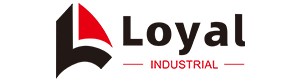
- Shandong Loyal Industrial Co.,Ltd.
- Macaroni Production Machine Instant Noodle Machine Biscuit Making Machine

Home> Company News> The Ultimate Guide to Snack Food Equipment in 2024

The Ultimate Guide to Snack Food Equipment in 2024
2024-04-22 16:38:49Introduction
Welcome to the ultimate guide to snack food equipment in 2024. In this comprehensive overview, we will delve into the world of snack food equipment, exploring its significance in the food processing industry and its role in shaping the future of snack production.
Snack food equipment encompasses a wide range of machinery and tools used in the manufacturing of various snack products. From extruders and fryers to packaging machines and quality control systems, these equipment play a crucial role in ensuring the efficiency, consistency, and quality of snack production processes.
Throughout this guide, we will discuss the key components and functions of snack food equipment, examine the latest technological advancements and market trends, and highlight the importance of quality control and sustainability practices in snack food manufacturing.
Whether you're a seasoned industry professional or a newcomer to the world of snack production, this guide aims to provide valuable insights and knowledge to help you navigate the complexities of snack food equipment in 2024. So, let's dive in and explore the fascinating world of snack food machinery together.
The Work Process of Snack Food Equipment
Snack food equipment plays a pivotal role in the efficient production of a wide range of snack products. Here's a concise overview of the work process involved in snack food equipment:
1. Ingredient Preparation:
The process begins with the preparation of ingredients. These may include grains, cereals, pulses, flavorings, and additives. Ingredients are carefully measured and mixed according to the desired recipe.
2. Mixing and Blending:
Once the ingredients are prepared, they are fed into the mixing and blending section of the equipment. Here, they are thoroughly combined to ensure uniform distribution of flavors and nutrients.
3. Extrusion or Forming:
The mixed ingredients are then passed through an extrusion or forming mechanism, depending on the type of snack being produced. Extrusion involves forcing the mixture through a die to create a specific shape, while forming involves molding the mixture into shape using molds or dies.
4. Cooking or Baking:
After extrusion or forming, the snacks undergo cooking or baking. This step is crucial for achieving the desired texture, flavor, and crispness. Cooking methods may include frying, baking, or toasting, depending on the product.
5. Seasoning and Coating:
Once cooked, the snacks are seasoned and coated to enhance their taste and appearance. Seasonings such as salt, spices, cheese powder, or sugar are applied to the snacks while they are still warm to ensure proper adhesion.
6. Cooling and Packaging:
After seasoning, the snacks are cooled to room temperature to prevent moisture buildup and ensure crispiness. Finally, the snacks are packaged in suitable containers, which may include bags, boxes, or pouches, ready for distribution and consumption.
Advantages of snack equipment
Advantages |
Description |
1. Versatility |
Snack food equipment offers versatility in processing various ingredients, allowing for the production of a wide range of snack products such as chips, extruded snacks, popcorn, and more. |
2. Efficiency |
Snack equipment is designed for high efficiency, enabling continuous production with minimal downtime. Advanced automation and control systems optimize the production process, reducing labor costs and increasing output. |
3. Customization |
Modern snack food equipment allows for customizable product attributes, including shape, size, texture, and flavor. Manufacturers can adjust processing parameters to meet consumer preferences and market demands, providing a competitive edge. |
4. Consistency |
With precise control over processing parameters, snack equipment ensures consistency in product quality and characteristics. This consistency is essential for building consumer trust and brand reputation. |
5. Hygiene and Safety |
Snack equipment is designed with hygiene and safety in mind, featuring easy-to-clean surfaces, sanitary design principles, and integrated safety features to minimize the risk of contamination and ensure compliance with food safety regulations. |
6. Cost-effectiveness |
Investing in snack food equipment can result in long-term cost savings due to increased production efficiency, reduced labor costs, and minimized product waste. Over time, the return on investment (ROI) of the equipment becomes apparent, contributing to business profitability. |
7. Innovation and Technology Integration |
Advancements in snack equipment technology continue to drive innovation in the industry. Integration with cutting-edge technologies such as artificial intelligence (AI), Internet of Things (IoT), and data analytics enhances equipment performance and productivity. |
8. Sustainability |
Many modern snack food equipment manufacturers prioritize sustainability by implementing energy-efficient processes, reducing water consumption, and utilizing eco-friendly materials. Sustainable practices not only benefit the environment but also appeal to environmentally conscious consumers. |
9. Scalability |
Snack equipment offers scalability to accommodate growing production demands. Manufacturers can easily expand production capacity by adding additional equipment or upgrading existing systems, allowing for seamless business growth and adaptation to market changes. |
10. Support and Service |
Reputable snack equipment suppliers provide comprehensive support and service, including installation, training, maintenance, and troubleshooting. Reliable customer service ensures smooth equipment operation and minimizes disruptions to production. |
Technological innovation of snack equipment
1. Automated Production Lines
Advancements in automation technology have led to the development of highly efficient snack food production lines.
Automated equipment such as conveyor systems, robotic arms, and packaging machines streamline the production process, reducing manual labor and increasing output.
2. Precision Control Systems
Modern snack food equipment is equipped with advanced control systems that offer precise control over various parameters such as temperature, pressure, and speed.
These control systems ensure consistent product quality and minimize wastage by optimizing process parameters in real-time.
3. Integrated Processing Solutions
Snack food equipment manufacturers are increasingly offering integrated processing solutions that combine multiple unit operations into a single system.
Integrated solutions optimize space utilization, reduce production footprint, and simplify maintenance and operation.
4. Energy-Efficient Designs
Energy efficiency is a key focus area in the development of snack food equipment, driven by sustainability concerns and cost-saving initiatives.
Equipment designs incorporate energy-efficient components, such as high-efficiency motors, insulation materials, and heat recovery systems, to minimize energy consumption.
5. Digitalization and Connectivity
Snack food equipment is becoming increasingly interconnected through the adoption of digitalization and IoT (Internet of Things) technologies.
IoT-enabled equipment allows for remote monitoring, predictive maintenance, and real-time performance optimization, improving overall equipment effectiveness (OEE).
6. Hygienic Design Standards
With growing emphasis on food safety and hygiene, snack food equipment manufacturers adhere to stringent hygienic design standards.
Equipment features sanitary designs, smooth surfaces, and easy-to-clean components to minimize the risk of contamination and ensure compliance with food safety regulations.
7. Customization and Flexibility
Manufacturers are offering customizable snack food equipment solutions to meet the diverse needs of customers and accommodate changes in product formulations and packaging formats.
Flexible equipment designs allow for quick changeovers between different product lines, reducing downtime and increasing production flexibility.
Market Trends
Several notable market trends are driving the demand for snack food equipment in 2024:
Health and Wellness: With an increasing focus on health-conscious consumption, there is a growing demand for snack foods that offer nutritional benefits. Snack food equipment is being used to produce healthier alternatives, such as baked snacks, vegetable chips, and protein-rich bars.
Convenience: Busy lifestyles and on-the-go consumption continue to fuel the demand for convenient snack options. Snack food equipment is optimized for efficiency and speed, allowing manufacturers to meet the need for convenient, grab-and-go snacks.
Customization: Consumer preferences are becoming more diverse and personalized. Snack food equipment with customizable features enables manufacturers to create unique flavor profiles, textures, and shapes tailored to specific target markets.
Sustainability: Environmental consciousness is driving the adoption of sustainable practices in snack food production. Equipment manufacturers are incorporating eco-friendly materials and energy-efficient processes to minimize environmental impact.
Importance of quality control
Snack food equipment plays a crucial role in the food processing industry, facilitating the production of a wide range of snacks enjoyed by consumers worldwide. Quality control is paramount in ensuring that these snacks meet the highest standards of safety, consistency, and taste. Let's delve into the importance of quality control in snack food equipment:
1. Ensuring Product Safety
Quality control measures are essential for ensuring that snack food equipment meets stringent safety standards. This includes verifying that equipment components are made from food-grade materials and undergo thorough sanitation procedures to prevent contamination.
2. Maintaining Consistency
Consistency is key in snack food production to deliver uniform products with consistent taste, texture, and appearance. Quality control processes help monitor and maintain parameters such as temperature, pressure, and moisture levels to achieve desired product characteristics.
3. Meeting Regulatory Requirements
Compliance with regulatory requirements is non-negotiable in the food industry. Quality control ensures that snack food equipment adheres to relevant regulations and standards, including those related to food safety, labeling, and packaging.
4. Enhancing Brand Reputation
A commitment to quality control reflects positively on a brand's reputation. Consistently delivering high-quality snacks builds trust and loyalty among consumers, leading to repeat purchases and positive word-of-mouth recommendations.
5. Minimizing Product Waste
Quality control measures help identify and address issues early in the production process, reducing the risk of producing substandard or defective products. This minimizes product waste and optimizes production efficiency.
6. Improving Customer Satisfaction
Ultimately, quality control contributes to customer satisfaction by ensuring that snack food equipment produces snacks that meet or exceed consumer expectations. Consistently delivering high-quality products enhances brand loyalty and fosters long-term customer relationships.
Comparison table between loyal and FEN companies
Aspect |
Loyal |
FEN |
Product Range |
Specializes in snack food machinery, including extruders, fryers, and packaging equipment. |
Offers a diverse range of industrial food processing equipment, including mixers, ovens, and conveyors. |
Technology Innovation |
Known for incorporating advanced technologies, such as PLC systems and automation, to enhance production efficiency and product quality. |
Focuses on innovative solutions, leveraging state-of-the-art technology for improved performance and reliability. |
Customization Options |
Offers extensive customization options to meet specific client requirements, with flexible configurations and design features. |
Provides tailored solutions tailored to client needs, offering customizable features and configurations for enhanced functionality. |
Industry Experience |
Boasts extensive experience in the snack food industry, with a proven track record of delivering high-quality machinery solutions to global clients. |
Established reputation in the industrial food processing sector, with a history of successful projects and satisfied customers. |
After-Sales Support |
Provides comprehensive after-sales support, including installation, training, and maintenance services, to ensure optimal performance and customer satisfaction. |
Offers dedicated customer support services, including technical assistance, spare parts availability, and troubleshooting guidance. |
Global Presence |
Operates a global network of sales and service centers, catering to clients worldwide and offering localized support and expertise. |
Maintains a strong international presence, with a network of distributors and partners ensuring seamless delivery and support services across regions. |
Sustainability and environmental impact
1. Sustainable Manufacturing Practices
Sustainable manufacturing practices have become increasingly important in the food industry. Snack food equipment manufacturers are embracing sustainable initiatives to reduce environmental impact. These practices include:
Energy-efficient designs: Snack food equipment manufacturers are integrating energy-efficient technologies into their machinery to minimize energy consumption during production processes.
Waste reduction strategies: Innovative equipment designs aim to minimize waste generation by optimizing material usage and reducing production inefficiencies.
Recycling and reuse: Manufacturers are incorporating recyclable materials into equipment construction and implementing recycling programs for end-of-life equipment components.
2. Environmental Impact Reduction
Snack food equipment plays a crucial role in reducing the environmental impact of snack food production. Advancements in equipment design and technology contribute to:
Lower carbon emissions: Modern snack food equipment utilizes cleaner energy sources and implements emission-reduction technologies to minimize carbon footprint.
Water conservation: Equipment designs prioritize water conservation by implementing efficient water usage systems and recycling wastewater for non-potable applications.
Sustainable packaging solutions: Snack food equipment manufacturers collaborate with packaging companies to develop eco-friendly packaging solutions, reducing plastic usage and promoting biodegradability.
3. Compliance with Regulatory Standards
Snack food equipment manufacturers adhere to stringent regulatory standards to ensure environmental compliance and food safety. Key considerations include:
Regulatory certifications: Equipment manufacturers obtain certifications such as ISO 14001 for environmental management systems and adhere to food safety standards such as HACCP.
Continuous improvement: Manufacturers engage in continuous improvement processes to enhance equipment performance, safety, and environmental sustainability.
4. Industry Collaboration and Innovation
Collaboration between equipment manufacturers, food producers, and regulatory agencies drives innovation in sustainable snack food equipment. Key initiatives include:
Research and development: Investment in research and development leads to the development of advanced equipment technologies that prioritize sustainability without compromising performance.
Industry partnerships: Collaborative efforts between equipment manufacturers and food producers result in the co-creation of sustainable equipment solutions tailored to specific production needs.
Post-maintenance guide
Equipment Component |
Maintenance Task |
Remarks |
Hoppers |
Cleaning and sanitization |
Ensure removal of any residues |
Conveyors |
Lubrication |
Use food-grade lubricants |
Mixers |
Inspection for wear and tear |
Replace worn parts as necessary |
Extruders |
Calibration and alignment |
Ensure consistent product quality |
Fryers |
Oil filtration and replenishment |
Monitor oil quality regularly |
Packaging Machinery |
Testing for sealing integrity |
Prevents product contamination |
Reference
1. Food Processing:
Website: [Food Processing](https://www.foodprocessing.com/)
2. Food Engineering:
Website: [Food Engineering](https://www.foodengineeringmag.com/)
3. Process Industry Forum:
Website: [Process Industry Forum](https://www.processindustryforum.com/)
4. Food Manufacture:
Website: [Food Manufacture](https://www.foodmanufacture.co.uk/)