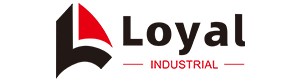
- Shandong Loyal Industrial Co.,Ltd.
- Macaroni Production Machine Instant Noodle Machine Biscuit Making Machine

Home> Processing> What Is The Operating Procedure Of Pet Food Extruder?

What Is The Operating Procedure Of Pet Food Extruder?
2021-01-12 14:55:23Pet food can be broadly divided into dry food and wet food. Among them, dry pet food is usually made by twin-screw extruder. The most common method is to pulverize raw materials such as grains and animal by-products and enter the extruder for extruding.
Pet food can be broadly divided into dry food and wet food. Among them, dry pet food is usually made by twin-screw extruder. The most common method is to pulverize raw materials such as grains and animal by-products and enter the extruder for extruding. The steam and water injected during the pressing process, and finally the drying material is sprayed with grease and protein digestion or flavoring substances to enhance the pet’s acceptance of food.
Dry pet food process:
Mixing of raw and auxiliary materials →primary crushing--secondary crushing →extruder extrusion → drying machine drying → spraying grease and flavoring agent → finished product
Extrusion is a very important part of the current dry pet food production and processing process. Today I will share with you the operating procedures of the pet food puffing machine.
Introduction of extruder:
The puffing machine is a kind of equipment for processing puffed food. Its main working principle is to convert mechanical energy into heat energy. The heat generated when the machine rotates is used to squeeze and cook the food. The most obvious feature of the puffed food is its larger volume.
Operating procedures of extruder:
(1). Check before starting
1. Check all parts, especially the connecting bolts and anchor bolts of each section of the expansion cavity, the connection bolts between the motor base and the frame, and the connection bolts between the expansion cavity and the base. There must be no looseness.
2. Manually rotate the main shaft to make it rotate. At this time, there should be no rubbing sound in the puffing cavity. If there is rubbing sound, it needs to be adjusted.
3. Confirm that the oil level of the main engine gearbox is within the normal range.
4. Make sure that the water level in the water tank is sufficient and the water pump pipe valve is opened to the correct position.
5. Check whether the liquid level of the grease addition tank is sufficient, and the valve of the liquid addition pipeline is opened to the correct position.
(2). Preparation before starting
1. Start the water pump, adjust the return ball valve, and adjust the pressure reducing valve.
2. Check the steam pressure of the steam drum of the pipe rack, remove the condensed water in the steam system, and open the steam trap of the pipe rack.
3. Check the pressure of the compressed air, and move the pneumatic valves to confirm the normal response.
4. Install the template, tighten the bolts evenly and firmly, check whether the cutter is neat and firm, connect the cutting device with the template, lock the four locks, adjust the distance between the blade and the template to make it evenly close to the template, lock the adjustment wheel, and close Make the two-sided access door and connect the socket cable of the cutting device.
5. Set the jacket temperature and turn on the jacket to automatically keep warm.
6. Open the conditioner and check whether there is any abnormality in the blades, whether there is a large accumulation of material, and there should be no accumulation of material on the inner wall of the feed opening.
7. According to the liquid addition ratio and its equivalent displayed on the touch screen of the extruder, calculate the preset frequency of the refueling pump and enter it in the “set frequency”.
(3). Boot operation process
1. Start the feeding auger of the feeding bin to feed.
2. The discharge port is bypassed, the feeding auger and the motor are started in turn, the moisture exhaust fan and the air shutter are started, when the bypassed powder flows out, the steam and water are turned on for conditioning, and the grease adding pump is started.
3. Turn on the gear box oil pump motor, turn on the cooling circulating water, and start the host.
4. When the quenching and tempering meets the requirements, the speed of the main engine is increased, and the cutter motor is started. When the speed of the main engine is in place, the bypass is closed and the material is fed into the expansion cavity.
5. Observe the shape and moisture of the discharged material, monitor the degree of expansion and bulk density, adjust the steam and water, adjust the frequency of the cutter, and the frequency of the main machine to make the product meet the requirements and stabilize the production.
6. Record production parameters, continuously monitor the discharge status, and adjust in time.
(4). Shutdown operation process
1. Switch the control mode, all the parameter control modes in the interface are switched from “automatic” to “manual”.
2. The temperature control of the jacket is switched from “automatic” to “manual”, and the jacket heat preservation is stopped.
3. Stop feeding the auger motor.
4. Turn off the grease adding pump, close the steam pneumatic valve, set the steam proportional valve opening to “0’, close the water tank pump and spray solenoid valve, and set the water proportional valve opening to “0”.
5. The conditioner is turned on by-pass, and when the current of the main machine is proper, the frequency of the main machine is reduced to “0”, then the main motor is turned off, and the cutter motor is turned off.
6. Turn off the air supply motor and the air shutter, and turn off the moisture exhaust fan and the air shutter.
7. Disassemble the mold, clean the template, pour into the washing machine water, clean the puffing cavity, clean the inner wall and the discharge port.