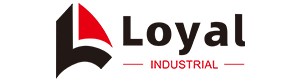
- Shandong Loyal Industrial Co.,Ltd.
- Macaroni Production Machine Instant Noodle Machine Biscuit Making Machine

Home> Company News> The Ultimate Guide to Corn Puffs Machine in 2024

The Ultimate Guide to Corn Puffs Machine in 2024
2024-04-22 16:27:40Introduction
In the dynamic landscape of food processing, the role of technology has become increasingly prominent, revolutionizing the way we produce and consume various food products. Among the many innovations in this realm, the corn puffs machine stands out as a cornerstone of modern snack production. As we delve into the intricacies of this fascinating piece of equipment, it becomes evident that understanding its capabilities, functionalities, and impact is essential for anyone involved in the food industry.
The year 2024 marks a significant juncture in the evolution of corn puff production, with advancements in technology driving efficiency, quality, and sustainability to new heights. In this comprehensive guide, we will explore every facet of the corn puffs machine, from its fundamental principles to its practical applications and future prospects. By the end of this journey, you will gain a profound understanding of how this remarkable machine shapes the landscape of snack manufacturing in the year 2024 and beyond.
Working Principle and Composition
Corn puffs machines, also known as puffing machines or puffing extruders, are essential equipment in the food processing industry, specifically in the production of corn-based snacks like puffed corn snacks. Understanding their working principle and composition is crucial for grasping their role in snack food production.
1. Working Principle:
Extrusion Process: The core principle behind corn puffs machines involves the extrusion process. Raw materials, typically corn grits or flour, are fed into the machine's barrel, where they undergo high temperature and pressure conditions.
Expansion and Puffing: As the raw materials move through the barrel, the combination of heat, pressure, and mechanical shear forces causes them to expand rapidly. This expansion results in the formation of the characteristic puffed texture of corn snacks.
2. Composition of Corn Puffs Machines:
Barrel: The barrel of the corn puffs machine is a cylindrical chamber where the extrusion process takes place. It is typically made of stainless steel and is divided into several sections, each with its own heating and cooling mechanisms.
Screw Elements: Inside the barrel, a rotating screw auger conveys the raw materials forward while also applying pressure and shearing forces to facilitate the extrusion process. The design and configuration of the screw elements play a critical role in controlling the flow and texture of the final product.
Die Assembly: At the end of the barrel, the extruded corn mixture passes through a die assembly, which shapes the snack into its final form. Dies can vary in design, allowing for the production of different shapes and sizes of corn puffs.
Control Systems: Modern corn puffs machines are equipped with advanced control systems that monitor and adjust various parameters such as temperature, pressure, and screw speed in real-time. These systems ensure consistent product quality and production efficiency.
Understanding the working principle and composition of corn puffs machines provides valuable insights into their role in snack food production. With their ability to produce a wide range of corn-based snacks efficiently, these machines continue to be indispensable in the food processing industry.
Advantages of corn puff machine
1. Versatility |
- Corn puff machines are highly versatile and can process various types of grains, including corn, rice, wheat, and more. |
2. Customization |
- These machines offer customization options, allowing manufacturers to create a wide range of snack products with different shapes, sizes, and flavors. |
3. Efficiency |
- Corn puff machines are highly efficient, capable of producing large quantities of snacks in a relatively short period. |
4. Cost-Effectiveness |
- With their high production capacity and minimal material wastage, corn puff machines offer a cost-effective solution for snack production. |
5. Consistency |
- These machines ensure consistent product quality, with precise control over parameters such as temperature, pressure, and extrusion rate. |
6. Hygiene and Safety |
- Corn puff machines are designed with hygiene and safety in mind, featuring easy-to-clean surfaces and robust safety mechanisms to prevent accidents. |
7. Automation |
- Many modern corn puff machines are equipped with advanced automation features, reducing the need for manual intervention and enhancing productivity. |
8. Energy Efficiency |
- Efforts are made to design corn puff machines that are energy-efficient, minimizing energy consumption and operational costs. |
9. Innovation |
- Constant innovation in corn puff machine technology leads to the development of new features and capabilities, keeping manufacturers at the forefront of snack production. |
10. Market Demand |
- With the growing demand for snack foods worldwide, the corn puff machine plays a crucial role in meeting consumer preferences and market trends. |
Technical innovation of corn puff machine
1. Improved Extrusion Technology
Extruder Design: Manufacturers have introduced enhanced extruder designs, incorporating features such as adjustable screw configurations and precision control systems.
Efficiency: Modern corn puff machines boast improved efficiency, with higher throughput rates and reduced energy consumption.
Versatility: These machines now offer greater versatility, enabling the production of a wide range of corn puff shapes, sizes, and textures.
2. Enhanced Automation and Control
Automation: Automation has become increasingly prevalent in corn puff machines, streamlining production processes and reducing the need for manual intervention.
Control Systems: Advanced control systems, including PLCs (Programmable Logic Controllers) and HMI (Human-Machine Interface) panels, provide operators with real-time monitoring and precise control over key parameters.
3. Integration of Advanced Materials
Food-Grade Materials: Manufacturers are utilizing high-quality, food-grade materials in the construction of corn puff machines, ensuring product safety and compliance with industry standards.
Wear Resistance: Components subjected to high wear, such as screws and dies, are now fabricated from wear-resistant materials, prolonging machine lifespan and reducing maintenance requirements.
4. Energy-Efficient Solutions
Energy Recovery Systems: Innovative energy recovery systems have been implemented to capture and reuse heat generated during the extrusion process, minimizing energy waste and reducing operating costs.
Optimized Heating Mechanisms: Corn puff machines now feature optimized heating mechanisms, utilizing infrared or induction heating technologies for precise and efficient heat distribution.
5. Enhanced Product Quality
Consistency: Through advancements in process control and material handling, modern corn puff machines ensure greater product consistency, minimizing variations in taste, texture, and appearance.
Quality Assurance: Integrated quality assurance systems monitor key parameters throughout the production process, identifying and rectifying deviations to maintain product quality standards.
The Importance of Quality Control in Corn Puffs Machine Operations
Quality control is paramount in the operation of corn puffs machines, ensuring that the final products meet the highest standards of safety, consistency, and consumer satisfaction. Here's why quality control is essential in this context:
1. Consistency and Uniformity: Quality control measures guarantee that every batch of corn puffs produced by the machine maintains consistent quality and uniformity in terms of size, shape, texture, and flavor. This consistency is crucial for building brand reputation and customer trust.
2. Safety Compliance: Rigorous quality control protocols help ensure that the corn puffs adhere to all safety regulations and standards set by regulatory authorities. This includes monitoring factors such as ingredient sourcing, processing conditions, and packaging to prevent contamination and ensure product safety.
3. Cost Efficiency: Implementing effective quality control procedures can help identify and rectify issues early in the production process, minimizing the risk of product defects, rejections, and wastage. This ultimately contributes to cost efficiency and maximizes the profitability of corn puffs manufacturing operations.
4. Customer Satisfaction: By maintaining high-quality standards, corn puffs manufacturers can consistently deliver products that meet or exceed customer expectations. This leads to greater customer satisfaction, loyalty, and repeat business, ultimately driving revenue growth and market success.
5. Brand Reputation: Quality control plays a significant role in safeguarding the brand reputation of corn puffs manufacturers. Consistently delivering superior-quality products reinforces the brand's image as a trusted provider of delicious and safe snacks, enhancing its competitive position in the market.
6. Continuous Improvement: Quality control processes also serve as a foundation for continuous improvement initiatives. By collecting and analyzing data related to product quality and performance, manufacturers can identify areas for optimization and innovation, driving ongoing enhancements in product quality and operational efficiency.
Sustainability and Environmental Impact
In recent years, the food industry has been increasingly focused on sustainability and reducing its environmental footprint. The same applies to the manufacturing of corn puffs machines. Let's delve into the sustainability efforts and environmental impact associated with these machines.
Sustainable Materials:
One key aspect of sustainability in the manufacturing of corn puffs machines is the choice of materials. Manufacturers are opting for eco-friendly materials, such as recyclable metals and biodegradable plastics, in the construction of these machines. This not only reduces environmental impact but also promotes a circular economy.
Energy Efficiency:
Another crucial factor is the energy efficiency of corn puffs machines. Manufacturers are continually striving to improve the energy efficiency of their equipment, utilizing advanced technologies and design modifications to minimize energy consumption during operation. This not only lowers operational costs but also reduces greenhouse gas emissions associated with energy production.
Waste Reduction:
Efforts to minimize waste generation are also paramount. Manufacturers are implementing innovative waste management systems to reduce, reuse, and recycle materials throughout the production process. By optimizing material usage and minimizing waste sent to landfills, the environmental impact of corn puffs machine manufacturing is significantly reduced.
Emissions Control:
Controlling emissions is essential for mitigating the environmental impact of manufacturing operations. Corn puffs machine manufacturers are implementing measures to minimize air and water emissions, such as installing pollution control devices and adhering to strict environmental regulations. By reducing emissions, these manufacturers contribute to cleaner air and waterways.
Supply Chain Sustainability:
Sustainability efforts extend beyond the manufacturing process to the entire supply chain. Corn puffs machine manufacturers are partnering with suppliers who share their commitment to sustainability, ensuring that raw materials are sourced responsibly and ethically. This promotes transparency and accountability throughout the supply chain.
Post-maintenance guide
1. Cleanliness is Key
Regular Cleaning: After each use, thoroughly clean the machine, including the hopper, extruder, and cutting mechanisms, to remove any residual corn mixture.
Deep Cleaning: Periodically, disassemble the machine for a deep clean, paying attention to hard-to-reach areas where food particles may accumulate.
2. Inspection and Lubrication
Routine Inspection: Regularly inspect the machine for signs of wear, damage, or loose components. Address any issues promptly to prevent further damage.
Lubrication: Apply lubricant to moving parts as per the manufacturer's recommendations to maintain smooth operation and prevent friction-related damage.
3. Calibration and Adjustment
Calibration: Check and calibrate temperature, pressure, and speed settings to ensure consistency in puffing quality.
Adjustment: Fine-tune the machine settings based on the type and condition of the corn mixture to achieve the desired puffing results.
4. Safety Checks
Electrical Safety: Inspect electrical connections and wiring for signs of wear or damage. Replace any frayed wires or malfunctioning components promptly.
Operational Safety: Remind operators to follow safety protocols and use protective equipment to prevent accidents during machine operation.
5. Record-Keeping
Maintenance Log: Maintain a detailed maintenance log, documenting each cleaning, inspection, and repair performed on the machine. This log helps track maintenance history and identifies recurring issues.
6. Professional Servicing
Scheduled Servicing: Arrange for professional servicing at regular intervals, as recommended by the manufacturer, to address any technical issues and ensure compliance with safety standards.
Training and Education: Provide ongoing training to machine operators on proper maintenance procedures and safety protocols to maximize efficiency and minimize downtime.
By following these post-maintenance guidelines diligently, you can prolong the lifespan of your corn puffs machine and maintain consistent product quality, ensuring continued success in your snack food production endeavors.
Conclusion
In conclusion, the corn puffs machine stands as a cornerstone in the landscape of food processing machinery, particularly within the realm of snack production. Its innovative design and robust capabilities allow for the efficient and reliable production of corn-based puff snacks, meeting the demands of consumers worldwide.
Technological advancements continue to drive the evolution of corn puffs machines, with continuous improvements enhancing efficiency, productivity, and product quality. As market trends and consumer preferences evolve, manufacturers are poised to capitalize on emerging opportunities, ensuring that the corn puffs machine remains at the forefront of snack food production.
With a keen focus on quality control and assurance, manufacturers uphold stringent standards throughout the production process, safeguarding the integrity and safety of the final product. Sustainability considerations also play a pivotal role, as industry stakeholders strive to minimize environmental impact and promote eco-friendly practices.
Looking ahead, the future of corn puffs machines is promising, with ongoing research and development paving the way for further innovation. As we navigate the complexities of the food industry, the corn puffs machine remains an indispensable tool, driving growth, and innovation in the snack food sector.
Reference
1. Food Processing:
Website: [Food Processing](https://www.foodprocessing.com/)
2. Food Engineering:
Website: [Food Engineering](https://www.foodengineeringmag.com/)
3. Process Industry Forum:
Website: [Process Industry Forum](https://www.processindustryforum.com/)
4. Food Manufacture:
Website: [Food Manufacture](https://www.foodmanufacture.co.uk/)