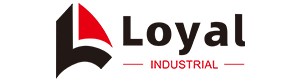
- Shandong Loyal Industrial Co.,Ltd.
- Macaroni Production Machine Instant Noodle Machine Biscuit Making Machine

Home> Company News> Everything you Need to Know About Dog Food Equipment

Everything you Need to Know About Dog Food Equipment
2024-04-22 16:03:53Introduction to Dog Food Equipment Industry Trends
In recent years, the dog food equipment industry has experienced significant growth and evolution, driven by changing consumer preferences, technological advancements, and regulatory requirements. One notable trend in the industry is the increasing demand for automated dog food production systems. Manufacturers are increasingly adopting automated machinery and equipment to streamline operations, improve efficiency, and meet the growing demand for high-quality dog food products.
Another trend in the dog food equipment industry is the emphasis on food safety and quality assurance. With heightened awareness of foodborne illnesses and contamination risks, manufacturers are investing in equipment that incorporates advanced sanitation and hygiene features. This includes equipment with easy-to-clean designs, antimicrobial coatings, and integrated quality control measures to ensure the safety and integrity of dog food products.
Additionally, sustainability is becoming a key focus in the dog food equipment industry. Manufacturers are developing equipment and processes that minimize waste, conserve energy, and reduce environmental impact. This includes the use of eco-friendly materials, energy-efficient technologies, and recycling and waste management solutions throughout the production process.
The dog food equipment industry is undergoing significant transformation in response to shifting consumer preferences, technological advancements, and sustainability concerns. Manufacturers are embracing automation, enhancing food safety measures, and prioritizing sustainability to meet the evolving demands of the market.
Key Components of Modern Dog Food Processing Machinery
Modern dog food processing machinery comprises several key components that work together to transform raw ingredients into finished dog food products. One essential component is the extruder, which plays a central role in the production of dry kibble and treats. Extruders use a combination of heat, pressure, and mechanical action to cook and shape the dough-like mixture of ingredients into uniform pieces.
Mixers and blenders are another crucial component of dog food processing machinery. These machines are responsible for thoroughly mixing and blending the various ingredients, ensuring uniform distribution of nutrients, flavors, and textures throughout the final product. Mixers and blenders come in various types, including paddle mixers, ribbon mixers, and tumbling mixers, each suited to different mixing requirements.
Dryers and ovens are essential components in the production of dry dog food products. These machines remove moisture from the product through evaporation, ensuring a longer shelf life and crispy texture. Ovens also play a role in the cooking process, further enhancing the flavor and palatability of the final product.
Packaging equipment is another key component of modern dog food processing machinery. Packaging machines automate the process of filling, sealing, and labeling dog food products, ensuring efficiency and consistency in packaging. These machines come in various forms, including vertical form-fill-seal machines, pouch fillers, and cartoners, each tailored to different packaging needs and formats.
Modern dog food processing machinery comprises extruders, mixers, blenders, dryers, ovens, and packaging equipment, among other components. These machines work together seamlessly to produce high-quality dog food products efficiently and consistently, meeting the needs and preferences of pet owners and their furry companions.
Benefits of Automated Dog Food Production Systems
Automated dog food production systems offer numerous advantages for manufacturers seeking to streamline their operations and improve efficiency. One significant benefit is increased productivity. By automating various stages of the production process, such as mixing, extrusion, and packaging, manufacturers can significantly increase their output while minimizing labor costs and human error.
Moreover, automated systems enhance consistency and quality control. With precise control over parameters such as ingredient ratios, cooking temperatures, and mixing times, automated equipment ensures that each batch of dog food meets the same high standards of quality and nutritional content. This consistency is essential for maintaining customer satisfaction and brand reputation.
Additionally, automated dog food production systems improve safety and hygiene in the manufacturing environment. By minimizing human interaction with raw ingredients and reducing the risk of contamination, automated equipment helps prevent foodborne illnesses and ensures compliance with stringent food safety regulations. This not only protects consumers but also safeguards the reputation of the manufacturer.
Automated systems offer flexibility and scalability, allowing manufacturers to adapt quickly to changing market demands and production requirements. With modular designs and customizable settings, automated equipment can easily accommodate variations in recipe formulations, batch sizes, and packaging formats. This agility enables manufacturers to stay competitive in a dynamic market landscape.
Types of Dog Food Extruders and Their Functions
Dog food extruders are essential pieces of equipment in the production of dry kibble and treats for canine companions. These machines utilize the extrusion process to transform raw ingredients into uniform, bite-sized pieces that are palatable and nutritious for dogs. There are several types of dog food extruders, each with its unique design and functionality.
Single-screw extruders are the most common type of dog food extruder and are widely used in the industry due to their simplicity and versatility. These extruders consist of a single rotating screw within a barrel, which conveys the raw ingredients forward while applying pressure and heat to cook and shape the product. Single-screw extruders are suitable for a wide range of formulations and production volumes.
Twin-screw extruders are another type of dog food extruder that offers enhanced mixing and cooking capabilities compared to single-screw extruders. These extruders feature two intermeshing screws within a barrel, which work together to knead, shear, and cook the ingredients more thoroughly. Twin-screw extruders are ideal for processing complex formulations and achieving precise texture and density control.
There are specialty extruders designed specifically for producing textured or high-meat dog food products. These extruders utilize unique die configurations and processing parameters to create products with specific shapes, textures, and nutritional profiles. Specialty extruders are often used to produce treats, chews, and premium dog food formulations that cater to discerning pet owners.
The Best Choice for Dog Food Equipment
When it comes to selecting dog food equipment, two prominent manufacturers stand out: LOYAL and Clextral. Let's compare their machines across various aspects:
Aspect |
LOYAL Dog Food Equipment |
Clextral Dog Food Equipment |
Technology |
Advanced automation technology |
Innovative processing technology |
Reliability |
Known for reliability and durability |
Renowned for robust performance |
Customization Options |
Offers customized solutions |
Provides versatile configurations |
Efficiency |
Optimized for maximum efficiency |
Designed for high productivity |
Maintenance |
Requires minimal maintenance |
Designed for easy maintenance |
Cost-effectiveness |
Provides excellent investment value |
Offers competitive pricing |
LOYAL's dog food equipment is renowned for its advanced automation technology, which streamlines the production process and enhances efficiency. Their machines are designed with precision and reliability, ensuring consistent performance throughout the production cycle. Moreover, LOYAL offers customization options, allowing manufacturers to tailor equipment to their specific needs and preferences.
On the other hand, Clextral's dog food equipment boasts innovative processing technology, delivering high-performance results. Their machines are versatile and adaptable, capable of handling various production requirements with ease. Additionally, Clextral equipment is designed for easy maintenance, minimizing downtime and optimizing productivity.
Quality Control Measures in Dog Food Processing Lines
Ensuring the quality and safety of dog food products is paramount in dog food processing lines. To maintain high standards of quality control, several measures are implemented throughout the production process.
First and foremost, ingredient sourcing plays a crucial role in quality control. Manufacturers must carefully select suppliers that provide high-quality, safe, and nutritious ingredients. Additionally, ingredients undergo rigorous testing and inspection upon arrival to ensure they meet specified standards for purity and quality.
Stringent sanitation and hygiene practices are enforced in dog food processing facilities to prevent contamination and ensure product safety. Equipment and production areas are regularly cleaned and sanitized according to established protocols to minimize the risk of microbial contamination.
Quality control measures extend to every stage of the production process, from mixing and blending to extrusion and packaging. Automated systems and sensors monitor critical parameters such as temperature, moisture, and ingredient ratios to maintain consistency and product quality.
Finished products undergo thorough testing and analysis to verify nutritional content, taste, texture, and safety. Samples are taken from each batch and subjected to laboratory testing to ensure compliance with regulatory requirements and industry standards.
Packaging Solutions for Dog Food Products
Packaging plays a vital role in preserving the freshness, quality, and safety of dog food products. With the increasing demand for convenience and sustainability, manufacturers are exploring various packaging solutions tailored to the unique needs of dog food products.
One common packaging solution for dog food products is flexible packaging, such as pouches and bags. Flexible packaging offers several advantages, including lightweight, space-saving, and cost-effective options. Additionally, flexible packaging can be customized with features like resealable zippers and tear-off tabs, enhancing convenience for pet owners.
Another popular packaging solution for dog food products is rigid packaging, such as cans and tubs. Rigid packaging provides excellent protection against moisture, oxygen, and other environmental factors, ensuring the freshness and quality of the product. Moreover, rigid packaging offers enhanced shelf visibility and branding opportunities, allowing manufacturers to differentiate their products in the market.
Vacuum packaging is often employed in dog food production lines to extend the shelf life of products by removing air from the packaging. This helps prevent oxidation and spoilage, preserving the flavor and nutritional integrity of the dog food. Vacuum packaging also reduces the need for preservatives, making it a popular choice among pet owners seeking natural and wholesome options for their pets.
Energy Efficiency in Dog Food Processing Equipment
Energy efficiency is a crucial consideration in the design and operation of dog food processing equipment. As energy costs continue to rise and environmental concerns grow, manufacturers are increasingly focused on optimizing the energy efficiency of their equipment to reduce costs and minimize their carbon footprint.
One key aspect of energy efficiency in dog food processing equipment is the use of advanced technologies such as variable frequency drives (VFDs) and energy-efficient motors. These technologies allow for precise control of motor speed and power consumption, reducing energy waste during operation. Additionally, modern equipment designs incorporate features such as insulation and heat recovery systems to minimize energy losses and maximize efficiency.
Furthermore, manufacturers are exploring alternative energy sources such as solar and wind power to supplement or replace traditional energy sources. By harnessing renewable energy, dog food processing facilities can reduce their reliance on fossil fuels and lower their carbon footprint. Additionally, energy management systems and monitoring tools are being implemented to track energy usage and identify opportunities for further efficiency improvements.
Energy efficiency is a key consideration in the design, operation, and maintenance of dog food processing equipment. By incorporating advanced technologies, alternative energy sources, and efficient operating practices, manufacturers can minimize energy consumption, reduce costs, and minimize their environmental impact.
Safety Features and Regulations for Dog Food Machinery
Safety is paramount in the design, operation, and maintenance of dog food machinery to ensure the well-being of workers and the quality of the final product. There are stringent safety features and regulations in place to govern the manufacturing and use of dog food equipment.
First and foremost, dog food machinery must comply with industry-specific safety standards and regulations set forth by regulatory bodies such as the Occupational Safety and Health Administration (OSHA) and the Food and Drug Administration (FDA). These standards outline requirements for equipment design, installation, maintenance, and operation to ensure worker safety and product quality. Manufacturers are required to adhere to these standards and undergo rigorous testing and certification processes to ensure compliance.
One of the key safety features of dog food machinery is the incorporation of guards and enclosures to prevent access to moving parts and hazardous areas. Guards are designed to shield operators from rotating blades, conveyor belts, and other potential hazards, while enclosures provide a barrier to contain spills and debris. Emergency stop buttons and safety interlocks are also installed on machinery to immediately halt operations in the event of an emergency or malfunction, allowing workers to quickly shut down equipment and prevent accidents or injuries.
Additionally, regular maintenance and inspection of dog food machinery are essential to identify and address potential safety hazards. Manufacturers and operators must follow maintenance schedules and conduct thorough inspections to ensure that equipment is functioning properly and meets safety standards. By implementing robust safety features and adhering to regulations, manufacturers can create a safe working environment and minimize the risk of accidents or injuries in dog food production facilities.
Emerging Technologies in Dog Food Equipment Industry
The dog food equipment industry is experiencing rapid technological advancements, driven by the need for increased efficiency, sustainability, and product innovation. Several emerging technologies are poised to transform the landscape of dog food equipment and revolutionize the way dog food is produced.
One of the most significant emerging technologies in the dog food equipment industry is the use of automation and robotics. Automated systems are being integrated into various aspects of dog food production, from ingredient handling and mixing to packaging and palletizing. Robotics enable precise control and manipulation of materials, reducing human error and improving efficiency. Automated systems can also enhance safety by minimizing the need for manual labor in hazardous environments.
Advanced sensors and data analytics are being utilized to optimize the performance of dog food equipment and processes. Sensors can monitor parameters such as temperature, moisture, and pressure in real-time, allowing for precise control and adjustment of production variables. Data analytics algorithms analyze production data to identify trends, optimize processes, and predict equipment failures, enabling manufacturers to maximize efficiency and minimize downtime.
Additionally, 3D printing technology is being explored for the production of customized parts and components for dog food equipment. 3D printing enables manufacturers to create complex shapes and designs with precision, reducing lead times and production costs. This technology also facilitates rapid prototyping and customization, allowing for faster innovation and development of new equipment designs.
References
1. Food Engineering Magazine: www.foodengineeringmag.com
2. Food Processing Technology: www.foodprocessing-technology.com
3. International Food Information Council (IFIC) Foundation: www.foodinsight.org
4. Food Safety Magazine: www.foodsafetymagazine.com
5. American Society of Agricultural and Biological Engineers (ASABE): www.asabe.org