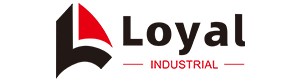
- Shandong Loyal Industrial Co.,Ltd.
- Macaroni Production Machine Instant Noodle Machine Biscuit Making Machine

Home> Company News> What Is Nutrition Bar Production Line

What Is Nutrition Bar Production Line
2023-06-25 14:02:20Nutrition bar production line refers to a set of mechanical equipment for mass production of nutrition bars. The line typically consists of multiple stages, including mixing and processing of ingredients, shaping and shaping of chocolate bars, baking or drying, and packaging for distribution. A production line can include various machines such as mixers, extruders, ovens, cooling tunnels, cutting and wrapping machines, and packaging equipment. These machines are designed to efficiently and accurately produce large quantities of nutritional bars. Some production lines are fully automated, while others may require some human intervention at certain stages. The line may also employ quality control measures such as inspection systems to check for size, shape and texture consistency, and metal detectors to ensure product safety. Using a nutritional bar production line allows manufacturers to streamline production processes, increase efficiency and maintain consistent quality. It also enables them to meet high demand and produce large volumes of nutrition bars to supply retailers and customers.
Flow Chart Of Nutrition Bar Production Line
- Puffing —— 2. Drying —— 3. Sugar Boiled Pot —— 4. Oil Sugar Electromagnetic Insulation Pot —— 5. Electromagnetic Sugar Cooker —— 6. Weighing Feeder —— 7. Temperature Control Mixer —— 8. Hoist —— 9.Automatic Cutting Machine —— 10.Cooling —— 11.Auto Packing
Functions Of Nutrition Bar Production Line
- Ingredients Mixing And Processing: The production line includes machines for mixing and processing different ingredients such as grains, nuts, seeds, sweeteners, protein powders and condiments. These machines ensure thorough mixing and homogeneity of ingredients.
- Forming And Forming: After the ingredients are mixed, they need to be formed into strips. The line includes machines that can shape the mixture into different shapes, such as bars, rectangles or squares. These machines ensure consistent and precise molding.
- Roasting Or Drying: Depending on the type of nutrition bar, it may need to be roasted or dried. The production line includes ovens or drying tunnels with controlled temperature and airflow to evenly roast or dry the sticks. This step helps enhance flavor, texture and extend shelf life.
- Cooling: After the rod is baked or dried, it needs to be cooled before further processing or packaging. Lines include cooling tunnels or conveyor belts that gradually cool the bars to prevent damage or deformation.
- Cutting And Winding: After cooling, the rod is usually cut into the required size or specification. The line includes machines that can precisely cut rebar without affecting its shape or integrity. Thereafter, the chocolate bars are individually wrapped or wrapped to keep them fresh and easy to handle.
- Packing And Labeling: The production line includes packing machines that can efficiently pack gold bars into various forms such as individual wrappers, boxes or bulk packs. It also includes labeling machines for applying labels with product information, nutrition facts, barcodes and expiration dates.
- Quality Control And Inspection: Throughout the production line, various quality control measures can be integrated. This may include inspection systems to ensure consistent bar size, shape and texture, and metal detectors to detect any metallic contamination.
- Automation And High Efficiency: The nutrition bar production line is designed to realize the automation of each process, ensuring high production efficiency and reducing labor. Automation helps maintain consistency, increase productivity and minimize production errors.
By incorporating these capabilities into a line of nutritional bars, manufacturers can mass-produce high-quality and consistent nutritional bars that effectively meet the needs of consumers and retailers.
Advantages Of Nutrition Bar Production Line
Increase Production Capacity |
The nutrition bar production line can realize large-scale production, and the overall production capacity is significantly improved compared with manual methods. This enables manufacturers to efficiently meet the rising demand for nutritional bars. |
Consistency Of Product Quality |
The automation and standardization of the production line process ensures the consistency of the quality of nutrition bars. With precise control over ingredients, blending, shaping, baking and packaging, manufacturers can achieve consistency in taste, texture and appearance from batch to batch. |
Improve Efficiency And Cost-Effectiveness |
Automation reduces the dependence on human labor, thereby increasing production efficiency and reducing labor costs. The line simplifies the process and eliminates bottlenecks, reducing overall production time and unit cost. |
Strengthen Food Safety |
The nutrition bar production line adopts various measures to ensure food safety. The use of automated processes minimizes human contact and reduces the risk of contamination. Additionally, quality control measures such as metal detectors and inspection systems help identify and eliminate potential hazards. |
Customization Options |
The production line is flexible enough to accommodate different formulas and nutritional bar changes. Manufacturers can easily adjust ingredient ratios, shapes, sizes and packaging formats to meet specific customer preferences or market demands. |
Extended Shelf Life |
The controlled baking or drying process in the production line helps to extend the shelf life of nutrition bars. Properly baked or dried chocolate bars can reduce moisture content, which inhibits microbial growth and improves product stability. |
Scalability And Growth Potential |
Investing in a nutritional bar production line presents an opportunity for business scalability. As demand increases, manufacturers can easily expand capacity by adding additional machines or production lines, thereby capitalizing on market growth opportunities. |
Save Time And Resources |
By automating processes, manufacturers can save time and resources that would otherwise be spent on manual labor. The line optimizes workflow, reduces waste, and minimizes human error, resulting in increased productivity and cost savings. |
Overall, a nutritional bar production line offers many advantages, including increased capacity, consistent product quality, efficiency, customization options, food safety, extended shelf life, scalability, and resource savings. These advantages help nutritional bar manufacturers succeed and increase profitability in a highly competitive market.
Performance And Other Instructions
A. The food contact location is made of stainless steel 304 material, which meets the food QS and pharmaceutical GMP hygiene requirements.
B. Double frequency conversion system control, bag length is set and cut immediately, saving time and film.
C. High-sensitivity electric eye automatic tracking, no need to manually adjust after setting, sealing and cutting size, accurate position, strong and beautiful sealing.
D. Temperature independent PID intelligent control, stable temperature control, better suitable for various packaging materials.
E. Color touch screen display, positioning shutdown, automatic fault diagnosis, the display is clear at a glance.
F. Intelligent human nature parameter design, ordinary personnel can use it skillfully in a short time. Reduce the professional skills requirements of operators.
G. A variety of cutting packaging shapes: straight, popcorn, corrugated, continuous bag, etc.
H. Suitable for moon cakes, bread, biscuits, candies, medicines, daily necessities, hardware parts, paper boxes, plastic products or all kinds of solid objects with regular shapes.