their complexity, these machines are engineered to meet stringent food safety and hygiene standards while maximizing productivity and minimizing waste.
Key components of food processing machines include motors, gears, blades, conveyors, and control systems, all working together to perform specific tasks efficiently and accurately. Advanced technologies such as sensors, robotics, and artificial intelligence are increasingly integrated into modern food processing machines to enhance performance, precision, and automation.
In summary, food processing machines are indispensable assets in the food industry, driving innovation, efficiency, and quality throughout the production process. Their versatility, reliability, and capability to handle various food products make them essential tools for meeting the demands of today's dynamic food market.
Evolution of Food Processing Technology
The evolution of food processing technology has been characterized by continuous innovation and advancements aimed at improving efficiency, product quality, and safety. Over the years, significant developments have transformed the landscape of food processing, revolutionizing how food is produced, preserved, and distributed.
Historically, food processing was predominantly manual labor, relying on traditional methods such as grinding, pounding, and fermenting to transform raw ingredients into edible products. With the advent of industrialization, mechanical and electrical technologies were introduced, leading to the development of steam-powered machines and electrically operated equipment for mass food production.
In the mid-20th century, the food processing industry witnessed the emergence of modern technologies such as pasteurization, refrigeration, and canning, which revolutionized food preservation and storage. This period also saw the introduction of specialized machines for tasks like slicing, dicing, and packaging, enabling greater efficiency and standardization in food production processes.
In recent decades, the integration of computerization, automation, and digitalization has further propelled the evolution of food processing technology. Advanced machinery equipped with sensors, actuators, and smart control systems enable precise control over processing parameters, resulting in improved product consistency and quality. Furthermore, the adoption of technologies such as high-pressure processing (HPP), ultraviolet (UV) sterilization, and microwave heating has enhanced food safety and extended shelf life without compromising nutritional value or sensory attributes.
Looking ahead, the future of food processing technology is poised for further innovation and disruption. Emerging trends such as 3D food printing, blockchain traceability, and sustainable packaging are expected to reshape the industry, driving efficiency, transparency, and sustainability across the entire food supply chain. As technology continues to evolve, food processing will remain at the forefront of innovation, addressing the challenges and opportunities of an ever-changing global food market.
Types of Food Processing Machines
Food processing machines encompass a wide range of equipment designed to handle various stages of food production, from raw ingredients to finished products. These machines play a crucial role in the food industry by automating tasks, ensuring consistency, and enhancing efficiency. Here are some common types of food processing machines:
1. Mixers and Blenders: Mixers and blenders are used to combine ingredients thoroughly, whether for batter, dough, sauces, or other food products. They come in various sizes and configurations to accommodate different production needs.
2. Cutting and Slicing Equipment: Cutting and slicing machines are essential for portioning, dicing, and slicing ingredients such as fruits, vegetables, meats, and cheeses. They improve precision and uniformity in food preparation.
3. Grinding and Milling Machinery: Grinding and milling machines are utilized to reduce the size of food ingredients, such as grains, spices, and nuts, into smaller particles or powders. They are commonly used in the production of flour, spices, and other food powders.
4. Cooking and Baking Appliances: Cooking and baking appliances include ovens, fryers, steamers, and grills, which are used to apply heat and cook food products. They ensure proper cooking and enhance the flavor and texture of the final products.
5. Packaging Machinery: Packaging machinery encompasses equipment for filling, sealing, labeling, and packaging food products into containers or packages. These machines ensure product safety, freshness, and shelf-life extension.
Factors to Consider When Selecting Better Equipment
When choosing between food processing machines from different manufacturers, such as LOYAL and Baker Perkins, several factors must be evaluated to ensure optimal performance and suitability for specific production needs. Here's a simple comparison in terms of performance, reliability, and other aspects:
Aspect |
LOYAL |
Baker Perkins |
Performance |
High efficiency and throughput rates, suitable for medium-scale operations. |
Renowned for precision and consistency in product quality, ideal for large-scale production facilities. |
Factory Space |
Compact design with a smaller footprint, suitable for limited space environments. |
Requires more floor space due to larger equipment size and capacity, ideal for spacious production facilities. |
Maintenance |
Easy maintenance with accessible components and user-friendly design. |
Requires regular maintenance due to complex machinery and larger equipment size. |
Customization |
Offers customizable configurations to accommodate various processing requirements. |
Limited customization options but provides standard configurations suitable for most applications. |
Cost |
Offers competitive pricing and low operating costs, providing excellent value for money. |
Higher initial investment but offers long-term cost savings through efficient operation and durability. |
By considering these factors, manufacturers can make informed decisions to select the food processing equipment that best meets their specific production requirements and operational objectives.
Components and Features of Modern Machines
Modern food processing machines incorporate a variety of components and features designed to enhance efficiency, productivity, and safety in industrial food production settings. Understanding these components and features is essential for selecting the most suitable equipment for specific processing needs.
One crucial component of modern food processing machines is the control system, which governs the operation of the machine and ensures precise control over processing parameters such as temperature, pressure, and speed. Advanced control systems utilize sensors and actuators to monitor and adjust process variables in real-time, optimizing performance and product quality.
Another essential feature is the material handling system, which facilitates the movement of ingredients and products throughout the processing line. Material handling systems may include conveyors, elevators, and hoppers, which are designed to transport materials efficiently and minimize contamination risks.
Modern food processing machines are equipped with safety features to protect operators and ensure compliance with industry regulations. These features may include emergency stop buttons, safety interlocks, and guarding systems to prevent accidents and injuries during operation.
Sanitation and hygiene are paramount in food processing, and modern machines are designed with easy-to-clean surfaces and sanitary design principles. Smooth, stainless steel construction, removable components, and automated cleaning systems help reduce the risk of microbial contamination and ensure product integrity.
Operational Insights: Maximizing Efficiency
Maximizing efficiency is a primary objective in industrial food processing, and operational insights play a crucial role in achieving this goal. By understanding key operational factors and implementing best practices, manufacturers can enhance productivity, minimize downtime, and improve overall efficiency in food processing operations.
One important aspect of operational efficiency is equipment maintenance and optimization. Regular maintenance schedules, including preventive maintenance and calibration of equipment, help ensure reliable operation and extend the lifespan of machinery. Additionally, optimizing equipment settings and adjusting processing parameters based on product requirements can improve efficiency and reduce waste.
Another key factor is workforce training and skill development. Well-trained operators who understand equipment operation and safety protocols are better equipped to troubleshoot issues, operate machinery efficiently, and minimize errors during production. Investing in training programs and providing ongoing education opportunities for employees can yield significant improvements in operational efficiency.
In conclusion, maximizing efficiency in food processing requires a holistic approach that addresses equipment maintenance, workforce training, data-driven decision-making, and lean manufacturing principles. By focusing on these operational insights, manufacturers can optimize productivity, reduce costs, and enhance overall performance in food processing operations.
Safety Measures in Food Processing
Food processing involves various steps and machinery, posing potential risks to workers and consumers if proper safety measures are not in place. Implementing effective safety protocols is essential to mitigate these risks and ensure the well-being of all involved in the food processing industry.
First and foremost, ensuring the proper training of personnel is crucial for maintaining a safe working environment. Employees should receive comprehensive training on equipment operation, handling hazardous materials, and emergency procedures. Regular training sessions and refresher courses can reinforce safety protocols and keep employees informed about the latest safety standards and regulations.
conducting thorough risk assessments of food processing operations is essential for identifying potential hazards and implementing appropriate control measures. This includes assessing machinery hazards, such as moving parts, sharp edges, and hot surfaces, and implementing safeguards such as machine guards, safety interlocks, and emergency stop buttons.
maintaining a clean and sanitary work environment is critical for preventing food contamination and ensuring product safety. Regular cleaning and sanitation of equipment and processing areas help reduce the risk of microbial contamination and cross-contamination. Implementing strict hygiene practices, such as handwashing, personal protective equipment (PPE) usage, and proper waste disposal, further contribute to maintaining a safe and hygienic workplace.
In conclusion, prioritizing safety measures in food processing is essential for protecting workers, consumers, and the reputation of food businesses. By implementing comprehensive training programs, conducting risk assessments, and maintaining a clean work environment, food processing facilities can minimize hazards and ensure the production of safe and high-quality food products.
Quality Assurance and Control Methods
Quality assurance and control are critical aspects of food processing, ensuring that products meet safety and quality standards before reaching consumers. Several methods and practices are employed in the food industry to maintain quality throughout the production process and minimize the risk of product defects or contamination.
One essential aspect of quality assurance is implementing Good Manufacturing Practices (GMPs), which are guidelines and procedures designed to ensure the consistent production of safe and high-quality food products. GMPs cover various aspects of food processing, including facility cleanliness, equipment maintenance, personnel hygiene, and product labeling, to minimize the risk of contamination and ensure product integrity.
Implementing Hazard Analysis and Critical Control Points (HACCP) systems is crucial for identifying and controlling potential hazards in food processing. HACCP involves systematically assessing food production processes, identifying critical control points where hazards can be prevented, monitored, or controlled, and implementing corrective actions as needed to ensure food safety.
Conducting regular quality inspections and product testing is essential for verifying product quality and compliance with regulatory standards. This includes visual inspections, sensory evaluations, and laboratory testing for microbiological, chemical, and physical parameters to detect any deviations from quality standards and ensure product safety.
Overall, quality assurance and control methods play a vital role in ensuring the safety, integrity, and consistency of food products. By implementing GMPs, HACCP systems, and rigorous quality inspections, food processing facilities can maintain consumer confidence and uphold their reputation for producing safe and high-quality food products.
Environmental Impact and Sustainability Practices
In the realm of food processing machinery, environmental impact and sustainability practices have become increasingly vital considerations. As the global demand for food continues to rise, so does the need for sustainable solutions to mitigate environmental harm. Several strategies are being employed within the industry to address these concerns and promote eco-friendly practices.
One significant area of focus is the reduction of energy consumption in food processing machines. Manufacturers are developing and implementing energy-efficient technologies to minimize electricity usage and decrease carbon emissions. This includes the utilization of advanced motors, variable frequency drives, and heat recovery systems to optimize energy efficiency throughout the production process.
Waste reduction and recycling initiatives play a crucial role in enhancing sustainability in food processing. Companies are implementing measures to minimize waste generation and maximize the reuse and recycling of materials. This includes the adoption of closed-loop systems, where waste products are repurposed as inputs for other processes, thus reducing landfill waste and conserving resources.
Sustainable sourcing practices are gaining traction in the food processing machinery industry. Manufacturers are increasingly prioritizing suppliers that adhere to ethical and environmentally friendly practices throughout the supply chain. This includes sourcing raw materials from sustainable sources, minimizing water usage, and promoting fair labor practices.
Environmental impact and sustainability practices are integral to the future of the food processing machinery industry. By embracing energy-efficient technologies, waste reduction initiatives, and sustainable sourcing practices, manufacturers can minimize their environmental footprint and contribute to a more sustainable food system.
Future Prospects and Innovations in the Industry
Looking ahead, the future of the food processing machinery industry is filled with exciting prospects and innovations. As technology continues to advance, new opportunities emerge to enhance efficiency, product quality, and sustainability. Several trends and developments are shaping the trajectory of the industry, driving innovation and opening up new avenues for growth.
One promising area of innovation is the integration of artificial intelligence (AI) and automation into food processing machinery. AI-powered systems can optimize production processes, improve quality control, and reduce waste by analyzing data in real-time and making data-driven decisions. This includes the use of predictive analytics to anticipate equipment failures and optimize production schedules for maximum efficiency.
Additionally, the development of smart sensors and Internet of Things (IoT) technology is revolutionizing food processing machinery. These sensors can monitor equipment performance, detect abnormalities, and provide real-time feedback to operators, enabling proactive maintenance and minimizing downtime. IoT-enabled devices also facilitate remote monitoring and control, allowing manufacturers to oversee operations from anywhere in the world.
There is a growing emphasis on the development of sustainable materials and manufacturing processes in the food processing machinery industry. Manufacturers are exploring alternative materials, such as biodegradable plastics and renewable resources, to reduce environmental impact and promote circular economy principles. Additionally, there is a focus on improving energy efficiency and reducing carbon emissions throughout the supply chain.
The future of the food processing machinery industry is bright, with innovations in technology, sustainability, and efficiency driving growth and progress. By embracing these advancements and staying ahead of emerging trends, manufacturers can position themselves for success in the evolving landscape of food processing.
Reference materials
1. Food Engineering Magazine
Website: [https://www.foodengineeringmag.com/]
2. Food Processing Magazine
Website: [https://www.foodprocessing.com/]
3. Institute of Food Technologists (IFT)
Website: [https://www.ift.org/]
4. American Society of Agricultural and Biological Engineers (ASABE)
Website: [https://www.asabe.org/]
5. European Federation of Food Science and Technology (EFFoST)
Website: [https://effost.org/]
FAQs: Common Questions about Food Processing Machines
1. What is a food processing machine?
A food processing machine is a piece of equipment used in the food industry to perform various tasks such as mixing, cutting, cooking, and packaging food products.
2. What types of food processing machines are there?
There are various types of food processing machines, including mixers, slicers, ovens, fryers, packaging machines, and more, each designed to perform specific functions in food production.
3. What are the benefits of using food processing machines?
Food processing machines offer several benefits, including increased efficiency, consistency in product quality, labor savings, and the ability to handle large volumes of food production.
4. How do I choose the right food processing machine for my needs?
When selecting a food processing machine, consider factors such as the type of food product you're processing, production volume, available space, budget, and any specific requirements for processing techniques or features. Consulting with industry experts and conducting thorough research can help in making an informed decision.