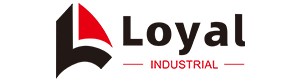
- Shandong Loyal Industrial Co.,Ltd.
- Macaroni Production Machine Instant Noodle Machine Biscuit Making Machine

Home> Company News> The Ultimate Pet Food Processing Line Guide to 2024

The Ultimate Pet Food Processing Line Guide to 2024
2024-04-22 15:53:04Introduction to Pet Food Processing Line Technology
Pet food processing lines represent a critical aspect of the modern pet food industry. These advanced technological systems encompass a range of equipment designed to efficiently produce high-quality pet food products. Pet food processing lines typically include machinery for mixing, grinding, extruding, drying, and packaging pet food products. The integration of automated systems and precision control mechanisms ensures consistency in product quality and production efficiency.
Pet food processing lines are equipped with specialized machinery tailored to handle various types of ingredients, including meat, grains, vegetables, and supplements. These ingredients are carefully combined and processed to create balanced and nutritious pet food formulations. The utilization of advanced processing technologies, such as extrusion and thermal processing, enables manufacturers to achieve optimal texture, palatability, and nutrient retention in the final products.
The development of pet food processing lines has revolutionized the pet food industry, allowing manufacturers to meet the growing demand for pet food products worldwide. These sophisticated systems have significantly improved production capacity, product consistency, and cost-effectiveness in pet food manufacturing. With ongoing advancements in technology and equipment design, pet food processing lines continue to evolve to meet the ever-changing needs and preferences of pet owners and their furry companions.
Historical Evolution of Pet Food Processing Equipment
The history of pet food processing equipment traces back to the early 20th century when commercial pet food production began to gain traction. Initially, pet food was primarily produced using simple methods such as cooking and canning. However, as the pet food industry expanded, there arose a need for more efficient and scalable processing solutions.
In the mid-20th century, the advent of extrusion technology revolutionized the pet food manufacturing process. Extruders became the cornerstone of pet food processing equipment, allowing for the production of a wide range of pet food products with consistent quality and texture. This marked a significant milestone in the evolution of pet food processing, enabling manufacturers to meet the growing demand for nutritious and palatable pet food formulations.
Throughout the latter half of the 20th century and into the 21st century, continuous advancements in engineering and technology have propelled the development of pet food processing equipment. Innovations such as automated mixing systems, precision extrusion dies, and sophisticated drying techniques have further enhanced the efficiency and productivity of pet food manufacturing.
Today, pet food processing equipment encompasses a diverse range of machinery tailored to meet the specific requirements of different types of pet food products. From kibble and canned food to treats and supplements, manufacturers have access to a comprehensive suite of processing solutions designed to optimize production processes and product quality. The ongoing evolution of pet food processing equipment continues to drive innovation and competitiveness in the pet food industry, ensuring that pet owners have access to a wide variety of nutritious and appealing food options for their beloved companions.
Understanding the Components of a Pet Food Processing Line
A pet food processing line comprises several essential components that work together seamlessly to produce high-quality pet food products. These components include:
1. Raw Material Handling Systems: This component involves the reception and storage of raw materials such as grains, meat, vegetables, and additives. Raw materials are stored in silos or bins and transported to the processing line as needed.
2. Grinding and Milling Equipment: Raw materials often require grinding or milling to achieve the desired particle size. This step facilitates better mixing and extrusion later in the process.
3. Mixing and Blending Machines: Mixing and blending equipment ensure homogeneity of the pet food mixture. Ingredients are accurately measured and mixed to create a consistent blend before extrusion.
4. Extruders: Extrusion is a key process in pet food production. Extruders use a combination of heat, pressure, and mechanical shear to cook the ingredients and form the desired shapes of pet food products.
5. Drying and Cooling Systems: After extrusion, pet food products need to be dried to remove excess moisture and cooled to ambient temperature. Drying and cooling systems ensure proper texture and shelf stability of the final products.
6. Coating and Flavoring Equipment: Some pet food products may require coating with fats, oils, or flavorings to enhance palatability and nutritional value. Coating and flavoring equipment add these ingredients in a controlled manner.
7. Packaging Machinery: Packaging machinery is responsible for filling, sealing, and labeling pet food products into bags, cans, or pouches. This component ensures proper packaging for storage, distribution, and retail.
Choose the Right Pet Food Processing Line
When selecting a pet food processing line, it's crucial to consider various factors to meet production requirements efficiently. Let's compare the machines from LOYAL and Buhler, two renowned manufacturers in the industry:
Aspect |
LOYAL Pet Food Processing Line |
Buhler Pet Food Processing Line |
Technology and Innovation |
Utilizes advanced extrusion technology |
Known for innovative solutions and engineering |
Customization Options |
Offers customizable configurations |
Provides tailored solutions for specific needs |
Production Capacity |
Capable of high-volume production |
Suitable for both small-scale and large-scale |
Quality and Durability |
Constructed with high-quality materials |
Renowned for durability and long lifespan |
Maintenance and Support |
Comprehensive after-sales support and service |
Reliable technical assistance and maintenance |
Both LOYAL and Buhler pet food processing lines have their strengths and are suitable for different production requirements. Companies should evaluate their specific needs and preferences to choose the most suitable option for their pet food manufacturing operations.
Innovations in Mixing and Blending for Pet Food Production
In the realm of pet food processing lines, mixing and blending play pivotal roles in ensuring the quality and consistency of the final product. Manufacturers continuously innovate in this area to enhance efficiency and meet evolving consumer demands.
One notable innovation lies in the development of precision mixing technologies. These systems leverage advanced algorithms and sensors to precisely control ingredient proportions, resulting in a more uniform blend. By optimizing the mixing process, manufacturers can achieve greater consistency in texture, flavor, and nutritional content across batches.
Additionally, the integration of automation and robotics has revolutionized mixing and blending operations in pet food processing lines. Automated systems can handle large volumes of ingredients with precision and speed, reducing the risk of human error and ensuring consistent product quality. Moreover, robotics enable the customization of mixing profiles to accommodate varying recipes and formulations, offering greater flexibility in production.
Furthermore, the use of advanced mixing vessels and equipment has contributed to improved efficiency and hygiene in pet food processing lines. These vessels are designed to minimize product waste and contamination risk while facilitating thorough mixing. Moreover, innovations in cleaning-in-place (CIP) systems allow for more efficient sanitation procedures, ensuring compliance with strict quality and safety standards.
Quality Control and Assurance Measures in Pet Food Processing Lines
Quality control and assurance are paramount in pet food processing lines to uphold product integrity and meet regulatory requirements. Manufacturers employ rigorous measures throughout the production process to ensure the safety and quality of pet food products.
One key aspect of quality control is the implementation of comprehensive testing protocols for raw materials and finished products. This includes screening for contaminants, such as pathogens and toxins, as well as analyzing nutritional composition and consistency. Advanced analytical techniques, such as chromatography and mass spectrometry, enable precise and reliable testing, ensuring compliance with industry standards.
Moreover, manufacturers utilize sophisticated monitoring systems to oversee various aspects of production, including temperature, humidity, and processing parameters. Real-time data analytics provide insights into process performance and enable proactive intervention to mitigate potential issues. Additionally, continuous monitoring helps maintain product consistency and traceability throughout the supply chain.
Furthermore, traceability systems play a crucial role in quality assurance by enabling quick and accurate identification of ingredients and finished products. By implementing robust tracking and labeling mechanisms, manufacturers can effectively manage recalls and address any quality concerns in a timely manner. This enhances consumer confidence in the safety and reliability of pet food products.
Automation and Robotics Integration in Pet Food Manufacturing
Automation and robotics integration has revolutionized the pet food manufacturing industry, streamlining processes and enhancing efficiency. Pet food processing lines are increasingly incorporating advanced robotics to handle various tasks, from ingredient handling to packaging.
One of the key benefits of automation in pet food processing lines is increased productivity. By utilizing robots for repetitive tasks such as ingredient mixing, extrusion, and packaging, manufacturers can significantly reduce production time while maintaining consistency and quality.
Moreover, robotics integration ensures precision and accuracy in the manufacturing process. Automated systems can measure ingredients with exact proportions, resulting in consistent product quality and nutritional content in every batch of pet food produced. This level of precision is crucial for meeting regulatory standards and consumer expectations.
Additionally, robotics integration enhances safety in pet food manufacturing facilities. By replacing manual labor with robotic systems for tasks like heavy lifting and handling hazardous materials, the risk of workplace accidents and injuries is significantly reduced. This not only protects workers but also minimizes downtime and production delays.
Automation and robotics integration enable manufacturers to adapt quickly to changing market demands. With customizable robotic systems, pet food processing lines can easily adjust production volumes and product variations without lengthy retooling processes. This flexibility is essential for meeting the dynamic needs of the pet food market while maintaining operational efficiency.
Energy Efficiency and Sustainability Practices in Pet Food Processing
Energy efficiency and sustainability have become increasingly important considerations in pet food processing, driven by both environmental concerns and cost-saving initiatives. Pet food processing lines are implementing various practices to minimize energy consumption and reduce environmental impact throughout the manufacturing process.
One strategy employed by pet food manufacturers is the optimization of equipment and processes to reduce energy usage. Modern pet food processing lines utilize energy-efficient machinery and technologies, such as high-speed extruders and advanced drying systems, to minimize energy wastage while maximizing productivity.
Sustainability practices extend beyond energy efficiency to include waste reduction and resource conservation. Pet food processing lines are implementing measures such as recycling and composting to minimize waste generation and optimize resource utilization. By repurposing by-products and excess materials, manufacturers can reduce their environmental footprint and contribute to a circular economy.
Moreover, sustainable packaging solutions are being adopted to further minimize environmental impact. From biodegradable packaging materials to lightweight designs that reduce transportation emissions, pet food manufacturers are exploring innovative packaging options that prioritize sustainability without compromising product quality or safety.
Safety Standards and Regulations for Pet Food Processing Equipment
Pet food processing equipment must adhere to stringent safety standards and regulations to ensure the quality and safety of pet food products. These standards encompass various aspects of equipment design, operation, and maintenance to mitigate risks associated with food processing.
Firstly, equipment manufacturers must comply with international standards such as ISO 22000, which outlines food safety management systems. This standard ensures that pet food processing equipment is designed and manufactured in a manner that prevents contamination, maintains hygiene, and ensures traceability throughout the production process.
Additionally, equipment used in pet food processing must meet specific regulatory requirements set forth by government agencies. For example, in the United States, the Food and Drug Administration (FDA) regulates pet food manufacturing under the Federal Food, Drug, and Cosmetic Act (FFDCA) and the Food Safety Modernization Act (FSMA). These regulations cover aspects such as ingredient sourcing, processing conditions, and labeling to safeguard pet food quality and consumer health.
Furthermore, safety standards address the operational aspects of pet food processing equipment, including proper installation, calibration, and maintenance procedures. Regular inspections and audits are conducted to verify compliance with safety standards and identify any potential hazards or deficiencies that may compromise product integrity.
Future Trends and Predictions in Pet Food Processing Line Technology
The pet food processing industry is witnessing significant advancements driven by technological innovation and evolving consumer preferences. Several trends and predictions are shaping the future of pet food processing line technology.
One notable trend is the adoption of automation and robotics in pet food manufacturing. Automated systems streamline production processes, enhance efficiency, and reduce labor costs. Robotics are increasingly utilized for tasks such as ingredient handling, mixing, and packaging, leading to improved consistency and quality control in pet food production.
Another emerging trend is the utilization of data analytics and artificial intelligence (AI) in pet food processing lines. By leveraging data from sensors and monitoring devices, manufacturers can optimize production parameters, predict equipment failures, and ensure real-time quality monitoring. AI algorithms can analyze vast amounts of data to identify patterns and optimize formulations for enhanced nutritional value and palatability.
Moreover, there is a growing emphasis on sustainability and environmental responsibility in pet food processing. Manufacturers are exploring eco-friendly packaging materials, reducing water and energy consumption, and implementing waste reduction strategies to minimize their carbon footprint.
Personalized nutrition is gaining traction in the pet food industry, driven by advancements in genomic research and pet health monitoring devices. Pet owners are seeking tailored diets that address their pets' specific nutritional needs and health concerns, leading to the development of customized pet food formulations.
References
1. Food Engineering Magazine: www.foodengineeringmag.com
2. Food Processing Technology: www.foodprocessing-technology.com
3. International Food Information Council (IFIC) Foundation: www.foodinsight.org
4. Food Safety Magazine: www.foodsafetymagazine.com
5. American Society of Agricultural and Biological Engineers (ASABE): www.asabe.org